Lazer toleransları: mühendisler bunları belirleyebilir ancak gerçek bir ihtiyaç durumu yoksa size sadece masraf çıkmış olur!
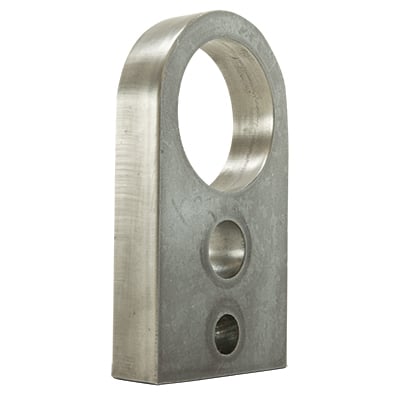
Lazer de, plazma da termal işlemle metal keser, ancak bunlar birbirlerinden çok farklı yollarla çalışırlar. Türü ne olursa olsun (CO2 veya fiber), lazerde, elektromanyetik radyasyonun eş değer salınımı ile oluşturulan monokromatik ışığın yoğun, koherent bir ışını kullanılır. Odaklı ışık ışınının avantajlarından biri, bu ışının son derece katı toleranslar kesebilmesidir. İşlemde daha az değişkenlik olur. Genel olarak, lazer, kesim parçasının boyutsal toleranslarını 0,25 mm altında tutabilir.* Öte yandan plazma, olağanüstü yüksek sıcaklıkta enerji odaklaması yapan süper konsantre bir ark oluşturmak amacıyla iyonlaştırma noktasına kadar ısıtılmış olan bir gaz kullanır. Bu, X-Definition® özellikli plazma sistemi kullanıldığında, yaklaşık 0,5 mm’lik kesim parçası boyutsal toleranslar getirir.
Parça toleransları oluşturma ve üretme işleminin teknik özellikleri bakımından, değerlendirilmesi gereken tavizler vardır ve bunlardan biri, gereksiz ölçüde sıkı gereksinimlerin ortaya çıkardığı maliyettir. Yukarıda açıklanan lazer ile plazma toleransları arasındaki farklar sadece sıradan bir kartvizitin kalınlığı kadardır! Bu nedenle, “lazer kalitesini” sorgulamadan veya lazer ekipmanı ve tesiste yeni ekipman yükseltmesi için araştırma yapmaya başlamadan önce kendinize şu soruları sormalısınız: “Bu parçada bu kadar katı toleranslara gerçekten ihtiyacım var mı?”
Katı toleransların gizli maliyetleri
Genel bir kural olarak, katı boyutsal toleranslar üretim işleminizde ve ürününüzde maliyet artışına neden olurlar. Parçanın formu, yapısı veya fonksiyonu gerçekten katı toleranslar kullanılmasını gerektirmiyorsa, bu katı özellikler gereksiz maliyet çıkartarak işleminize yük olacaktır. Bu gereksiz maliyetler kârlılığınızın azalmasına veya şirketinizin rekabette dezavantajlı bir konum edinmesine veya her ikisine birden neden olacaktır!
Gerekenden daha katı toleranslar istemek işleminizde şu şekilde maliyet yaratır:
- Toleransları iletmek için gereken makine aracının satın alma maliyeti. Lazer değil de bir X-Definition, XPR™, plazma sistemi söz konusu olduğunda, farklı yatırım maliyetleri yüz binlerce doları bulabilmektedir. Büyük yatırımlar bir şirketin bilançosunu ve amortisman giderlerini etkileyebilir.
- İnceleme ekipmanı maliyeti. Daha sıkı toleranslar genelde daha yüksek inceleme ekipmanı maliyeti demektir. Toleranslarınız bir mezür veya başka bir basit aletle ölçülebiliyorsa, inceleme ekipmanı maiyetiniz asgari düzeyde olur. Öte yandan, toleranslarınız için daha sofistike bir ölçüm aleti, örneğin bir CMM (Koordinat Ölçüm Makinesi) gerekiyorsa, yatırım masrafınız 120 bin ABD dolarına kadar çıkabilir. Daha da kötüsü, doğru bir şekilde ölçemediğiniz toleranslar belirlerseniz, size gerçek dönüşü olmayacak bir şeye para harcamış olabilirsiniz.
- Ölçüm idaresinin uygulanması için gereken ölçümün sıklığı ve eğitim. Genel olarak, toleranslar katılaştıkça daha sık ölçüm yapmak ve ölçüm ekipmanını kullanmak için daha fazla eğitim almak gerekir. Yukarıdaki örnekte görüldüğü gibi, toleransları bir mezür kullanarak ölçen bir çalışan ile CMM kullanarak ölçen çalışan arasında çok farklı eğitim ve ödeme düzeyleri söz konusudur.
- Hurda. Bir başka maliyet artışı hurda ile bağlantılıdır. Kesim için kullanılan işlem, belirlenen toleransları karşılamada kendini kanıtlamış kapasitede olmalıdır. Becerisi düşükse veya beceri zaman içinde bozuluyorsa, daha yüksek oranda hurda çıkabilir.
- Tedarik zinciri sorunları. Daha yüksek toleransların tanımlanması dış kaynak kullanımı veya uygun tedarikçi bulma olanaklarınızı da sınırlandırabilir. Tedarikçiler arasındaki rekabetin azalması size daha yüksek fiyatlar getirebilir.
- Daha az üretim. Daha katı tolerans gerekliliğinin bedeli daha düşük kesim hızı ve üretim olabilir. Malzeme tipi ve kalınlığına bağlı olarak, sonuçların işletim maliyetleri önemli oranda yüksek olabilir ve her seferinde daha az parça üretilebilir.
Kâr optimizasyonu için mühendislik ve operasyonlar ile birlikte titiz bir DFM (İmal Edilebilirlik Tasarımı) sürecini uygulamaya geçirmeyi ve bu şekilde, parçaların sundukları fonksiyonlar için doğru şekilde boyutlandırılmalarını ve tanımlanmalarını sağlamayı düşünün.
Örneğin, eğer bir parça, kesim sehpasından, parçanın teknik özelliklerinin izin verdiği boyutsal toleransları çok aşan kaynak toleransının bulunduğu kaynak kovuğuna gidiyorsa, parça tasarımının belirlediği katı toleranslar anlamsız olabilir.
Toleranslar söz konusu olduğunda, daha katısı daha iyidir gibi bir yaklaşımın tuzağına düşmeyin. Gereksiz üretim yatırımı ve maliyetlerini önlemek için parça maliyeti ve fonksiyonel tavizler açısından ele alınarak parçanın teknik özellikleri değerlendirilmelidir.
*Boyutsal toleranslar kesilecek metalin kalınlığına göre değişebilir.