ProNest software helps Craig Manufacturing meet new challenges
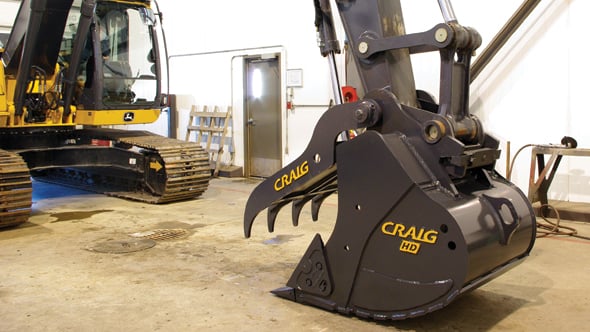
“We’ve reduced our raw material inventory by half. Today, because of ProNest our management is happier because cash tied up in plates has been reduced without sacrificing delivery.”
Colden Wetmore
Operations Manager, Craig Manufacturing
Company overview
Craig Manufacturing of Hartland, New Brunswick, Canada is the largest privately owned heavy equipment attachment manufacturer in North America. The company operates out of a state-of-the-art 71,000-square-foot manufacturing facility in Hartland and a 15,000-square-foot facility in Cambridge, Ontario used for distribution and specialty manufacturing. Craig Manufacturing’s products include hydraulic plows, multi-purpose buckets, pallet forks, snow pushers, crane booms, heavy-duty blades, and more.
Challenge: Existing nesting software was too time-consuming
As business increased at Craig Manufacturing, the need arose for additional cutting capacity. The company’s existing nesting software was too slow, creating a bottleneck in production.
“Our existing nesting software program had its limitations; creating nests was often a time-consuming process. Every hour spent nesting would only produce about one hour’s worth of cutting. The software didn’t have much in the way of automated features, so we ended up with a bottleneck right at the beginning of the process,” said Operations Manager Colden Wetmore.
Solution: ProNest nesting software eliminates bottleneck
The decision team took a close look at the latest Hypertherm solutions, including ProNest® CAD/CAM part nesting software. They were particularly interested in how ProNest would interface with their SOLIDWORKS® 3D CAD and how it would fit into their specific workflow. They also wanted to improve hole quality, so ProNest’s support of Hypertherm’s True Hole® technology was an added bonus.
Before long, Craig Manufacturing’s new EBF plasma table arrived equipped with Hypertherm’s HPR400XD®, EDGE® Pro CNC, ArcGlide® THC, and programmed by ProNest.
“With our prior software, we spent six years tweaking the cutting parameters and never got them right,” said Wetmore, “then here comes ProNest with all the parameters built-in.”
ProNest nesting software
ProNest is an industry-leading CAD/CAM part nesting software designed for advanced mechanized cutting. It offers the highest level of cutting expertise and provides a single solution for all profile cutting needs – including plasma, laser, waterjet, and oxyfuel. ProNest’s powerful, high-yield nesting is designed to supercharge cutting operations, enabling fabricators and manufacturers to increase material utilization, boost productivity, lower operating costs, and improve part quality.
ProNest’s intuitive screens and a wide variety of helpful features make it easy to learn and use. Its faster, fully automated interface can reduce programming time from hours to minutes, while specialized cutting techniques can reduce total cut time by up to 50%.
ProNest is designed to work with virtually any ERP, MRP, or MES program. These integrations can extend ProNest’s efficiencies more broadly across the organization.
Unlimited access to technical support, training, and software updates is included with ProNest, ensuring every user gets the most value from their ProNest software.
True Hole technology
True Hole technology produces significantly better hole quality than what has been previously possible using plasma. True Hole is automatically applied by the nesting software or CNC software to thicknesses up to 25 mm (one inch). Diameter and hole coverage ranges from hole diameter to thickness ratios from 2:1 to as low as 1:1.
True Hole virtually eliminates hole taper, delivering true bolt-hole quality automatically, without operator intervention. Ding is reduced and biased to the outside of the hole. True Hole reduces the need for secondary processes and completes jobs in fewer steps, narrowing the gap with laser hole quality and making the plasma process suitable for many jobs previously cut with laser.
Rapid Part technology
More than half of production time is often spent moving between cuts — time that could be used to cut faster and increase productivity. Rapid Part uses hardware and software features to reduce cycle time, providing more efficient motion and enabling up to a 100% increase in parts per hour. It provides more efficient motion during the cutting process, skipping unnecessary steps and reducing production time by up to 50%.
Rapid Part optimizes three critical aspects of the cutting process and executes them automatically through the CNC.
-
The CAM software optimizes the cut path, minimizing the distance traveled from one cut to the next. It also avoids potential collisions, such as part tip-ups that would otherwise require a time-consuming full head raise (Z-axis) motion to traverse safely.
-
In cases where the torch head must be raised fully, the torch height control features rapid Z-axis/vertical motion capability, including automatic fast-to-slow speed crossover calibration.
-
At the beginning of the initial height sensing or machine motion, Hypertherm HPRXD plasma system gas consoles have gas pre-flow functionality, saving valuable time on each pierce.
Business impact: 19X productivity boost and better cut quality
With the new Hypertherm system, Craig Manufacturing is getting 19 hours of cutting for each hour spent nesting, instead of spending one-hour nesting for each hour of cutting – a 19X productivity boost.
“Since we installed the new table, which includes Rapid Part technology, even our highly experienced operator couldn’t keep up with the increased plate loading and unloading requirements; we had to change our flow to keep up,” shared Wetmore.
ProNest has increased the company’s material utilization and improved cash flow.
Cut quality has also improved. True Hole technology’s improved hole accuracy and quality have significantly reduced secondary grinding operations for the company, increasing productivity even further.
Learn how ProNest nesting software can help your business increase material utilization, cut speed, and cut quality. Click the button below, fill out the form, and a Hypertherm product expert will contact you.