Easy to use and cleaner, dross-free cuts across various industries
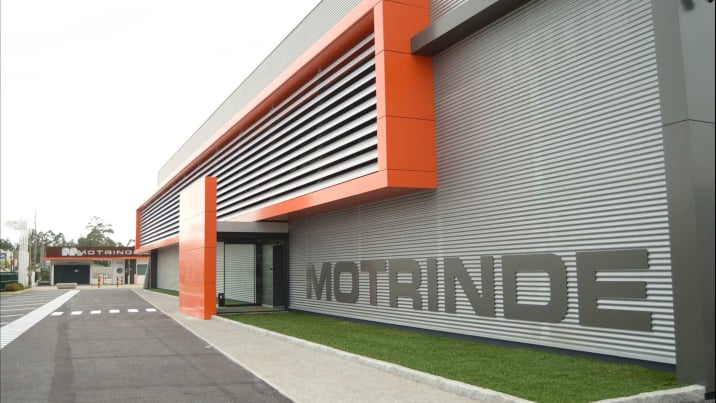
Background
Based in Portugal, family-owned, Motrinde has been a leader in metalworking for 29 years. Specializing in metal mechanics, industrial maintenance, and metal construction, Motrinde serves various industries, including paper, mining, environmental, and nuclear sectors. With a commitment to high-quality manufacturing processes and innovative solutions, Motrinde continuously seeks to enhance its operations and productivity.
Founded nearly three decades ago, Motrinde has built a reputation for excellence and reliability. The company’s dedication to quality and innovation has allowed it to grow and adapt to the changing needs of its diverse clientele. Over the years, Motrinde has invested in state-of-the-art technology and training for its workforce, ensuring it remains at the forefront of the metalworking industry. This commitment to continuous improvement has enabled Motrinde to deliver superior products and services, earning the trust and loyalty of its customers.
Challenges
Despite their success, Motrinde faced several challenges in their manual cutting processes:
-
Complexity and inefficiency: Traditional manual cutting methods were time-consuming and required significant skill and effort. The intricate nature of these processes often led to inconsistencies in the cut quality, affecting the operations' overall efficiency. Skilled labor was essential, but the availability of such labor was limited, making it challenging to maintain high standards consistently.
Manual cutting processes involved a high degree of precision and control, which could only be achieved by experienced operators. However, relying on manual methods meant that even minor errors could lead to significant delays and increased costs. The complexity of the tasks also made it challenging to scale operations, as training new employees to the required skill level was both time-consuming and costly.
- Material heating: Excessive heating of materials during cutting led to quality issues and increased the need for post-processing. The heat generated during manual cutting could cause warping and other forms of thermal distortion, compromising the integrity of the final product. This affected the quality and increased the time and cost associated with additional processing steps to correct these issues.
The problem of material heating was particularly pronounced in industries where precision and quality were paramount. For instance, in the nuclear sector, any form of thermal distortion could have serious implications for the safety and functionality of the components. As a result, Motrinde had to invest considerable resources in post-processing to ensure that the final products met the stringent quality standards required by their clients.
-
Need for grinders: Relying on grinders for finishing cuts increased the workload and reduced overall efficiency. Grinders were necessary to achieve the desired finish, but it was a labor-intensive process that further slowed down production. Additionally, using grinders posed safety risks to the operators, increasing the potential for workplace injuries.
Grinders were used to smooth out rough edges and remove any excess material left after cutting. While this was essential for achieving a high-quality finish, it also introduced additional steps into the production process, each requiring careful attention and skill. The physical demands of using grinders also meant that operators were at risk of repetitive strain injuries and other health issues, further impacting productivity.
Solution
The introduction of the Powermax105 SYNC system revolutionized Motrinde’s cutting processes. This advanced system brought several key benefits that addressed the challenges faced by the company:
-
Simplified cutting: The Powermax105 SYNC simplifies manual cutting with single-component consumables and color-coded cartridges, making the process more user-friendly. The system's intuitive design reduces the operators' learning curve, allowing them to achieve high-quality cuts with minimal training. This improves efficiency and reduces the dependency on highly skilled labor.
The Powermax105 SYNC's user-friendly interface and straightforward operation mean that even less experienced operators can quickly become proficient in using the system. This has allowed Motrinde to expand its workforce more easily, as new employees can be trained more quickly and effectively. The simplified cutting process also reduces the likelihood of errors, leading to more consistent and reliable results.
-
Reduced material heating: The system minimizes material heating, ensuring higher quality cuts with less thermal distortion. By controlling the heat input more effectively, the Powermax105 SYNC prevents warping and other heat-related issues, resulting in cleaner and more precise cuts. This reduces the need for post-processing and enhances the overall quality of the final product.
Cutting materials with minimal heating has been a game-changer for Motrinde, particularly in industries where precision is critical. The reduced thermal distortion means that components can be produced to exact specifications without extensive post-processing. This saves time and money and ensures that the final products meet the highest quality standards.
-
Elimination of grinders: By providing cleaner, dross-free cuts, the need for grinders is eliminated, streamlining the workflow. The precision of the Powermax105 SYNC’s cuts means that additional finishing steps are no longer necessary, significantly speeding up the production process. This also reduces the risk of injuries associated with using grinders, creating a safer working environment for the operators.
The elimination of grinders has had a profound impact on Motrinde's operations. It has reduced the physical demand on operators and streamlined the production process, allowing the company to increase its output without compromising quality. The improved safety and efficiency have also contributed to higher employee satisfaction and retention rates.
-
Boosted productivity: The intelligent error detection and self-regulating features of the Powermax105 SYNC enhance efficiency and productivity, allowing Motrinde to meet client demands effectively. The system’s ability to detect and correct errors in real-time ensures consistent quality and reduces downtime. This leads to higher throughput and the ability to take on more projects, ultimately driving growth and profitability for the company.
The Powermax105 SYNC's advanced features have enabled Motrinde to optimize its cutting processes, resulting in significant productivity gains. The system's real-time error detection and capabilities mean that issues can be addressed immediately, minimizing disruptions and ensuring production runs smoothly.
By adopting the Powermax105 SYNC, Motrinde has significantly improved its cutting processes, ensuring cleaner, more efficient, and higher-quality results across various industries.