Robotic plasma bevel cutting
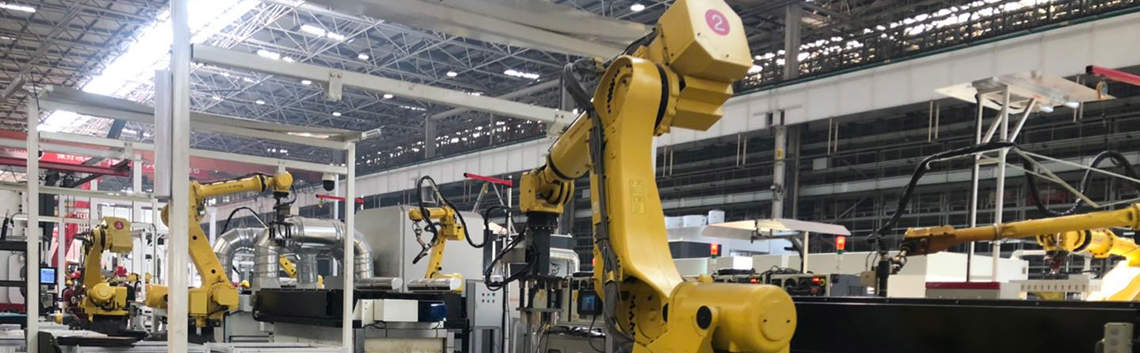
Bevel-cut angles are critical for weld and joint preparation. Milling, oxyfuel, flame cutting, laser cutting, and plasma cutting, with varying levels of automation, are common methods.
Common beveling problems
-
Parts cut with oxyfuel are distorted out of tolerances by heat, making automated welding impossible. Corrections to part geometry require long and costly secondary processes such as manual grinding and use of filler material to weld gaps.
-
Manual bevel cutting slows operations, and quality is dependent on operator skill and experience.
-
In addition to creating production bottlenecks, manual beveling and rework operations expose operators to poor ergonomic conditions, as well as hazardous dust, noise, and vibration.
Adding value with robotic plasma beveling
Replacing current hand-held or carriage track beveling processes with robotic automation improves cut quality and consistency, enabling automated welding processes downstream without the need for secondary grinding steps or excessive fill welding by human operators.
When compared to robotic oxyfuel beveling, the efficiency of robotic plasma beveling is more than 3 times higher, with a comprehensive cost 3 to 4 times lower.
The accuracy and reliability of robotic bevel cutting with X-Definition® and air plasma results in superior quality and flexibility, and results in faster lead times, which are critical to remaining competitive in the face of ever-increasing market demand.