Износ электродов в системах воздушно-плазменной и кислородно-плазменной резки
Как отличить естественный износ электрода от неестественного и повысить производительность системы.
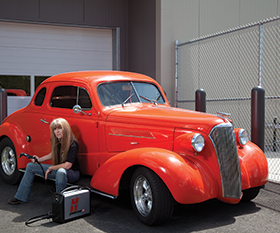
Электроды для высокомощных систем плазменной резки — это конструктивно сложные расходные детали. Их конструкция, материал и принцип работы подобны соответствующим характеристикам автомобильных свечей зажигания. Так же, как и свечи зажигания, электроды проводят электричество высокого напряжения в среде с высокой температурой. Поэтому материалы, из которых состоит электрод, должны быть устойчивы к воздействию веществ, образующихся при температуре плазменной дуги, и высокоскоростных струй вихревого газа. Кроме того, эти материалы должны обеспечивать надежное уплотнение, не допускающее утечек газов и жидкостей под высоким давлением. Подобно свече зажигания, электрод — это наиболее прочная рабочая часть в системе.
Осмотрев свечи зажигания, опытный автомеханик может сказать многое о состоянии двигателя внутреннего сгорания. Точно так же, опытный технический специалист может сделать выводы о состоянии системы плазменной резки. Для этого необходимо знать, как осматривать электрод, иметь представление об характере обычного износа и признаках, свидетельствующих о наличии проблем.
Электрод проводит питание постоянного тока от источника тока системы плазменной резки к металлическому листу. Типичная конструкция электрода — это держатель из меди или композитного материала медь-серебро с эмиттером из гафния — тугоплавкого металла, устойчивого к воздействию дуги в средах воздушно-плазменной или кислородно-плазменной резки. Эмиттер постепенно изнашивается под воздействием высоких температур дуги и высокоскоростных потоков плазмообразующего газа. Основной износ электрода приходится на запуск и останов резки, когда гафниевый материал плавится и отвердевает, быстро нагреваясь и остывая.
При нормальном износе на краю детали образуется небольшое изъязвление вогнутой формы. Оно постепенно увеличивается в размере (на несколько тысячных см за один раз) до 0,10–0,31 см в зависимости от конструкции и материалов резака и расходных деталей. (См. таблицу ниже). Когда изъязвление становится слишком глубоким, дуга цепляется за материал держателя и расплавляет его. Электрод приходит в негодность, когда он больше не может зажечь или поддержать дугу. Если расплавленный материал с электрода стекает вниз и откладывается в отверстии сопла, это приводит к внезапному и неустранимому отказу электрода и сопла.
Система плазменно-дуговой резки | Медные электроды, износ в дюймах | Электроды из композита медь-серебро, износ в дюймах |
Прецизионная система плазменно-дуговой резки (кислородно-плазменная резка) |
0,07–0,12 см | 0,15–0,20 см |
Система плазменно-дуговой резки с впрыском воды |
0,10–0,20 см | 0,25–0,35 см |
Традиционная система плазменно-дуговой резки с использованием двухкомпонентной газовой смеси (кислородно-плазменная резка) | 0,10–0,20 см | 0,25–0,35 см |
Традиционная система плазменно-дуговой резки с использованием двухкомпонентной газовой смеси | 0,22–0,30 см | 0,25–0,35 см |
Срок службы деталей в самых современных системах кислородно-плазменной резки обычно составляет 1–2 часа фактического времени «на дуге» или 200–300 прожигов. В системах воздушно-плазменной резки этот срок может в два раза превышать указанный, достигая таким образом 400–600 запусков. Это обусловлено тем, что содержащийся в воздухе азот понижает интенсивность реакции воздуха с электродами. В системах кислородно-плазменной резки с инертными пусковыми газами и плавным изменением тока срок службы электрода может достигать 1000 или более запусков.
Рис. 1
|
Новое состояние На рис. 1 показан новый электрод. Представленный в этом примере электрод имеет конструкцию из сварного композитного материала медь-серебро с серебром в передней части электрода и медью в его задней части. В центре детали расположен неиспользованный гафниевый элемент.
|
Рис. 2
|
Естественный износ На рис. 2 представлен электрод с естественным износом. Изъязвление гафниевой вставки образовано в ее центре и однородно по форме, что свидетельствует о правильном выравнивании расходных деталей и соответствующей скорости потока вихревого плазмообразующего газа. Глубина изъязвления составляет приблизительно 0,25 см. Передние края детали ровные и четкие. Цвет серебра существенно не изменился. На передней поверхности детали заметны оксидные образования серого оттенка. Это обычное явление.
|
Рис. 3
|
Естественный износ на 1/2 от полного износа На рис. 3 представлен электрод с типичными признаками естественного износа. Данный электрод сняли с системы до окончания срока службы по другой причине. Таким причинами могут быть: скольжение резака по листу, удар резака, изменение напряжения, изменение качества резки и т. д. Глубина изъявления составляет 0,19 см. Несмотря на то, что этот электрод выглядит как отработанный, он еще может выполнить 100 или более прожигов, а его изъязвление может увеличиться до 0,25 см или даже до 0,35 см, прежде чем он выйдет из строя.
|
Рис. 4
|
Изъязвление не по центру На рис. 4 представлен электрод с изъязвлением, смещенным относительно центра. Эту проблему легко заметить. Такое расположение изъязвления свидетельствует о серьезной проблеме с потоком газа (неисправный или закупоренный завихритель) или о разбалансировке деталей резака (вследствие ошибок при сборке и проблем с подгонкой деталей). Если эту проблему не удается решить путем полной замены деталей резака, это может свидетельствовать о неисправности самого резака.
|
Рис. 5
|
Влага при запуске Картина на рис. 5 свидетельствует о наличии влаги при запуске дуги. Представленные детали имеют неровные следы воздействия вихревой дуги от выточки под ключ до контактной поверхности электрода. Влага в газе, который подается до возбуждения дуги, приводит к тому, что серебро подвергается воздействию высоких частот. Передние края серебра нечеткие; качество поверхности как при обработке пескоструйным аппаратом. Проверьте газ, который подается до возбуждения дуги, на наличие влаги. Быструю проверку можно выполнить с помощью бумажного полотенца. Поместите чистое бумажное полотенце под резак и включите подачу газа в системе (только в режимах TEST (ТЕСТ) или GAS CHECK (ПРОВЕРКА ГАЗА)!). На полотенце не должно быть признаков наличия влаги или загрязнений.
|
Рис. 6
|
Утечки охлаждающей жидкости Рис. 6. Из всех проблем легче всего заметить утечки охлаждающей жидкости. Сильное искрение контактной поверхности электрода; на боковых поверхностях электрода имеются изъязвления и полости. Передняя поверхность шероховатая и черная с блестящими точечными наплавлениями из материала держателя. Эта проблема часто происходит из-за разреза уплотнительных колец, недостаточной смазки уплотнительных колец или по причине ненадежно закрепленных или разбалансированных деталей.
|
Рис. 7
|
Недостаточная подача газа до возбуждения дуги Рис. 7. Недостаточная подача газа при возбуждении дуги обусловливает медленное зажигание. Перенос дуги с начальной точки (как правило, это острый угол, наподобие выточки под ключ) на эмиттер длится слишком долго. На этих деталях будет достаточно однородное кольцо расплавленного материала держателя вокруг изъязвления. Поверхность может выглядеть, как спаянные брызги металла, или вдоль передней части детали может образоваться сварочная ванна.
|
Рис. 8
|
Эксплуатация до отказа На рис. 8 представлен электрод, который эксплуатировался до неустранимого отказа. Поскольку электрод расположен выше, то при его работе повреждается сопло, когда расплавленный материал выдувается с наконечника электрода и откладывается на внутренней поверхности сопла. При достаточно длительной эксплуатации в работе всех деталей наступает такой отказ.
|
Рис. 9
|
Эксплуатация до отказа Рис. 9. Недостаточная подача плазмообразующего газа Мелкие углубления вдоль всего края электрода и соответствующие повреждения сопла свидетельствуют о недостаточной скорости потока газа. Недостаточная скорость потока газа приводит к неконтролируемому зажиганию дуги между соплом и электродом. Проверьте скорости потока газа, подаваемого на резак. Лучше всего это сделать, используя расходомер (0–400 куб.фут/ч) со шлангом, надетым на выпускное отверстие резака тестируемой системы. Если нет возможности воспользоваться расходомером, можно выполнить тест на тактильное ощущение потока газа на выпускном отверстии резака, когда включена подача только плазмообразующего газа. Должен ощущаться вихревой поток газа, который действует как всасывающая сила.
|
Рис. 10
|
Высокая скорость потока газа Рис. 10. Если сопло в хорошем состоянии, но при этом электрод имеет глубокое концентричное изъязвление, то скорость потока плазмообразующего газа может быть слишком высокой. При интенсивном воздействии вихрей плазмообразующего газа элемент быстро разрушается. Это приводит к стремительному глубокому износу. Проверьте объемную скорость потока плазмообразующего газа.
|