Является ли плазма эффективной альтернативой лазеру?
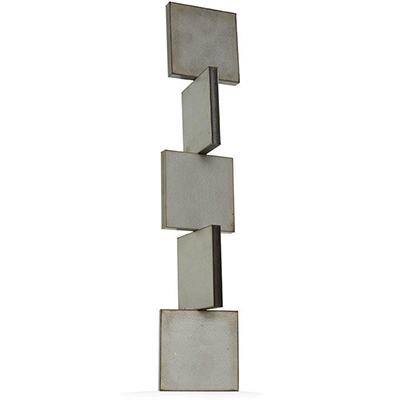
За последние два десятилетия возможности плазменной резки существенно выросли благодаря изобретению компанией Hypertherm прецизионной резки, а также благодаря постоянным усовершенствованиям в области технологии резаков и расходных деталей и внедрению в 2008 году технологии XD. Дальнейшее повышение возможностей применения плазмы для решения задач по высокоточной резке обусловлено внедрением нового класса резки под названием X-Definition™.
При условии установки на высококачественную машину для резки, оснащенную линейными направляющими и зубчатыми рейками эллиптической формы, новая система плазменной резки XPR300™ от Hypertherm со встроенной технологией резки X-Definition обеспечивает допуски в пределах класса 1 и 2 по ISO 9013 и качество резки в пределах диапазона 2 и 3 по ISO 9013. Кроме того, при резке материалов большей толщины, поверхности кромок, получаемых при использовании системы XPR300, как правило, более гладкие, чем кромки, получаемые при резке волоконным лазером; качество кромок при резке остается стабильным на протяжении всего срока службы комплекта расходных деталей.
Лазер, с другой стороны, широко известен тем, что позволяет с очень высоким качеством выполнять резку мелких деталей и вырезание отверстий благодаря узкому разрезу (примерно 0,2–0,4 мм для низкоуглеродистой стали при резке с кислородом); при резке низкоуглеродистой стали толщиной до 25 мм с использованием азота получается еще более узкий разрез. Волоконный лазер также обеспечивает очень хорошую прямолинейность реза и при очень жестких допусках, в пределах 0,2 мм. Для сравнения, разрезы, получаемые при резке плазмой металла, находятся в диапазоне от 1,5 мм для материала очень малой толщины до 5 мм при обработке металла толщиной 25 мм с силой тока 300 А. Исходя из вышесказанного, можно сделать вывод о том, что наилучшим вариантом для резки деталей крайне малого размера или вырезания мелких отверстий (с соотношением толщины к диаметру менее 1:1) является лазер.
Вместе с тем, при необходимости получения высококачественных резов по периметру при допусках в пределах 0.020 дюйма предпочтительным вариантом является плазма, так как она позволяет выполнять резку на более высокой скорости, особенно при обработке материала толщиной более 10 мм. Например, при указанной толщине материала плазменная резка с силой тока 170 А с применением технологии X-Definition обеспечивает высокое качество реза на скорости, в два раза превышающей аналогичный показатель для волоконного лазера мощностью 4 кВт с использованием кислорода.
Внедрение технологии X-Definition также способствовало значительному прогрессу в области резки цветных металлов и сплавов. Благодаря технологиям вентилируемого сопла, vent-to-shield и поглощения пульсаций давления и потока плазмы при резке нержавеющей стали толщиной до 12 мм практически не образуется окалины и получаются очень прямые кромки. Использование в качестве плазмообразующего газа смеси N2-Ar-H2 также обеспечивает исключительное качество резки при обработке нержавеющей стали большей толщины. Новая технология Vented Water Injection (VWI) позволяет выполнять резку алюминия толщиной от 6 до более 25 мм без образования окалины и получить гладкие прямые кромки. Безусловно, для прецизионной резки нержавеющей стали крайне малой толщины лучше всего подходит волоконный лазер; но для обработки материалов большей толщины, в частности, листов стали толщиной более 6 мм, плазменная резка X-Definition представляет собой эффективную альтернативу при меньших затратах.
Кроме того, изобретение компанией Hypertherm в 2008 году процесса True Hole® для низкоуглеродистой стали и выпуск системы XPR300, поднявший указанную технологию на новую высоту, предоставляют возможность простого выполнения отверстий под болты с соотношением диаметра к толщине вплоть до 1:1.
Еще одним типом резки, для которого лучше всего подходит плазма, является резка со скосом. В частности, появление технологии True Bevel™ значительно повысило рентабельность операций резки со скосом прямо на машине для резки. Это позволило сократить затраты и свести к нулю потребность во вторичной обработке. Благодаря тому, что резка со скосом повышает эффективную толщину разрезаемого листа, применение плазмы для обработки материала может обеспечивать значительные преимущества по скорости резки.
Кроме того, с помощью плазмы можно успешно резать листы со следами окисления или иными дефектами. Для плазменной дуги наличие подобных дефектов не является препятствием для резки. Про волоконный лазер, однако, подобного сказать нельзя. В заключение отметим, что, несмотря на то, что при выполнении плазменной резки необходимо использовать средства индивидуальной защиты от шума и яркого света, для использования систем с волоконным лазером требуется устройство защитного кожуха по всему периметру системы для защиты от возможных травм, которые можно получить от работающего лазерного луча.