Company uses robots equiped with Hypertherm plasma to enhance cutting efficiency and reduce costs across 6 factories
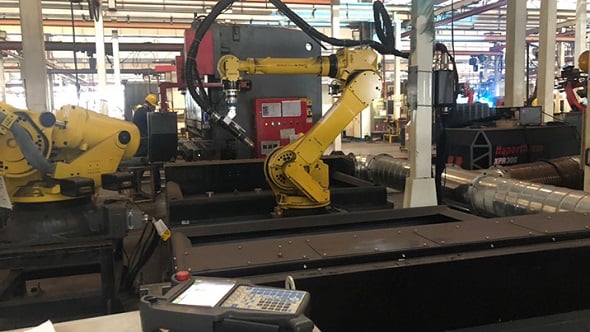
— Business impact —
-
Gained Significantly improved cutting efficiency, with less than 5 minutes for loading, cutting, and unloading
-
Trippled efficiency of component production
-
Reduced use of combustible gases, eliminating safety hazards
Overview
Since its founding in 1994, this leading construction machinery manufacturer has experienced rapid and continuous growth. Today, the company is recognized as one of the global leaders in equipment manufacturing. Their product portfolio is comprised of concrete machinery, excavators, cranes, pile drivers, road construction machinery, and prefabricated structural components. Their dominant products, including pump trucks, trailer pumps, excavators, crawler cranes, rotary drilling rigs, and complete sets of road construction equipment are renowned as top brands in China.
Challenge
The company established the first, fully digital factory in the domestic construction machinery industry. Their independently developed MES (Manufacturing Execution System) and functional warehousing logistics system serve as the foundation for flexible mixed-flow production lines and production modes within the factory. Among these operations, the company requires bevel cutting of bench parts. Although they have introduced robotic cutting, the existing robotic flame cutting cannot keep up with the production pace due to high production volume. Additionally, the use of combustible gases for on-site flame cutting poses various safety risks.
Solution
Upon learning about this issue, a key account manager from Hypertherm Associates shared their solution of using robots equipped with the Hypertherm XPR300® plasma cutting system for bevel cutting. In addition, Hypertherm Associates deployed customer application engineers to various factories of the company, assisting partners in customizing and fine-tuning the most effective application solutions based on the actual working conditions of each factory. Ultimately, a robotic plasma beveling solution with a single plasma source and dual cutting stations, as well as automatic loading and unloading capabilities, was delivered. The company's six factories in Changsha, Beijing, Shanghai, Kunshan, Shenyang, and Huzhou were successively upgraded to use robots equipped with the XPR300 plasma bevel cutting system.
Learn how your business can strike the perfect balance between cut quality, cut speed, and cost. Click below and fill out the form so the right expert can be in touch.
Prefer to research more before having a conversation? Learn more about XPR plasma.