Fought & Company saves time and money with the XPR300
Steel fabricator gains competitiveness in cutting applications
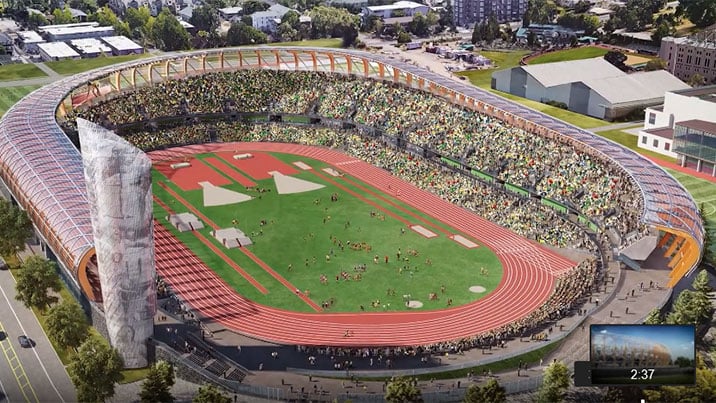
Company: Fought & Company
Fought & Company operates one of the largest steel fabrication facilities in the Pacific Northwest. Founded in 1949, Fought & Company has a rich history serving as one of the most prestigious complex steel fabricators in the Western United States. Their distinguished team of over 300 employees has a reputation as some of the best project management, structural steel, and bridge fabrication specialists in the industry. Their diverse portfolio of projects includes bridges, commercial, hospitals, stadiums, and industrial buildings.
Challenge: Pipe, tube, and plate cutting were not competitive
Fought & Company was struggling to be competitive in pipe, tube, and plate cutting. Most of the structures that they build – stadiums, airports, malls, hospitals, and bridges – have complicated shapes, including wide flange shapes, angles, tubes, round pipes, and other pieces. When cutting complicated or oversized shapes, they would have to lay things out with a template and then carefully cut along the template using an oxygen acetylene torch, a process that is extremely slow and requires a lot of post-cutting grinding.
Solution: The XPR300 enables faster, more accurate, more competitive cutting
Fought & Company switched from an oxygen acetylene torch to automated plasma cutting with Hypertherm’s XPR300® and added Rotary Tube Pro™ software for better tube and pipe cutting.
The XPR300
The XPR300 represents a significant advancement in mechanized plasma cutting technology, redefining what plasma can do by expanding its capabilities and opportunities in ways never before possible. With unmatched cut quality on mild steel, stainless steel, and aluminum, the XPR300 increases cut speed, dramatically improves productivity, and reduces operating costs.
Ease-of-use features and system optimizations make the XPR300 easier to run with minimal operator intervention, lowering labor requirements while ensuring optimal performance and unmatched reliability. The XPR system’s intuitive operation and automatic system monitoring redefine what simple and user-friendly plasma cutting means.
The XPR300 is designed with fewer consoles and easy connections, so operators spend less time setting up and more time cutting.
Additional ease-of-use features include:
-
EasyConnect™ torch lead and one hand torch-to-receptacle connection enable fast and easy change-outs.
-
QuickLock™ electrode delivers easy consumable replacement.
-
Full control of all functions and settings is available via the CNC.
-
Wi-Fi in the power supply enables multiple system monitoring and service from mobile devices.
-
Arc response technology™ provides automatic torch and ramp-down error protection, eliminating the impact of ramp down errors and reducing the impact of catastrophic electrode blowouts which can damage the torch – significantly extending the life of consumables.
-
Sensors in the power supply deliver refined diagnostic codes and significantly enhanced system monitoring information, reducing troubleshooting time and delivering proactive data to improve overall system optimization and uptime.
Rotary Tube Pro
Rotary Tube Pro software makes it easy for anyone to design and cut tube and pipe parts. There is no 3D CAD experience required. Designed for mechanized rotary cutting, Rotary Tube Pro supports stand-alone units and cutting table add-ons, including plasma, laser, waterjet, and oxyfuel machines. In addition, it supports perpendicular cutting as a standard feature and bevel cutting as an optional module.
The software features a parametric design interface that allows main tubes and side-wall cutouts to be added from a list of pre-defined shapes, or users can add tubes and cutouts directly from a CAD program. This flexibility lets fabricators and manufacturers enjoy greater productivity by increasing programming speed and improving cut quality for improved fit-up with fewer secondary operations.
Rotary Tube Pro software delivers optimal outcomes based on factory-tested and proven job parameters, including leads, separations, kerf, feed rate, and cutting techniques.
Enhancements include:
-
3D geometric modeling engine that delivers a faster, more responsive 3D model when entering dimensions and other properties
-
Ability to import STEP file formats (*.step) for the quick exchange of 3D objects from one platform to another
-
Cut sequence enhancements that allow cutting interior parts first and improved sequencing flexibility
-
Simplified bevel material selection in which only materials and classes that can be beveled are displayed
-
New setups, spreadsheets, and machine files that enhance cut quality and accuracy on beveled tubes
Business impact: XPR opens new markets, saves time and money
Fought & Company has improved cutting quality and efficiency with the XPR300, enabling them to pursue more complicated jobs without outsourcing key components and increasing their competitiveness. With the increased speed and accuracy of the XPR300, Fought & Company has secured and completed jobs they would not have been able to compete on before, increasing market share and profits.
Because of the speed and accuracy, we are able to get work that normally we would not be able to get, so we have a higher market share.
Wayne Searle, CEO (retired)
Fought & Company
With Hypertherm’s XPR, jobs that used to take 8–16 hours using a template and oxygen acetylene torch are completed in under an hour, saving over seven hours on each process. The system is also easy to learn, so operators become productive quickly, without requiring extensive training.
With the Rotary Tube Pro, Fought & Company no longer outsources fishmouth cutting, saving time, decreasing costs, and improving efficiency. The Rotary Tube Pro’s ability to nest fishmouth pieces together also saves a lot of material, decreasing material costs and eliminating a lot of waste.
The quality of the parts cut matches the actual dimensions and sizes very precisely with little to no slag, eliminating hours of cleanup and grinding. Operators are able to simply knock a little slag off and move on with the job, saving both time and money.
“One of the things that I like most about the machine is once the product has been cut, it’s done. There’s no more cleanup, there’s no more grinding. You knock a little slag off and go right to work. We save time and money, lots of time and money.” Wayne Searle, CEO (retired), Fought & Company
For example, Fought & Company was able to build one of the world’s largest track and field arenas with components that are not typically part of a regular steel project, including pipes that sit on the backside, big plate columns, and more. Without the XPR300, they would have spent hours cutting, grinding, and hacking things apart, a time-consuming process that would not have enabled them to compete for this project. The XPR300 ensured they could win the contract at a competitive price and complete the job.
Learn how your business can strike the perfect balance between cut quality, cut speed, and cost using the XPR300. Click the button below, fill out the form, and a Hypertherm product expert will contact you.