Как увеличить рентабельность?
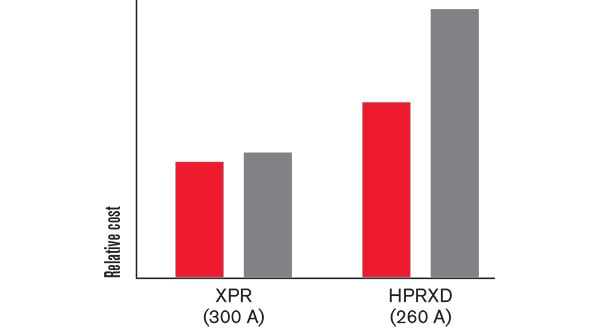
Основным направлением в усовершенствовании технологии плазменной резки с момента ее изобретения является разработка методов снижения затрат на метр разрезаемого металла. Именно данный принцип снижения затрат, положенный в основу множества новейших технологий, реализованных в системе XPR300™, является определяющим фактором, позволяющим пользователю системы повысить рентабельность своей работы. Указанное значительное сокращение эксплуатационных затрат при использовании системы XPR300 стало возможным благодаря ряду факторов, таких как скорость резки, срок службы расходных детали и качество резки.
Фактор номер один — скорость резки. Система XPR300 позволяет выполнять резку листов металла наиболее часто используемой толщины на 10–20 % быстрее по сравнению с предшествующей версией, а при резке металла толщиной более 50 мм — почти на 50 % быстрее.
Thickness | XPR300 | HPR260XD | HPR400XD |
XPR300 |
HPR400XD и XPR300 % |
|
15 mm | 3440 | 3130 | 3950 | 10% | 15% | |
20 mm | 2550 | 2170 | 2805 | 18% | 10% | |
25 mm | 1950 | 1685 | 2210 | 16% | 13% | |
30 mm | 1530 | 1290 | 1790 | 19% | 17% | |
40 mm | 940 | 790 | 1160 | 19% | 23% | |
50 mm | 560 | 405 | 795 | 38% | 42% | |
60 mm | 385 | 258 | 580 | 49% | 51% | |
70 mm | 250 | N/A | 380 | N/A | 52% |
Скорость резки (mm/min)
Также стоит отметить, что система XPR300 более эффективна в работе, так как требует меньшей силы тока для обеспечения той же производительности, что и предшествующие версии. Как показано на диаграмме ниже, для достижения одной и той же скорости резки системе XPR требуется всего 170 А, в то время как системе HPR — 200 А выходного тока.
Вторым ключевым фактором, оказывающим влияние на величину эксплуатационных затрат, является срок службы расходных деталей. В условиях лабораторных испытаний инженерам Hypertherm удалось почти на 50 % повысить количество резов по сравнению с результатами, которых удавалось добиться раньше. В то время как ранее срок службы комплекта расходных деталей составлял около 1000 резов, расходные детали системы XPR способны выдержать почти 1400 резов низкоуглеродистой стали толщиной 3/4 дюйма длительностью 20 секунд. Подобное увеличение срока службы расходных деталей стало возможно благодаря ряду факторов. Одним из них является тщательно продуманная конструкция системы XPR. В источнике тока системы реализована технология под названием Arc Response Technology, которая автоматически предотвращает события, которые могут привести к повреждениям системы или сокращению срока службы расходных деталей.
Для примера рассмотрим ошибки плавного выключения. Указанные ошибки, при которых происходит неконтролируемое прекращение подачи дуги в результате ее ухода с листа или выпадения при вырезании внутреннего элемента (отверстия или щели), приводят к серьезным повреждениям расходных деталей. Причина заключается в том, что гафниевый эмиттер, расположенный у наконечника электрода, не способен вернуться в твердое состояние при внезапном прекращении подачи дуги. В результате, при каждой ошибке плавного выключения, небольшой фрагмент гафния отделяется от электрода, что приводит к ускоренному износу расходных деталей.
Источник тока системы XPR300 устраняет данную проблему благодаря усовершенствованной функции автоматического обнаружения. При обнаружении состояния, предшествующего ошибке плавного выключения, система запускает процесс быстрого контролируемого прекращения подачи дуги, что позволяет значительно продлить срок службы электрода и сопла. В то время как срок службы расходных деталей в большинстве систем плазменной резки сокращается примерно на 50 % вследствие ошибок плавного выключения, для системы XPR300 потери от данных ошибок по сроку службы составляют менее 10 %. Это соответствует сроку службы, почти в три раза превышающему стандартный.
Еще одним важным фактором, который необходимо принимать во внимание, является качество резки. В системе XPR300 реализован совершенно новый класс резки, который называется X-Definition. Благодаря таким усовершенствованным функциям, как Cool nozzle™, Advanced arc stability, расширенной резке HyDefinition на сплавах, не содержащих железа, технологиям Vented Water Injection (VWI), раздельному смешиванию газов (H2, Ar, N2), технологиям Vent-to-shield и Plasma Dampening, суть которой состоит в том, что пульсации давления и потока в сопле поглощаются установленной в нем камерой, возможно достижение исключительной стабильности качества резки на протяжении очень длительного периода времени.
В то время как с помощью систем HyPerformance HPR для деталей можно было стабильно получать резы диапазона 4 по ISO, система XPR300 обеспечивает качество резки в диапазоне 3 по стаадарту ISO, а на материалах меньшей толщины — в диапазоне 2.
Подобные серьезные улучшения по качеству резки низкоуглеродистой стали, и, что более важно, нержавеющей стали и алюминия, могут создать условия для того, чтобы производители начали применять типы резки, традиционно выполняемые при помощи лазера или в специализированных центрах по резке, на своих предприятиях. В перспективе это позволит значительно сократить затраты, оптимизировать цепочку поставок (перейти на работу по принципу «строго вовремя»), выполнять задания в более сжатые сроки, и в целом, увеличить общую рентабельность.
Качество кромки реза алюминия, полученное при помощи технологии VWI (патентная заявка на рассмотрении) системы XPR300
Качество кромки реза нержавеющей стали, полученное благодаря уникальной функции системы XPR300 по смешиванию газов H2-Ar-N2 в качестве плазмообразующего газа в консоли OptiMix
В заключение можно отметить, что именно сочетание в рамках одной системы таких факторов, как более быстрые скорости резки, более длительный срок службы расходных деталей, защита от ошибок плавного выключения, улучшенное качество и повышенная стабильность резки, способны обеспечить снижение эксплуатационных затрат и повышение рентабельности. По факту, использование системы XPR300, выходной ток которой равен 300 А, может снизить относительные затраты на метр разрезаемого материала более чем на 50 %.