R.M.P. Products triples cutting speed by using XPR300 to cut bolt holes
Cuts three times faster than drilling
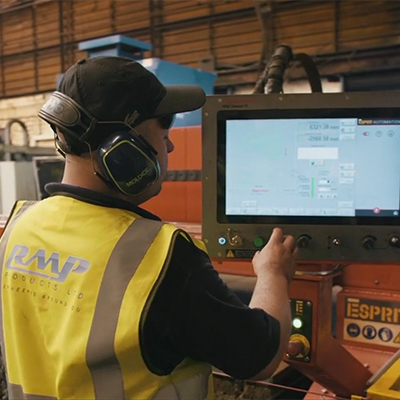
— Business impact —
-
Realized 3x faster cutting speed
-
Excellent cut quality and control
-
Increased customer satisfaction with high quality cut and finish
Company: R.M.P. Products
R.M.P. Products (RMP) specializes in high-definition plasma cutting, CNC flame/gas cutting, chamfering/edge beveling, machining, Lumsden grinding, and shot blasting. With a focus on quality, accuracy, on-time deliveries, and customer service, RMP undertakes large and small profiling jobs from all sectors, including general fabrication, earth moving, oil & gas, mining, rail & highway, structural, recycling, offshore, renewables, and high-end specialized nuclear projects.
Challenge: Old machinery too costly to run and maintain
RMP has been delivering precision components and steel profiling jobs since 1992. A few years ago, the company was experiencing high costs both running and servicing their old cutting system. They decided to invest in a new plasma cutting system to lower ongoing costs of operations, improve cut quality, and increase customer satisfaction.
Solution: XPR300 delivers faster, higher-quality cuts at a lower cost
RMP purchased a new Hypertherm XPR300® to replace their old cutting machine, increase productivity, lower operating costs, and improve cut quality. At the time, it was the biggest investment the company had ever made.
The XPR300
The XPR300 represents a significant advancement in mechanized plasma cutting technology, redefining what plasma can do by expanding its capabilities and opportunities in ways never before possible. The XPR300 blends new technology with refined processes for next generation, X-Definition® cutting that delivers unmatched cut quality on mild steel, stainless steel, and aluminum.
The XPR300 also delivers increased cut speed, dramatically improved productivity, and a significant reduction in operating costs. In addition, new ease-of-use features and engineered system optimization make the system easier to run with minimal operator intervention, while also ensuring optimal performance and reliability.
Benefits of the system include:
-
Improved cut quality on thin mild steel, with consistent ISO range 2 results
-
Extended ISO range 3 cut quality results compared with earlier plasma technology
-
Superior stainless steel cut quality across all thickness ranges
-
Superior results on aluminum using Vented Water Injection™ (VWI)
-
Increased cut speeds on thicker materials
-
Thicker piercing capability than with competitive plasma systems
-
Consumable life that is three times longer than consumable life in competitive plasma systems
-
Lower energy costs with 62% higher power-to-weight ratio and 14% faster cuts
The XPR300’s advanced power supply technology delivers highly responsive, rapid system feedback and automatically intervenes to eliminate events that negatively impact system efficiency and consumable life. Arc response technologyTM provides automatic torch and ramp-down error protection to increase the life of the torch and consumables.
Sensors in the power supply deliver refined diagnostic codes and enhanced system monitoring information to reduce troubleshooting time and provide proactive system maintenance data for improved system optimization. These enhancements eliminate the impact of ramp down errors and increase consumable life to up to three times longer than that of competitive systems. They also reduce the impact of catastrophic electrode blowouts which can damage the torch at high current levels.
Intuitive controls and operation, together with automatic monitoring, make the system easy to use, even for new operators. Training is faster, and seasoned operators deliver better cut quality more efficiently. Full control of all functions and settings is available via the CNC, and automatic system monitoring and specific troubleshooting codes improve maintenance and service. Wi-Fi in the power supply connects to mobile devices and LAN for multiple system monitoring and service.
Both consumable and torch changes are easier as well. The XPR300’s EasyConnect™ torch lead and one hand torch-to-receptacle connection enable fast and easy change-outs, and the system’s QuickLock™ electrode makes consumable replacement easy.
Business Impact: The best investment the company has ever made
R.M.P. Products considers the Hypertherm XPR300 the best investment the company has ever made. The XPR300 cuts three times faster than their previous cutting machines, delivers higher quality cuts, and has increased customer satisfaction.
The XPR300 is the biggest investment the company has ever made. But, looking back, it's the best investment the company has ever made.
R.M.P. Products
The cut quality is much better than the quality they had with their previous cutting machine, and the XPR300 is easier for operators to use. The controls are clear and easy to understand, with fewer buttons, so it’s also easier to learn how to use it.
The XPR300 cuts much better bolt holes than their previous machine. The XPR300 holds .5 mm tolerance on thicknesses up to about 15 mm from top to bottom. On their previous machine, they had 1-1.2 mm tolerance from top to bottom. This significant improvement in cutting tolerance enabled them to completely change their business processes.
Because the bolt holes cut with the XPR300 are so much better than with previous plasma cutting machines, RMP now uses the XPR300 to cut bolt holes rather than having to drill the holes. This has significantly increased productivity. Using the XPR300, RMP is cutting bolt holes three times faster than they have experienced using any other cutting process they have used.
ROI was quick with the XPR300. Their previous machine began to pay for itself after 12 months. The XPR300 runs 24/7 and began paying for itself immediately. The system is also less expensive to operate and maintain.
“I would certainly recommend the XPR300, simply because of the consumable cost, the speed, and the quality of the cut – which is massive in today’s trade. Quality of cut and finish is huge.” R.M.P. Products
The company has even invited some of their key customers, including JCB and Caterpillar, to visit the shop. These companies have seen the XPR300 in action, and they are also impressed with the finish and hole quality.
We deal with some real good customers – JCB, Caterpillar – and they have been in and have seen the machine, and they are very, very impressed with the finish and hole quality as well.” R.M.P. Products
Learn how the XPR300 can help your business strike the perfect balance between cut quality, cut speed, and cost. Click the button below, fill out the form, and a Hypertherm product expert will contact you.