Основные рекомендации для повышения качества плазменной резки
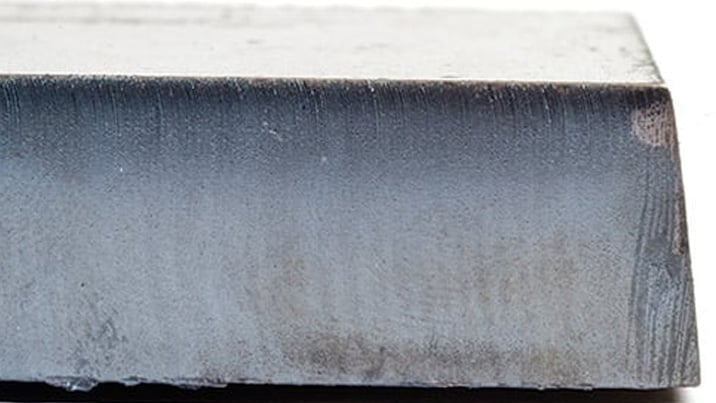
Ниже в справочном руководстве приводится описание нескольких методов, позволяющих повысить качество резки. Следует опробовать и испытать все эти методы, поскольку зачастую на качество резки влияет множество факторов.
- Тип машины (например, стол для координатной резки, вырубной пресс, робот)
- Система плазменной резки (например, система воздушно-плазменной резки, кислородно-плазменной резки, система прецизионной плазменной резки)
- Устройство управления перемещением (например, возможности машины с ЧПУ и системы регулировки высоты резака)
- Переменные процесса (например, скорость резки, высота резки, выбранные расходные детали)
- Внешние переменные факторы (например, неоднородность материалов, чистота газа, опыт оператора)
Поэтому в процессе усовершенствования процесса резки важно учитывать все эти факторы.
Шаг 1. Проверка направления плазменной дуги
Наиболее прямые углы среза при резке всегда находятся справа по направлению движения резака.
- Проверьте направление резки
- При необходимости измените направление резки
Плазменная дуга при использовании стандартных расходных деталей вращается по часовой стрелке.
Контур:
- Резак движется по часовой стрелке
- Хорошая сторона среза находится справа от резака при его движении вперед
Внутренняя функция (отверстие):
- Резак движется против часовой стрелки
- Хорошая сторона среза находится справа от резака при его движении вперед.
Лист с внутренним отверстием
Шаг 2. Проверка выбора процесса в соответствии с материалом и толщиной
См. технологические карты резки в разделе «Эксплуатация» инструкции по эксплуатации Hypertherm.
Обязательно соблюдайте технические характеристики, приведенные в технологических картах резки:
- Выберите подходящий процесс с учетом перечисленных ниже факторов:
- Тип материала
- Толщина материала
- Требуемое качество среза
- Требования к производительности
- Выберите нужный плазмообразующий и защитный газ
- Выберите нужные значения следующих параметров.
- Значения давления газа (или скорости потока)
- Расстояние между резаком и изделием и дуговое напряжение
- Скорость резки
- Убедитесь, что используются соответствующие расходные детали (для этого нужно проверить номера деталей)
Примечание. Обычно при процессах с малым током удается достичь меньшей угловатости и более качественной поверхности, однако при этом ниже скорость резки и больше окалины.
Шаг 3. Проверка износа расходных деталей
- Проверьте расходные детали на предмет их изношенности
- Замените изношенные расходные детали
- Электрод и сопло нужно заменять одновременно
- Не наносите на уплотнительные кольца излишнее количество смазки
Примечание. Для достижения наилучших показателей резки используйте фирменные расходные детали Hypertherm.
Шаг 4. Проверка перпендикулярности резака заготовке
- Выровняйте заготовку
- Расположите резак перпендикулярно заготовке (относительно и передней, и боковой сторон резака)
Примечание. Проверьте материал на наличие неровностей и искривлений. В сложных случаях перпендикулярности добиться невозможно.
Шаг 5. Проверка корректности расстояния между резаком и изделием
- Отрегулируйте расстояние между резаком и изделием
- При использовании управления дуговым напряжением отрегулируйте напряжение
Примечание. По мере износа расходных деталей нужно регулировать дуговое напряжение для поддержания нужного расстояния между резаком и изделием.
Расстояние между резаком и изделием может влиять на угловатость среза
Отрицательный угол среза: резак расположен слишком низко; увеличьте расстояние между резаком и изделием
Положительный угол среза: резак расположен слишком высоко; уменьшите расстояние между резаком и изделием
Примечание. Небольшое расхождение угла среза является нормальным, если оно находится в пределах допуска.
Шаг 6. Проверка используемой скорости резки
- Отрегулируйте скорость резки, как необходимо
Примечание. Скорость резки может влиять на объем окалины.
Окалина при высокой скорости: слишком высокая скорость резки (дуга отстает); нужно уменьшить скорость
Окалина при низкой скорости: слишком низкая скорость резки (дуга уходит вперед); нужно увеличить скорость
Верхнее забрызгивание: слишком высокая скорость резки, ее нужно уменьшить
Примечание. Помимо скорости, на уровень образования окалины влияет состав материала и качество его поверхности. По мере нагревания заготовки в ходе последующих операций резки может образовываться большее количество окалины.
Шаг 7. Проверка наличия проблем с системой подвода газа
- Найдите и устраните все утечки или сужения
- Используйте регуляторы и газовые магистрали нужного сечения
- Используйте чистый высококачественный газ
- Если требуется ручная очистка, например при использовании MAX200, убедитесь, что цикл очистки завершен
- Обратитесь к поставщику газа
Шаг 8. Проверка наличия вибрации резака
- Убедитесь, что резак надежно зафиксирован в портале стола
- Обратитесь к изготовителю комплексного оборудования. Возможно, необходимо техническое обслуживание стола
Шаг 9. Проверка необходимости настройки стола
- Убедитесь, что стол обеспечивает выполнение резки на заданной скорости
- Обратитесь к изготовителю комплектного оборудования. Возможно, необходимо выполнить настройку скорости стола