Pressure tank manufacturer
Read moreIndustrial pressure vessel fabrication
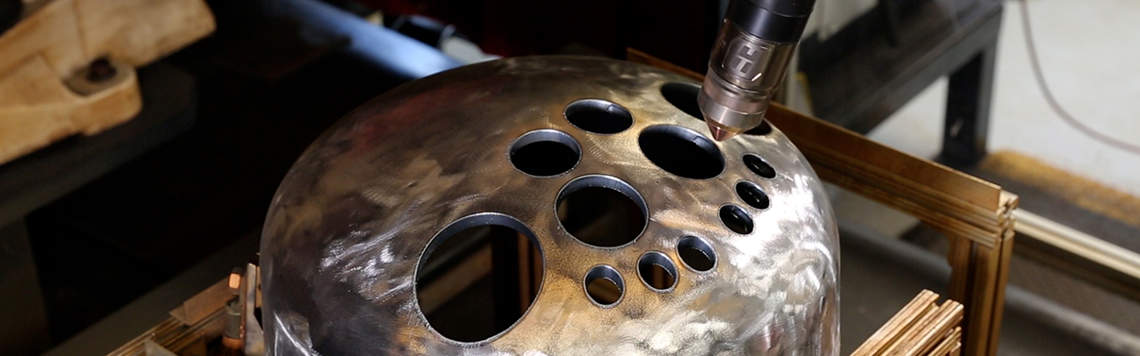
Traditional manufacturing processes for pressure vessel heads can involve hours of manual marking and cutting, followed by hours of grinding. With Hypertherm’s automated plasma cutting solutions, these steps are reduced to minutes, or eliminated altogether, while improving safety, efficiency, and cut quality for added value across the entire operation.
Adding value with robotic pressure vessel cutting
For large, complex pressure vessel assemblies, layout and marking, cutting, and grinding processes can consume a full shift or more, creating bottlenecks and consume valuable skilled labor.
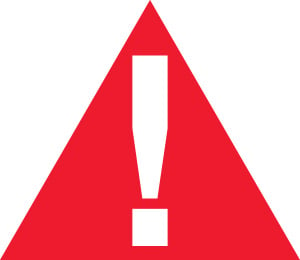
Safety
Robotic cutting eliminates operator risks such as tripping hazards, combustible gases, and awkward ergonomic positions.
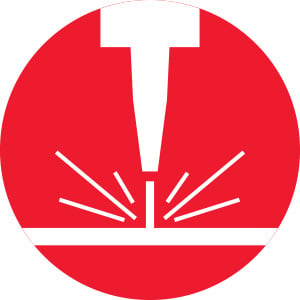
Cut quality
Consistent geometry and high cut quality results in weld-ready parts, reducing bottlenecks, secondary grinding steps, and the need for excess weld filler material.
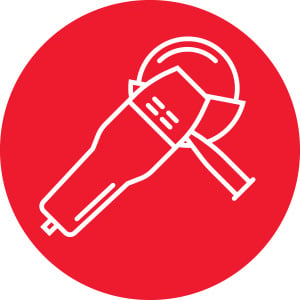
Secondary operations
Minimize the need for secondary grinding and finishing operations after cutting, reducing prolonged exposure to cutting and grinding noise, dust, and vibration, and making the most of your time and your workforce.
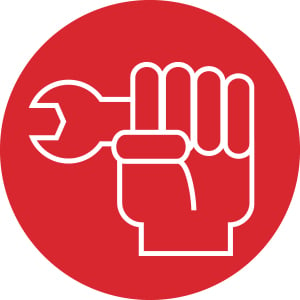
Skilled labor
Get ahead of the skilled labor shortage by shrinking the learning curve for newer employees, and replacing time-consuming and inconsistent manual layout marking and cutting operations with easy-to-program automated solutions.
State of the art robot and programming technologies enables flexible high-mix, low volume production, and by working with a robot cell integrator, it is possible to combine several operations into a single cell (cutting, welding, grinding, handling), optimizing your value stream.
Explore solutions for pressure vessel fabrication
Robot programming
Offline programming solutions to maximize robot productivity on high-mix, low-volume production runs. Reduce programming time, easily program parts of varying complexities, and eliminate the robot downtime associated with manual or teach pendant programming.
Robotic plasma cutting
Robotic cutting systems support your most complex projects. Combined with robot programming, robotic plasma cutting dramatically improves efficiency by increasing cut speeds, cut quality, and production in low-volume runs — returning hundreds of hours to your business.
Plasma marking
Marking metal to indicate bend or score lines, inventory numbers, or reference points for drilling or robotic processes is traditionally done with a hammer and punch, powder or ink, soapstone, or handheld engraving machines. Using plasma for marking during CNC processes offers many significant advantages.