Powermax45 XP cuts repair time in half for concrete manufacturer
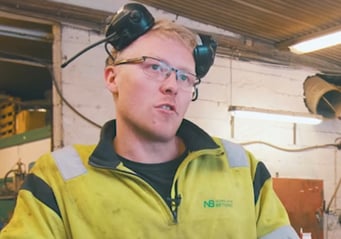
Company overview
Nordland Betong was founded in 1947 in Bodø and is one of Norway’s largest concrete manufacturers. In 2011, Nordland built the most modern factory for field concrete production in Norway. In 2013, Nordland invested further to increase capacity and delivery capability. The company produces prefabricated concrete, coatings, and road blocks for private individuals and large enterprises for projects in the northern region of Norway. Nordland employs 25 people.
Challenge: Grinding molds to prep for welding was slow and cumbersome
Nordland makes both concrete in its fluid form and concrete products such as bricks, road blocks, and various other products used in construction. Steel molds are used to produce the concrete products. Since the quality of the steel molds influences the quality of the concrete products made with them, these molds are fabricated from high quality steel. Despite the high quality of the steel molds, the pressure exerted on these molds sometimes causes them to crack.
In the past, Nordland used a grinder to prepare the cracks for welds, but this process was slow and cumbersome. Sometimes, Nordland would use the grinder for 30 minutes and still not gouge deep enough to make a good weld. This was not efficient or effective.
Solution: Powermax45 XP improves gouging efficiency
To increase gouging efficiency and effectiveness, Nordland chose the Powermax45® XP with gouging capability, using the 75° torch and special gouging consumables. The Powermax45 XP has a low-amp process for precision gouges and a variety of consumable types for specialized cutting and gouging applications. Using the Powermax45 XP with the right torch and consumables, Nordland can achieve smooth, clean, and consistent gouges.
The Powermax45 XP
The Powermax45 XP plasma cutter provides fast cut speeds and automatic gas adjustment for quick, simple setup and operation up to a recommended cut capacity of 16 mm (.625 inch). Duramax® Lock torches support handheld and mechanized cutting of a wider range of metal thicknesses, along with precision gouging such as spot weld removal and marking capabilities. The Powermax45 XP is compact and light weight, enabling flexibility and versatility.
Powermax45 XP benefits include:
- Patented drag-cutting technology makes the Powermax45 XP easy to use – even for first-time operators.
- Smart Sense™ technology ensures that air pressure is always correctly set.
- CNC interface and FastConnect™ torch connection allow both handheld and mechanized operation.
- A wide range of torch and consumable styles is available to choose from based on job requirements.
- Cut speeds are 1.5 times faster than oxyfuel on 6 mm (.25 inch) mild steel.
- Superior cut and gouge quality reduces time for grinding and edge preparation.
- New torch disable switch feature allows faster, easier changeout of consumables.
- SpringStart™ technology ensures consistent starting and optimum torch performance.
The Duramax 75° handheld torch
Designed for durability and reliability with SpringStart technology, Duramax torches are available for handheld and mechanized cutting and gouging as well as robotic cutting. These torches are designed for high-impact and heat resistance, and they perform well even in challenging environments.
Duramax torches are available with an extensive array of specialty consumable options that perform a variety of applications, such as fine feature cutting, extended reach cutting, gouging, flush cutting, and marking. The ergonomic design of the Duramax 75° torch is perfect for normal cutting and precision gouging.
Business impact: Gouging is twice as fast with the Powermax45 XP
The Powermax45 XP has increased efficiency for Nordland Betong, cutting the time they need to spend repairing concrete molds in half. In the past, the Nordland team could spend 30 minutes grinding and still not gouge deep enough to make a good weld. They were spending a lot of time without achieving the desired outcome.
With the Powermax45 XP, Nordland can complete the gouging job – at the correct depth – in just 15 minutes. This time savings gets molds back into production faster, so the company can manufacture their concrete products with shorter production delays.
“One of the advantages of the Powermax45 XP is its efficiency. It reduces the time needed to do the job by half. It gets the molds back into production more quickly and makes it easier for me to gouge.” - Johan Edvard Risnes, Operator, Nordland Betong
Because the quality of the gouges is better with the Powermax45 XP, the quality of the welds is also better. This ensures the molds last longer in production, and higher quality molds result in better concrete products.
Since the Powermax45 XP is versatile and easy to use, with the ability to quickly switch processes, the company also uses the Powermax45 XP for other jobs that come into the workshop. These jobs are easier to do with the Powermax45 XP and are completed more quickly than they were using other processes.