Scrapyard enjoys 300% growth in productivity with Powermax SYNC
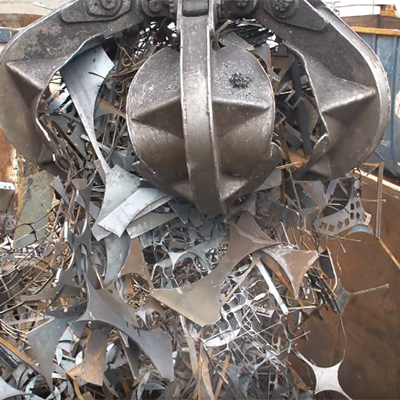
Company overview: Aço e Ferro
Brazil’s Aço e Ferro, which translates to Steel and Iron, has been in the metal scrap business for over 15 years. Its main business is the purchase and sale of scrap, and one of the segments the company serves is mills and foundries. From both an environmental and economic standpoint, recycling metal is extremely effective. Metals such as steel, iron, aluminum, and copper can be recycled an infinite number of times because their metallic properties do not deteriorate with repeated melting and casting.
Aço e Ferro cuts all types of material, but its largest volume is with thicker thicknesses, ranging from 12 to 16 mm.
Challenge: Oxyfuel could not keep up with increased daily demand
Aço e Ferro could not keep up with the daily volume of scrap coming in from the mills and foundries it serves. When the volume of the material to be cut increased, oxyfuel became a problem because the oxyfuel cutting process was not fast enough to keep up with demand. In addition, there was a constant concern for the safety of operators due to the highly flammable gas that oxyfuel needs to work.
Solution: Powermax SYNC increases productivity
When Aço e Ferro began to lose business due to capacity constraints, they reached out to a supplier and the supplier suggested switching to a plasma cutting system. Aço e Ferro tested many brands, but their experience with most plasma systems was negative. Most of the plasma cutting systems they tested were not sturdy enough and did not stand up to Aço e Ferro’s process, so these plasma cutting systems broke easily. Also, most plasma torches require the operator to hold the torch off of the material while cutting.
The company was convinced that the Powermax SYNC® was the right choice after Hypertherm demonstrated the system in Aço e Ferro’s cutting operation. Aço e Ferro was impressed with how sturdy the Powermax SYNC was and how easy it was to use. They chose the Powermax105 SYNC for their operation.
“We were impressed with the robustness of the equipment and the ease of use for the operator to handle it.” – Aço e Ferro
The Powermax105 SYNC
The Powermax105 SYNC is a next-generation, professional-grade air plasma cutter that dramatically simplifies system operation for gouging and cutting up to 32 mm (1 ¼ inches). It features automated system process set-up via advanced RFID-enabled SmartSYNC® torches and a revolutionary single-piece cartridge consumable that provides trackable utilization data. The Powermax105 SYNC maximizes productivity through reductions in downtime, optimized cut quality performance, and streamlined consumable inventory management.
Benefits include:
-
RFID-enabled SmartSYNC torches and cartridges automatically set the correct amperage and operating mode, eliminating setup errors.
-
End-of-life consumable detection eliminates the uncertainty of knowing when to change the cartridge consumables.
-
Flexible lead reduces operator fatigue.
-
Simplified system operation minimizes the time and costs spent on training and troubleshooting.
-
Easily interchangeable torch styles and application-specific cartridges for various types of cutting and gouging (e.g., drag cutting, max removal gouging, mechanized cutting) enable operators to tackle a wide range of jobs.
-
Time-saving hand torch controls allow the operator to adjust the amperage on the fly and change cartridges and applications without returning to the power supply.
-
Powermax SYNC plasma systems and SmartSYNC torches are engineered for rugged, industrial environments and can be used in challenging locations.
-
SpringStart™ technology ensures consistent starting and a more reliable torch.
Drag cutting with Hypertherm Powermax
Generally, operators need to hold the tip of the torch off the material they are cutting. Hypertherm torches are unique, so operators using a Hypertherm torch do not have to hold a stand-off. Operators can use Hypertherm torches directly on the material they are cutting because Hypertherm’s consumables are shielded. This shield technology, found on the front of the torch, electrically isolates the nozzle from the metal workpiece to eliminate a common phenomenon known as double arcing.
There are a couple of advantages to drag cutting. Drag cutting is easier for the operator. Operators don't have to worry about having a steady hand and can simply drag the torch along a straight edge or template. This is much easier than trying to keep a torch at an exact distance from a workpiece while cutting. In most cases, operators will end up with a more accurately cut piece. Drag cutting also helps increase consumable life, because spatter and blow back aren’t as much of a problem.
Operators using a Powermax SYNC can drag the torch right on the metal while cutting using Hypertherm’s yellow, Drag Cut, cartridges.
Business impact: Powermax SYNC delivers 300% increase in productivity
After purchasing the Powermax105 SYNC, Aço e Ferro saw several improvements to their process. The biggest impact was increased productivity. Before purchasing the Powermax SYNC, their maximum capacity was to cut around 900 kilos per day and they needed three or four operators to do it. With the Powermax SYNC, one operator can cut around three tons per day – a more than 300% increase in productivity. The Powermax SYNC also produces higher quality cuts, so it has dramatically reduced material loss.
“Our maximum capacity was to cut around 900 kilos per day and we needed three or four operators. With Powermax SYNC, only one operator can cut around three tons per day.” Aço e Ferro
The second benefit was the Powermax SYNC’s ease of use. Operators can just plug the Powermax in and start working, and it can be used right on the plate, making cutting much easier for operators. It does not require changing cannisters containing highly flammable gas the way oxyfuel does, so it’s easier to use, more efficient, and safer.
“When I worked with oxyfuel, it was very exhausting, because at each step of the work, you have to stop and interrupt to change the gas. Another major issue with oxyfuel is that you cannot touch it directly to the part.” – Neir Antonio da Silva, Plasma Operator, Aço e Ferro
Finally, the Hypertherm SYNC is much sturdier than other plasma systems the company tested, working well in conditions that caused other plasma systems to fail.
Other brands of plasma cutters we tested did not stand up to our process and broke easily.
Aço e Ferro
Learn how the Powermax SYNC can help your business increase efficiency. Click the button below, fill out the form, and a Hypertherm product expert will contact you.