Как повысить производительность?
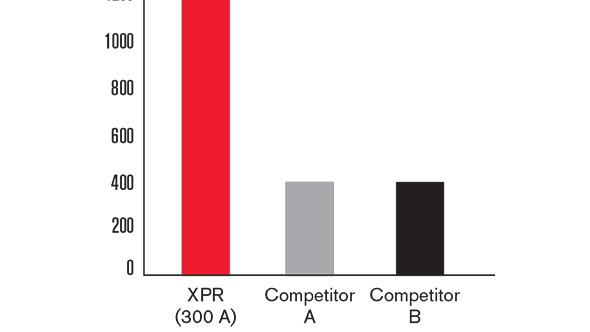
Применительно к промышленной резке, производительность (или ее отсутствие) можно свести к сумме трех факторов. Скорость резки, качество резки и время полезной работы системы. Новая система XPR300™ от Hypertherm обеспечивает повышение производительности по всем трем указанным направлениям. Данная система позволяет выполнять резку быстрее и с более высоким качеством, благодаря чему снижается объем требуемой вторичной обработки (вплоть до полного устранения необходимости в таковой). Применение интеллектуальных технических решений и использование экономящих время операций позволяет увеличить полезное время работы системы.
Скорость резки
Увеличение скорости резки стало возможным благодаря повышению выходного тока и мощности в системе XPR300 до 300 А (260 А в предыдущей версии системы) и 63 кВт, соответственно. Точное значение повышения скорости зависит от толщины разрезаемого материала. В общем, для материала толщиной от 15 до 40 мм прирост скорости составляет 10–20 %; для материала толщиной 50 мм скорость резки увеличена на 38 %, при резке материала толщиной 60 мм скорость выше на 50 %.
Thickness | XPR300 | HPR260XD | HPR400XD |
XPR300 |
HPR400XD и XPR300 % |
|
15 mm | 3440 | 3130 | 3950 | 10% | 15% | |
20 mm | 2550 | 2170 | 2805 | 18% | 10% | |
25 mm | 1950 | 1685 | 2210 | 16% | 13% | |
30 mm | 1530 | 1290 | 1790 | 19% | 17% | |
40 mm | 940 | 790 | 1160 | 19% | 23% | |
50 mm | 560 | 405 | 795 | 38% | 42% | |
60 mm | 385 | 258 | 580 | 49% | 51% | |
70 mm | 250 | N/A | 380 | N/A | 52% |
Скорость резки (mm/min)
Кроме более высокой скорости резки, система XPR превосходит предшествующую систему HPR260XD® и по эффективности. Как показано на диаграмме ниже, для достижения одной и той же скорости резки системе XPR300 требуется всего 170 А, системе HPR260XD — 200 А. Новая система обеспечивает не только повышение скорости резки, но и снижение потребляемой мощности.
Качество резки
Говоря о качестве резки, необходимо отметить, что в системе XPR300 реализован совершенно новый класс резки, который называется X-Definition™. Данный класс резки позволяет повысить качество резки, которое измеряется по международному стандарту ISO 9013, с помощью которого определяют качество резки деталей при термической резке. В рамках стандарта применяется шкала от 1 до 5; при этом наилучшим считается рез в диапазоне 1. Новая система XPR позволяет стабильно получать качество резки в пределах диапазона 3 по стандарту ISO на протяжении практически всего срока службы расходных деталей. Что же касается систем HPRXD®, то, как показано ниже, среднее качество реза, которое они обеспечивали, находится в пределах диапазона 4.
Несмотря на то, что в диаграмме выше представлены данные применительно к резке низкоуглеродистой стали толщиной 12 мм, результаты лабораторных испытаний показывают, что при резке низкоуглеродистой стали меньшей толщины с меньшей силой тока можно получить качество резки в пределах диапазона 2 по шкале ISO. Кроме повышения качества резки, необходимо также отметить улучшения, связанные с ее стабильностью. Как показано на диаграмме, в ходе лабораторных испытаний, включавших в себя сотни резов продолжительностью 20 секунд, были достигнуты результаты, позволяющие говорить об очень высоком уровне стабильности резки. Деталь, для резки которой использовались совершенно новые расходные детали, выглядела практически так же, как и деталь, вырезанная с использованием расходных деталей, выдержавших к тому моменту более 1000 зажиганий дуги.
Система обеспечивает значительное улучшение качества резки применительно к таким металлам, как низкоуглеродистая, нержавеющая сталь и алюминий. Это стало возможным благодаря применению ряда новых технологий (патентная заявка на рассмотрении). В рамках одной из них, которая называется Vented Water Injection, плазмообразующий газ (азот) используется совместно с защитным экраном (вода), что позволяет добиться лучшего центрирования и концентрации дуги. Вторая технология под названием Vent-to-Shield позволяет использовать в процессе резки водород из отходящего плазмообразующего газа, смешивая его с защитным газом. Применение указанных двух технологий позволяет получать рез с более прямыми кромками, сниженной угловатостью и более высокой чистотой поверхности, по сравнению с резкой с помощью систем HPR. В системах XPR также применяется процесс под названием Advanced Arc Stability, позволяющий стабилизировать плазменную дугу, а также новые протоколы деления дуги на сегменты для вырезания отверстий. Эффективность их применения превосходит результаты, получаемые при использовании лучшей из существующих на данный момент в отрасли технологии True Hole® от Hypertherm.
Полезное время работы системы
Несмотря на то, что в системах XPR применяется большое количество самых современных технологий, сама система достаточно проста в использовании. Датчики источника тока предоставляют точные коды диагностики и существенно улучшенную информацию для мониторинга системы. Это позволяет сократить время на поиск и устранение неисправностей и получать данные в упреждающем режиме, что даст возможность лучше оптимизировать работу системы.
Кроме того, в этой системе меньше консолей и подключений, что позволяет операторам уделять больше внимания непосредственно резке, поскольку меньше времени уходит на настройку. К функциям, позволяющим сэкономить время на операции обслуживания, относятся: соединительное устройство EasyConnect™, которое позволяет операторам быстро подключить резак к консоли без использования инструментов. Электрод QuickLock™ (патентная заявка на рассмотрении) фиксируется поворотом на четверть оборота, сокращая время на настройку задания; новая конструкция позволяет оператору быстро заменить резак одной рукой. На всех системах есть функции автоматического управления подачей газов, которые позволяют операторам выбирать и выполнять задания резки непосредственно с ЧПУ, беспроводной связи (оборудование встроено в источник тока) для удаленного мониторинга системы (или нескольких систем).
Продление срока службы расходных деталей также позволяет увеличить полезное время работы системы и сократить эксплуатационные затраты. Функция Cool Nozzle™ (патентная заявка на рассмотрении) делает возможной подачу охлаждающей жидкости прямо в сопло, что позволяет увеличить срок службы расходных деталей на 40 %. Запатентованная технология PowerPierce® решает, в принципе, такие же задачи в отношении защитного колпачка. В рамках данного процесса охлаждающая жидкость подается к защитному колпачку, благодаря чему в процессе прожига брызги расплавленного металла отталкиваются от поверхности колпачка, не повреждая его. Клапан в разъеме резака позволяет оперативно и более точно контролировать потоки газов, что способствует значительному увеличению времени резки кислородом без остановки и более быстрому плавному выключению. Как показано ниже, устранение ошибок плавного выключения для большинства типов резки равноценно увеличению срока службы расходных деталей почти в 3 раза по сравнению с любой иной системой. Меньше времени на замену расходных деталей — больше времени на резку и иные технологические операции.
Резюмируем. Система XPR300 позволяет добиться большей производительности благодаря сочетанию таких факторов, как более высокие скорости резки, улучшенное качество резки и увеличенное полезное время работы.
Как повысить производительность?