Powermax gouging for better weld preparation on railcars
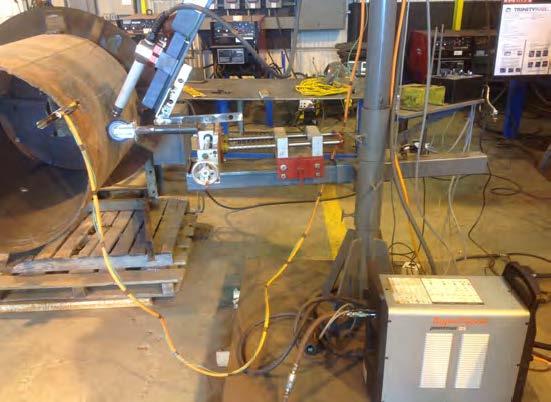
Customer overview
When parts are prepared for welding, their edges can be beveled to produce a groove for the weld. A common practice in weld preparation is back gouging. Back gouging is the removal of weld and base metal from the other side of a partially welded joint to ensure complete fusion and penetration after subsequent welding from that side. It removes material from the root of a weld before filler material is added behind the joint. Carbon arc gouging and grinding are frequently used for back gouging.
Back gouging is used to create a weld that is stronger and more durable, creating a joint that is as strong as the base metal. It is commonly used in applications where high stress and high strength are required, such as aerospace, shipbuilding, structural steel, boilers, pipelines, and railcars.
One Hypertherm customer was using carbon arc gouging for back gouging seams on railcars.
Challenge: Carbon arc gouging is loud, messy, and hazardous
Carbon arc gouging can be challenging for operators. It takes skill to create consistent gouges and requires extensive training. Because of high currents (up to 2000A) and high air pressures (80 to 100 psi), carbon arc gouging can be very noisy, requiring ear protection. The air jet causes the molten metal to be ejected over a significant distance, so extra care must be taken to keep workers safe from molten metal.
Carbon arc gouging also creates hazardous fumes. The force of the air blast tends to vaporize much of the molten metal into fine droplets, creating fumes consisting of metal vapor, carbon dust, and metallic byproducts.
Most electrodes used in carbon arc gouging are made from a mixture of graphite and pure carbon. As the electrode is consumed, it releases carbon into the base material. This carbon becomes brittle as it cools and must be removed before welding, requiring the entire gouge to be grinded or sanded before welding. This secondary work is labor intensive, increasing both the costs and time required to finish the job.
Solution: Automating gouging with Powermax125 improves gouge quality, worker safety
The company replaced carbon arc gouging by hand with automated gouging using the Powermax125® plasma cutting system and a track cutter.
Plasma gouging benefits
Plasma gouging is generally four times faster than carbon arc gouging and creates cleaner, more consistent gouge profiles that need little to no secondary work.
Plasma gouging is easier to learn, requiring less training, so new hires are productive faster and the company saves on training costs. The work environment is also safer. The plasma gas pushes the molten metal out of the groove less violently than carbon arc gouging air jets. As a result, arc spatter is reduced and less molten metal vaporizes, reducing the metallic vapor and reaction with the surrounding atmosphere and generating fewer toxic fumes. Plasma gouging is also 5 to 10 decibels quieter than carbon arc gouging.
The Powermax125
Delivering maximum power and performance for air plasma, the Powermax125 plasma system cuts thick metals fast. The system makes short work of the toughest cutting and gouging jobs and offers a 100% duty cycle, a 25 mm (1 inch) mechanized pierce capability, and fast gouging metal removal. Eleven Duramax Hyamp torch styles provide versatility for hand cutting, portable automation, X-Y table cutting, extended reach cutting, and robotic cutting and gouging.
Benefits of the Powermax125 include:
-
Operators finish jobs faster with cut speeds five times greater than oxyfuel on 12 mm (½ inch) mild steel.
-
Superior cut and gouge quality ensure operators spend less time on grinding and edge preparation.
-
100% duty cycle maximizes cutting time.
-
Operators do not need to manually change the air pressure because the Powermax’s Smart Sense™ technology ensures that air pressure is always correctly set.
-
SpringStart™ technology ensures consistent starting and a more reliable torch.
-
Operators can drag cut at full output with a patented shield that reduces dross buildup for smoother cutting.
-
Consumable life is up to four times longer than other systems in this amperage range.
-
Electrode end-of-life detection protects the torch and workpiece from damage by automatically stopping power when the electrode is overused.
Track cutting and gouging
Track cutting and gouging is used to make long, straight cuts or gouges that are difficult and time-consuming to do by hand with the necessary precision. Track cutting is sometimes used on a job site when the material to be cut or gouged is of a size or shape not suited to an X-Y table. Automating these processes with a portable track burner increases productivity and results in a more uniform cut or gouge.
Although originally designed for use with oxyfuel torches, many track burners now deliver the faster speeds needed when cutting with plasma. Typical uses include shipbuilding, pressure vessel fabrication, scrapping I-beams, structural steel applications, and back gouging welded plates.
Business impact: Cleaner welds reduce secondary operations
Switching from hand carbon arc gouging to automated plasma gouging has improved gouge quality for the company. The gouges are very clean compared to the carbon arc gouge, requiring minimal clean-up and secondary grinding. Now that the process is automated, the consistency of the width and depth of the gouges is far superior to carbon arc gouging.
Learn how the Powermax125 plasma cutting system can improve gouge quality, increase worker safety, and eliminate secondary grinding. Click the button below, fill out the form, and a Hypertherm product expert will contact you.