The XPR300 helps Lyman-Morse diversify and access new opportunities
Increases cut efficiency, accuracy, and quality with Hypertherm plasma
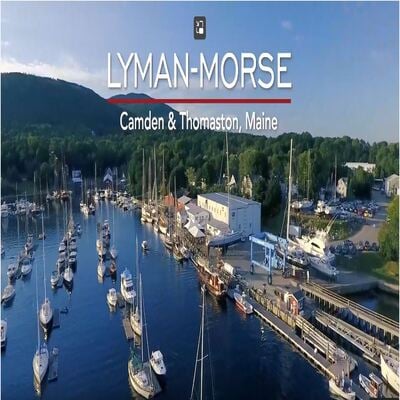
Company: Lyman-Morse
Lyman-Morse’s broad-ranging capabilities are showcased by the skilled people who work at their boatyards in Thomaston and Camden and their modern and expansive facilities. The combination of their state-of-the-art equipment with some of the world’s finest craftsmen has allowed them to develop many areas of expertise in both the marine and non-marine world.
Lyman-Morse Fabrication has established itself as the source for custom-made metal fabrication projects throughout New England and beyond. They combine broad-ranging capabilities, a 15,000-square-foot facility, and fine craftsmen and engineers with expertise in stainless, aluminum, bronze, steel, titanium, and plastics. With a foundation in constructing ocean going yachts and marine components, their fabrication team also designs and works with municipalities, homeowners, architects, businesses, industrial manufacturers, and more.
Challenge: Outsourcing cutting was inhibiting growth
Lyman-Morse was founded in 1978 with a few people building boats in a small facility. Forty years later, the company had expanded and demand for their high-quality boats was accelerating. At the time, they were sending all of their materials out to a vendor to be cut, but this process added both time and cost to each project. They created Lyman-Morse Fabrication to bring cutting in-house.
When they began looking at plasma cutting systems, one of their first concerns – as a marine fabricator – was the size of the heat affected zone in non-ferrous materials, especially stainless steel. The heat affected zone is that area of metal that has not been melted and has undergone changes in properties as a result of being exposed to relatively high temperatures during cutting. A smaller heat affected zone protects the integrity of the metal better. Lyman-Morse needed a process with a small heat affected zone that would also deliver the cut quality they required.
Solution: Hypertherm's XPR300 increases cutting efficiency, accuracy, and quality
After careful consideration and evaluation, the Lyman-Morse Fabrication team chose Hypertherm’s XPR300® for their metal fabrication business. The XPR300’s water-shielded cutting technology has a heat affected zone of just thousandths of an inch, which is within their tolerances for marine fabrication.
They can now cut any material in-house, including titanium, bronze, aluminum, stainless steel, and mild steel, and can cut material up to three inches thick. Lyman-Morse Fabrication also implemented True Hole® technology to improve bolt hole quality.
The XPR300
The XPR300 represents a significant advancement in mechanized plasma cutting technology, redefining what plasma can do by expanding its capabilities and opportunities in ways never before possible. The XPR300 blends new technology with refined processes for next generation, X-Definition™ cutting that delivers unmatched cut quality on mild steel, stainless steel, and aluminum. The XPR300 also delivers increased cut speed, dramatically improved productivity, and a significant reduction in operating costs. In addition, new ease-of-use features and engineered system optimization make the XPR300 easier to run with minimal operator intervention, while also ensuring optimal performance and reliability.
The XPR300 also provides access to Hypertherm’s exclusive SureCut™ technologies. SureCut technologies are designed to maximize cutting performance by automatically applying optimized cutting process parameters to simplify cutting and reduce operator intervention. These technologies improve cutting outcomes and positively impact the bottom line.
SureCut technologies include:
-
True Hole® technology applies process expertise to automatically deliver bolt ready holes.
-
True Bevel™ technology automatically applies the correct bevel angle and reduces operator trial and error.
-
Rapid Part™ technology increases the number of parts produced per hour by automatically reducing cut-to-cut cycle time between parts.
-
PlateSaver™ technology combines XPR® arc stability and specialized software parameters to dramatically increase material utilization.
True Hole technology
True Hole technology for mild steel produces significantly better hole quality than what has been previously possible using plasma. True Hole is automatically applied by the nesting software or CNC software to thicknesses up to 25 mm (one inch). Diameter and hole coverage ranges from hole diameter to thickness ratios from 2:1 to as low as 1:1.
True Hole technology benefits include:
-
Bolt hole quality is delivered automatically without operator intervention.
-
True Hole narrows the gap with laser hole quality making the plasma process suitable for many jobs previously cut with laser.
-
Hole taper is virtually eliminated.
-
Ding is reduced and biased to the outside of the hole.
-
True Hole delivers true bolt-hole quality.
Business Impact: Lower costs, higher quality cuts, and access to new markets
Adopting the XPR300 has been a complete success. The plasma system delivers the efficiencies, accuracy, and quality that Lyman-Morse requires for its marine business and has enabled the company to diversify and offer metal fabrication to companies in markets beyond marine fabrication. With the XPR300, they can cut any material, and have cut titanium, bronze, aluminum, stainless steel, and mild steel, successfully cutting materials up to three inches thick.
The quality of the XPR300 cut is the very best that I’ve seen.
Jonathan Egan, General Manager
Lyman-Morse
Hypertherm’s cutting-edge technology is helping them continue to grow and expand into different markets. Today, the fabrication facility is 90% non-marine based, including projects in the agricultural, aeronautical, architectural, structural, and energy sectors. The stainless steel they cut goes all over the world, used in everything from the pleasure yachts that they build to pharmaceutical applications.
“It provides efficiencies, it provides accuracy, quality, all of the above. If we can stay on that cutting edge with the technology that Hypertherm creates, it allows manufacturers like us to grow and to access different areas of the business environment.” Drew Lyman, President/Owner, Lyman-Morse
Moving cutting inside the facility has helped improve the company’s bottom line as well. Before installing the XPR300, Lyman-Morse sent all of their materials out to a vendor to be cut. Now, they do all the cutting in-house using their own people. This is both more cost effective and a great time saver, and they have complete control over the entire process.
“Previously, we were sending all of our materials out to a vendor to be cut. Now we are doing it all in-house using our own people, which is much better for our bottom line. And, it’s helping us to expand into other sectors that we’ve not been in before such as agricultural, aeronautical, architectural, structural, energy sector.” Jonathan Egan, General Manager, Lyman-Morse
By adopting True Hole technology, they now produce bolt-ready holes in-house right on the CNC table. They have experienced a significant reduction on time spent on these jobs using the XPR300.
Learn how the XPR300 can help your business strike the perfect balance between cut quality, cut speed, and cost. Click the button below, fill out the form, and a Hypertherm product expert will contact you.
Contact an expert