EXCON gains speed and precision with the XPR300
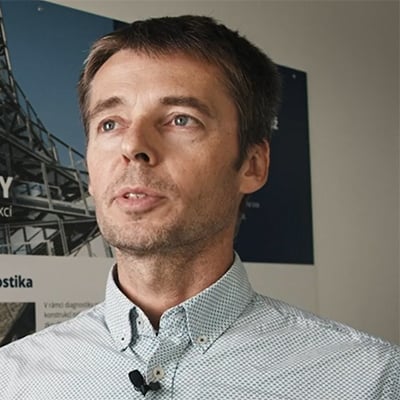
“We have been using our automatic lines for about four months now. They meet our expectations in terms of speed and precision in the production of individual items, whether sheet metal or profile items. Thanks to these automatic machines we are also able to increase the capacity to our desired target of 300 tons of production per month.”
Miloslav Lukeš
Technical Director, EXCON
Company overview
EXCON is primarily and traditionally engaged in the business of steel structures. The company began operations in 1990 as a design studio specializing in the structural analysis and dynamics of steel structures. In early 1995, it expanded its activities to include engineering and contracting. Following the introduction of new standards for inspections and maintenance of steel structures, which EXCON helped author, it is rolling out structure diagnostic services. EXCON is located in the Czech Republic.
EXCON provides the complete execution of steel structures from design through production to assembly. At its Prague branch, the company focuses on the design of steel structures. Data in the Prague office is sent to EXCON’s production location in Teplice, where the data is entered into the machines and the actual production occurs. The final products are welded structures for a wide range of steel buildings, from sports facilities to technology structures to powerplants and more.
Challenge: The company needed to increase capacity and accuracy of production
In order to increase the capacity and accuracy of the company’s production, EXCON acquired two automatic lines. One line is for sheet metal production and the other is for profile production, enabling EXCON to produce precision welded parts. During production, the company uses all of the capabilities of the new lines, including drilling, precise shape cutting, and marking individual items. All of this is useful for effective, fast assembly of welded pieces.
To tackle the problem of not having enough qualified workers, EXCON decided to include a robotic beam cutting workplace in its automatic line. The company had a goal to increase the capacity and quality of its production, and the EXCON team decided they needed automatic preparation of items to meet this goal. They started to search for an automatic line that would fit their needs.
Solution: Voortman machine with XPR300 enables increased capacity and accuracy
It took EXCON about three years to map out the European market, and the team visited several companies. Finally, after considering the technical parameters, price, service offer, and options for fully automatic material transport, they decided on machines from Voortman, a global leader in creating CNC steel processing machinery, with the Hypertherm® XPR300® plasma cutting system.
The XPR300
The XPR300 represents a significant advancement in mechanized plasma cutting technology, redefining what plasma can do by expanding its capabilities and opportunities in ways never before possible. The XPR300 blends new technology with refined processes for next-generation, X-Definition® cutting that delivers unmatched cut quality on mild steel, stainless steel, and aluminum.
The XPR300 delivers increased cut speed, dramatically improved productivity and a significant reduction in operating costs. In addition, new ease-of-use features and engineered system optimization make the system easier to run with minimal operator intervention, while also ensuring optimal performance and reliability.
Benefits of the system include:
-
Improved cut quality on thin mild steel, with consistent ISO range 2 results
-
Extended ISO range 3 cut quality results compared with earlier plasma technology
-
Superior stainless steel cut quality across all thickness ranges
-
Increased cut speeds on thicker materials
-
Thicker piercing capability than with competitive plasma systems
-
Consumable life that is three times longer than consumable life in competitive plasma systems
-
Lower energy costs with 62% higher power-to-weight ratio and 14% faster cuts
The XPR300’s advanced power supply technology delivers highly responsive, rapid system feedback and automatically intervenes to eliminate events that negatively impact system efficiency and consumable life. Arc response technologyTM provides automatic torch and ramp-down error protection to increase the life of the torch and consumables.
Sensors in the power supply deliver refined diagnostic codes and enhanced system monitoring information to reduce troubleshooting time and provide proactive system maintenance data for improved system optimization. These enhancements eliminate the impact of ramp-down errors and increase consumable life to up to three times longer than that of competitive systems. They also reduce the impact of catastrophic electrode blowouts which can damage the torch at high current levels.
Intuitive controls and operation, together with automatic monitoring, make the system easy to use, even for new operators. Training is faster, and seasoned operators deliver better cut quality more efficiently. Full control of all functions and settings is available via the CNC, and automatic system monitoring and specific troubleshooting codes improve maintenance and service. Wi-Fi in the power supply connects to mobile devices and LAN for multiple system monitoring and service.
Both consumable and torch changes are easier as well. The XPR300’s EasyConnect™ torch lead and one hand torch-to-receptacle connection enable fast and easy change-outs, and the system’s QuickLock™ electrode makes consumable replacement easy.
Business impact: Higher cut speed and quality increase production capacity
The new automatic plasma cutting system’s higher cut speed and higher-quality cuts increased production capacity for EXCON. Plasma marking and high precision allow for fast assembly of welded parts, increasing production even further.
The system’s increased reliability means EXCON spends less time on maintenance, with long intervals between required service. This enables workers to focus more on production and less on maintaining machines. The EXCON team explains, “The accuracy of the items is good; they are in accordance with our standards. The regular maintenance is there for sure, like with every machine, but it’s not as much work as with other machines. Other than that, there are rather long maintenance intervals.”
Overall, the EXCON team is very happy with the Hypertherm XPR300 and they would purchase another Hypertherm system if they needed to expand production further.
Learn how the XPR300 can help your business strike the perfect balance between cut quality, cut speed, and cost. Click the button below, fill out the form, and a Hypertherm product expert will contact you.