Phoenix Products achieves closer tolerances, little distortion with XPR300
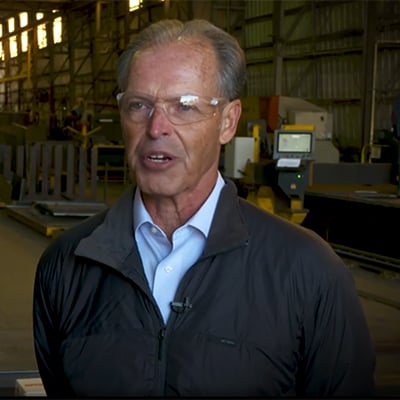
— Business impact —
-
Improved cut quality enables precision parts and less post table work
-
Faster training time with easty-to-use system
-
Increased plate capacity from 5–10 plates per day to 20–30
Company: Phoenix Products
Phoenix Products is a division of Ring Power Corporation, a company that sells and distributes Caterpillar Incorporated heavy equipment and generators. Headquartered in Jacksonville, Florida, Phoenix Products manufactures custom generator enclosures, UL 142 and UL 2085 fuel tanks, and fueling systems for standby, prime, and peak shaving power applications. They serve and satisfy customers in a variety of businesses and industries that include banking, colleges and universities, data centers, grocery stores, federal agencies, hospitals and nursing homes, lift stations, military bases, municipal organizations, retail centers, wastewater treatment plants, and more.
They also manufacture The Rook, an armored critical incident vehicle used by law enforcement throughout the United States to protect police officers in hostage situations or standoffs of some type. The material they use for The Rook is ballistic steel that is rated up to a 50-caliber rifle round, so any bullet that is 50 caliber or lower will not penetrate The Rook’s armor.
Challenge: Cutting ballistic steel was slow and imprecise
Cutting ballistic steel with their old plasma system was slow, and it was not very precise. The old machinery could only cut five to 10 plates per day. Bolt holes required grinding and deburring, decreasing efficiency and increasing costs.
The importance of ballistic steel in law enforcement
Ballistic steel goes through a special process to make it extra hard and dense. It is a tough, bendable, long-lasting material with a wide range of applications, including armored vehicles such as cash-in-transit vehicles, vaults, bank counters, training facilities, security doors, police cars, and security booths. When a bullet hits ballistic steel, the steel absorbs the impact and stops the bullet. A bullet would pierce the side of a standard motor vehicle.
Solution: XPR300 and True Hole technology deliver high-quality results faster
Phoenix Products purchased a new Hypertherm XPR300® to replace their old cutting process, increasing both productivity and cut quality. They were also able to discontinue outsourcing some processes because the XPR300 can cut more refined, intricate patterns than their previous system could with laser machine quality.
The XPR300
The XPR300 represents a significant advancement in mechanized plasma cutting technology, redefining what plasma can do by expanding its capabilities and opportunities in ways never before possible. With unmatched cut quality on mild steel, stainless steel, and aluminum, the XPR300 increases cut speed, dramatically improves productivity, and reduces operating costs.
Ease-of-use features and system optimizations make the XPR300 easier to run with minimal operator intervention, lowering labor requirements while ensuring optimal performance and unmatched reliability. The XPR system’s intuitive operation and automatic system monitoring redefine what simple and user-friendly plasma cutting means.
The XPR300 is designed with fewer consoles and easy connections, so operators spend less time setting up and more time cutting.
Additional ease-of-use features include:
-
EasyConnect™ torch lead and one hand torch-to-receptacle connection enable fast and easy change-outs.
-
QuickLock™ electrode delivers easy consumable replacement.
-
Full control of all functions and settings is available via the CNC.
-
Wi-Fi in the power supply enables multiple system monitoring and service from mobile devices.
· Arc response technology™ provides automatic torch and ramp-down error protection, eliminating the impact of ramp down errors and reducing the impact of catastrophic electrode blowouts which can damage the torch – significantly extending the life of consumables.
· Sensors in the power supply deliver refined diagnostic codes and significantly enhanced system monitoring information, reducing troubleshooting time and delivering proactive data to improve overall system optimization and uptime.
True Hole technology
True Hole technology produces significantly better hole quality than what has been previously possible using plasma. True Hole is automatically applied by the nesting software or CNC software to thicknesses up to 25 mm (one inch). Diameter and hole coverage ranges from hole diameter to thickness ratios from 2:1 to as low as 1:1.
True Hole technology benefits include:
-
Bolt hole quality is delivered automatically without operator intervention.
-
True Hole narrows the gap with laser hole quality making the plasma process suitable for many jobs previously cut with laser.
-
Hole taper is virtually eliminated.
-
Ding is reduced and biased to the outside of the hole.
-
True Hole delivers true bolt-hole quality.
Business Impact: Easy to use XPR300 delivers faster, higher-quality cuts
The XPR300 has exceeded Phoenix Products’ expectations. The system provides better cut quality and significantly increased productivity.
The XPR has a better quality of cut. The overall performance is 300% better. With the old machine, I was able to cut between five and 10 plates per day. With the XPR, I can cut anywhere between 20 to 30 plates per day easily.
Al Hartfield, Table Operator
Phoenix Products
With the old system, they would have to use a grinder and deburr the holes. Hypertherm’s True Hole technology delivers bolt-ready holes that require no grinding or secondary work. Overall cutting performance is 300% better than with their previous system and there is little to no heat distortion.
“The Hypertherm technology is critical to our operation because we need to be able to produce parts that have close tolerances, have little distortion because of the heat, and have holes that line up correctly.” – Rob Delp, Vice President & General Manager, Phoenix Products
With the XPR300, Phoenix Products no longer has to outsource cutting the letters for the names on The Rook, decreasing costs while increasing productivity. Since they installed the Hypertherm plasma system, they create labels in-house that are as good as if they were cutting them off on a laser machine.
The XPR300 has simple controls, so operators quickly learn how to operate the machine. For Phoenix Products, it only took one day of training to teach operators how to use the new system. After just one day of training, their team was prepared to use the new system to increase production from five to 10 plates per day to 20 to 30 plates per day.
Learn how the XPR300 can help your business strike the perfect balance between cut quality, cut speed, and cost. Click the button below, fill out the form, and a Hypertherm product expert will contact you.