Sargent burns double the parts with the XPR300
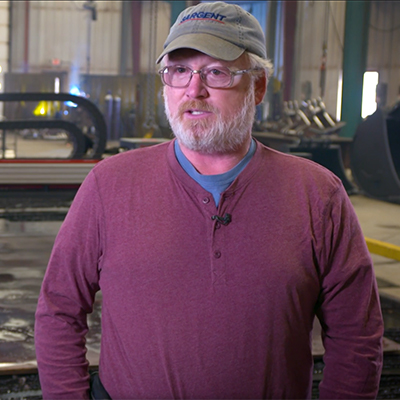
Company overview
Sargent Corporation is a team of over 450 employee-owners building infrastructure projects – including renewable energy, highways, commercial site work, landfill cells, and underground work – in the Northeast and Mid-Atlantic regions of the United States. Sargent has offices in Maine, New Hampshire, Virginia, and North Carolina.
Challenge: Old burn table was slow and could not keep up with production
Sargent’s various infrastructure projects require moving a lot of earth, so the company has a fleet of excavators and bulldozers. They make a variety of excavator attachments, such as buckets, couplers, tilt buckets, and conversion plates.
They were using an old burn table, but it was slow. Demand for production was increasing, and the old table could not keep up. They decided that they needed to upgrade.
Solution: The XPR300 fulfills all of Sargent’s requirements
The Sargent team thought about upgrading to a laser system but quickly realized that the Hypertherm XPR300® with ProNest® nesting software and True Hole® technology would deliver exactly the speed, accuracy, and ease of use they required. “We thought about doing laser, but the XPR300 better suited our needs,” noted Marcel Rancourt, Welding Supervisor at Sargent Corporation.
The XPR300
The XPR300 represents a significant advancement in mechanized plasma cutting technology, redefining what plasma can do by expanding its capabilities and opportunities in ways never before possible. With unmatched cut quality on mild steel, stainless steel, and aluminum, the XPR300 increases cut speed, dramatically improves productivity, and reduces operating costs.
Ease-of-use features and system optimizations make the XPR300 easier to run with minimal operator intervention, lowering labor requirements while ensuring optimal performance and unmatched reliability. The XPR system’s intuitive operation and automatic system monitoring redefine what simple and user-friendly plasma cutting means.
The XPR300 is designed with fewer consoles and easy connections, so operators spend less time setting up and more time cutting.
Additional ease-of-use features include:
-
EasyConnect™ torch lead and one hand torch-to-receptacle connection enable fast and easy change-outs.
-
QuickLock™ electrode delivers easy consumable replacement.
-
Full control of all functions and settings is available via the CNC.
-
Wi-Fi in the power supply enables multiple system monitoring and service from mobile devices.
-
Arc response technology™ provides automatic torch and ramp-down error protection, eliminating the impact of ramp-down errors and reducing the impact of catastrophic electrode blowouts which can damage the torch – significantly extending the life of consumables.
-
Sensors in the power supply deliver refined diagnostic codes and significantly enhanced system monitoring information, reducing troubleshooting time and delivering proactive data to improve overall system optimization and uptime.
ProNest nesting software
ProNest nesting software for advanced mechanized cutting is designed to supercharge cutting operations, enabling greater automation, efficiency, and profitability. ProNest optimizes performance for plasma, laser, waterjet, and oxyfuel cutting machines. Its powerful, high-yield nesting reduces material costs and increases profitability.
ProNest’s intuitive screens and a wide variety of helpful features make it easy to learn and use. Its faster, fully automated interface can reduce programming time from hours to minutes, while specialized cutting techniques can reduce total cut time by up to 50%.
True Hole technology
True Hole technology produces significantly better hole quality than what has been previously possible using plasma. True Hole is automatically applied by the nesting software or CNC software to thicknesses up to 25 mm (one inch). Diameter and hole coverage range from hole diameter to thickness ratios from 2:1 to as low as 1:1.
True Hole technology benefits include:
-
True bolt-hole quality is delivered automatically, without operator intervention.
-
True Hole narrows the gap with laser hole quality, making the plasma process suitable for many jobs previously cut with laser.
-
Hole taper is virtually eliminated.
-
Ding is reduced and biased to the outside of the hole.
Business impact: Sargent more than doubles the number of parts cut each day
Sargent cuts plates from 1/8 inch to 1 ½ inches, and they burn a lot of mild steel. The XPR300 is significantly faster than their old system, and the cut quality is much better. There is no dross, eliminating secondary work and greatly increasing efficiency. At the same time, True Hole technology enables Sargent to create bolt-ready holes.
“We cut anywhere from 1/8 inch to 1 ½ inch plate, we burn a lot of mild steel, a little bit of aluminum and stainless,” shared Matt Moon, Table Operator, Sargent Corporation. “The XPR is a lot faster, the cuts are cleaner, there’s no dross on the bottom side of the cut, so I can burn at least double the parts in the day. And it helps the guys that put the pieces together because they don’t have to spend as much time preparing the part.”
Sargent cuts 60 tons of plate on the table each year, and they are very impressed with the quality and quantity of the pieces they can cut with the XPR300. “This year, we probably burned 60 tons of plate on this thing, so it’s been pretty impressive,” said Marcel Rancourt, Welding Supervisor, Sargent Corporation. “We’re building over 200 pieces each year now and we plan on expanding more, so it’s been a valuable part of the process. The quality is excellent. We get nice, smooth cuts.”
The team is also impressed with how easy ProNest is to use and how much more efficient cutting is with ProNest.
“ProNest is easy to use, and we probably do things two to three times faster than we did before, so at times that frees up a man to do other work on projects. It saves a lot of time, money, headaches.”
Marcel Rancourt
Welding Supervisor, Sargent Corporation
Overall, the Sargent team is very happy with the XPR300. It has greatly increased efficiency and cut quality. “The XPR300 is the way to go. It’s a very good piece of equipment. We’re real impressed with it,” said Rancourt.
Learn how the XPR300 can help your business strike the perfect balance between cut quality, cut speed, and cost. Click the button below, fill out the form, and a Hypertherm product expert will contact you.
Contact an expert