High Steel Structures improves efficiency and accuracy with the Kinetics K5000XMC and XPR460
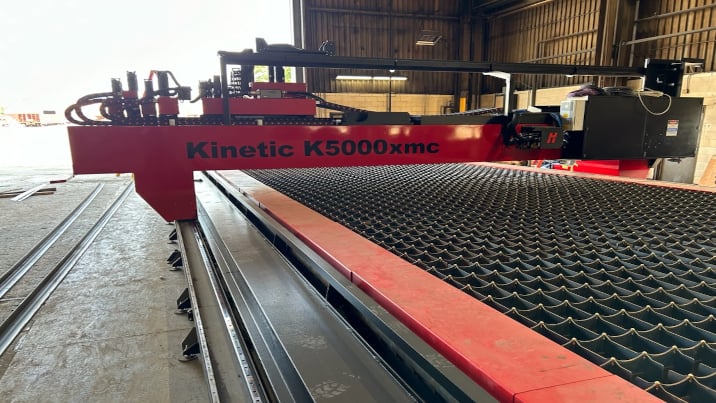
— Business impact —
-
Improved efficiency and accuracy
-
Long-term reliability and high performance
-
Rapid return on investment
Company: High Steel Structures (HSS)
HSS specializes in building steel bridges for highways, pedestrians, and railroads. The company also constructs heavy girders for structural building support. Serving businesses of all sizes, from private entities to the Federal Highway Administration for road projects, HSS has supplied steel for many noteworthy projects, including the Arthur Ravenel, Jr. Bridge, Woodrow Wilson Bridge, Gov. Mario M Cuomo bridge, and the HOT Lanes megaprojects in Northern Virginia.
Operating with over 700 employees across three plants in Lancaster, PA, and one in Williamsport, PA, HSS started as a small welding shop in the 1930s and transitioned to building bridges in the 1970s. Its four fabrication plants feature more than 500,000 square feet of enclosed production space and 85 acres of assembly yard. Since the 1990s, they have undergone major facility expansions and expanded their market area well beyond the East Coast. They run two shifts daily in their fabricator bays, with some areas operating three shifts.
The new machine has improved our efficiency and accuracy, aligning our labor estimates with actual hours worked within 15 minutes.
Mike Slein
Shop Supervisor, HSS
HSS is successful not only because they handle large projects but also because of their responsiveness, including urgent work taken with little or no advanced notice. “We are known for our quality and timeliness,” said Maintenance and Facilities Director Barry Miller. “Our company has a reputation for ensuring that our products fit together perfectly when they reach the job site, reducing field issues.”
Challenge: HSS required tight tolerances
HSS predominantly cuts mild steel plates, including grades 588 and 572, with thicknesses ranging from half an inch to 3.5 inches. They required a machine to hold a maximum of 2 degrees of tolerance for lengthy straight cuts.
Solution: Kinetics K5000XMC with a Hypertherm XPR460
HSS upgraded to a new Hypertherm XPR460® plasma cutting machine, which offers improved accuracy, speed, and cut quality. The XPR460 provides the most powerful, high-definition plasma cutting capability to the Kinetics K5000XMC gantry machine and features a multifunctional setup that includes drilling and marking capabilities. The Kinetic cutting table is 185 feet long by 15 feet wide, making it one of the largest on the East Coast.
Business impact: Improved efficiency and accuracy
HSS realized a rapid return on investment by purchasing the Kintetic machine with the Hypertherm XPR460. “The new machine has improved our efficiency and accuracy, aligning our labor estimates with actual hours worked within 15 minutes,” said Mike Slein, Shop Supervisor, HSS. “We also expect the new machine to provide long-term reliability and maintain high performance with proper maintenance and operator training.”