MASI improves productivity and quality with Hypertherm’s XPR300
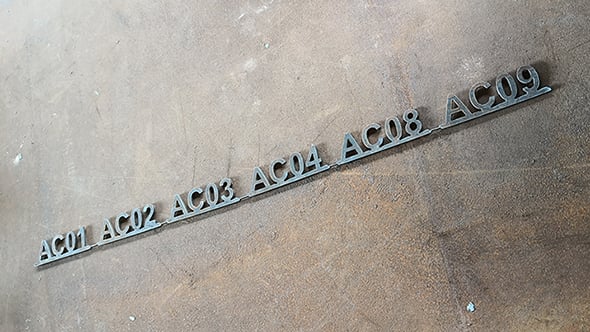
“The XPR300 system has proven to be stable and reliable so far — allowing us to improve our productivity and quality, and we expect that it will also eventually help us to reduce the manpower required in the production of parts for the various systems and equipment.”
Mr. Edward Wong
Technical Manager, MASI
Muhibbah Airline Support Industries Sdn Bhd (MASI) is headquartered in Selangor, Malaysia. MASI manufactures a variety of products for the aviation services sector, including maintenance docking systems, aerobridges, and aircraft parking guidance systems. A subsidiary of Muhibbah Engineering (M) Bhd, the first company in Malaysia to achieve ISO 9002 certification in the construction sector, MASI places strong emphasis on quality and safety in every aspect of its operations.
MASI designs and manufactures a full range of aircraft maintenance docking systems. These systems are specialized platforms positioned around an aircraft to allow maintenance personnel to access all areas of the aircraft, providing an efficient and safe working environment. An effective aircraft maintenance docking system enables the maintenance team to perform their jobs better, which then assures people of aircraft functions and safety.
Challenge: MASI needed a cutting system that could deliver high-quality parts faster
The team at MASI had a good grasp of the aviation industry’s needs, and MASI’s innovative systems featured state-of-the-art functions. To bring these innovative systems to fruition, the company realized it needed to invest in a cutting technology that could produce high-quality cut parts that required little or no post-production processes at fast speeds.
Solution: XPR300 boosts production processes and improves quality
The company chose Hypertherm’s X-Definition® XPR300® plasma cutting system to significantly boost production processes without compromising on quality. They added True Hole® technology to easily fabricate bolt-ready holes down to a diameter-to-thickness ratio of 1:1.
The XPR300
The XPR300 represents a significant advancement in mechanized plasma cutting technology, redefining what plasma can do by expanding its capabilities and opportunities in ways never before possible. The XPR300 blends new technology with refined processes for next-generation, X-Definition cutting that delivers unmatched cut quality on mild steel, stainless steel, and aluminum.
The XPR300 also delivers increased cut speed, dramatically improved productivity, and a significant reduction in operating costs. In addition, new ease-of-use features and engineered system optimization make the system easier to run with minimal operator intervention, while also ensuring optimal performance and reliability.
Benefits of the system include:
- Improved cut quality on thin mild steel, with consistent ISO range 2 results
- Extended ISO range 3 cut quality results compared with earlier plasma technology
- Superior stainless steel cut quality across all thickness ranges
- Superior results on aluminum using Vented Water Injection™ (VWI)
- Increased cut speeds on thicker materials
- Thicker piercing capability than with competitive plasma systems
- Consumable life that is three times longer than consumable life in competitive plasma systems
- Lower energy costs with 62% higher power-to-weight ratio and 14% faster cuts
The XPR300’s advanced power supply technology delivers highly responsive, rapid system feedback and automatically intervenes to eliminate events that negatively impact system efficiency and consumable life. Arc response technology™ provides automatic torch and ramp-down error protection to increase the life of the torch and consumables.
Sensors in the power supply deliver refined diagnostic codes and enhanced system monitoring information to reduce troubleshooting time and provide proactive system maintenance data for improved system optimization. These enhancements eliminate the impact of ramp-down errors and increase consumable life to up to three times longer than that of competitive systems. They also reduce the impact of catastrophic electrode blowouts which can damage the torch at high current levels.
Intuitive controls and operation, together with automatic monitoring, make the system easy to use, even for new operators. Training is faster, and seasoned operators deliver better cut quality more efficiently. Full control of all functions and settings is available via the CNC, and automatic system monitoring and specific troubleshooting codes improve maintenance and service. Wi-Fi in the power supply connects to mobile devices and LAN for multiple system monitoring and service.
Both consumable and torch changes are easier as well. The XPR300’s EasyConnect™ torch lead and one hand torch-to-receptacle connection enable fast and easy change-outs, and the system’s QuickLock™ electrode makes consumable replacement easy.
The XPR300 also provides access to Hypertherm’s exclusive SureCut™ technologies. SureCut technologies are designed to maximize cutting performance by automatically applying optimized cutting process parameters to simplify cutting and reduce operator intervention. These technologies improve cutting outcomes and positively impact the bottom line.
SureCut technologies include:
-
True Hole®technology applies process expertise to automatically deliver bolt-ready holes.
-
True Bevel™ technology automatically applies the correct bevel angle and reduces operator trial and error.
-
Rapid Part™ technologyincreases the number of parts produced per hour by automatically reducing cut-to-cut cycle time between parts.
-
PlateSaver™ technologycombines XPR® arc stability and specialized software parameters to dramatically increase material utilization.
True Hole technology
True Hole technology produces significantly better hole quality than what was previously possible using plasma. True Hole is automatically applied by the nesting software or CNC software to thicknesses up to 25 mm (one inch). Diameter and hole coverage range from hole diameter to thickness ratios from 2:1 to as low as 1:1.
True Hole technology benefits include:
-
True Hole delivers true bolt-hole quality automatically, without operator intervention.
-
True Hole narrows the gap with laser hole quality, making the plasma process suitable for many jobs previously cut with laser.
-
Hole taper is virtually eliminated.
-
Ding is reduced and biased to the outside of the hole.
Business impact: XPR300 improves consumable life, and reduces production times and material waste
The XPR300 with True Hole technology addresses MASI’s requirements for a cutting solution that can handle a variety of plate thicknesses – ranging from 4mm to 40mm – with various types of shape and hole cutting. Cut quality has improved. Switching to the XPR300 has also improved consumable life for MASI while reducing production times and material waste. This has allowed MASI to register cost savings of 10-20%, depending on material thickness.
Apart from the cutting-edge features of the XPR300, MASI was also won over by Hypertherm’s high level of service standards. From the early stages of decision-making through to after-sales assistance, the Hypertherm team offered timely response and their full support to address MASI’s every concern.
On MASI’s plans to further improve their processes, Mr. Edward Wong added that the company is looking to purchase more cutting machines and also plans to explore more advanced solutions such as robotic plasma beam cutting lines.
“Judging from the results we’ve seen so far, we’re optimistic that Hypertherm’s advanced cutting solutions will support our endeavor to improve the agility and profitability of our business. We also look forward to satisfying our customers with consistent and quality products that will allow their maintenance teams to perform their tasks well and ensure safe functioning of aircrafts,” added Mr. Edward Wong.
Learn how the XPR300 can help your business strike the perfect balance between cut quality, cut speed, and cost. Click the button below, fill out the form, and a Hypertherm product expert will contact you.