Automating plasma cutting from the river's edge
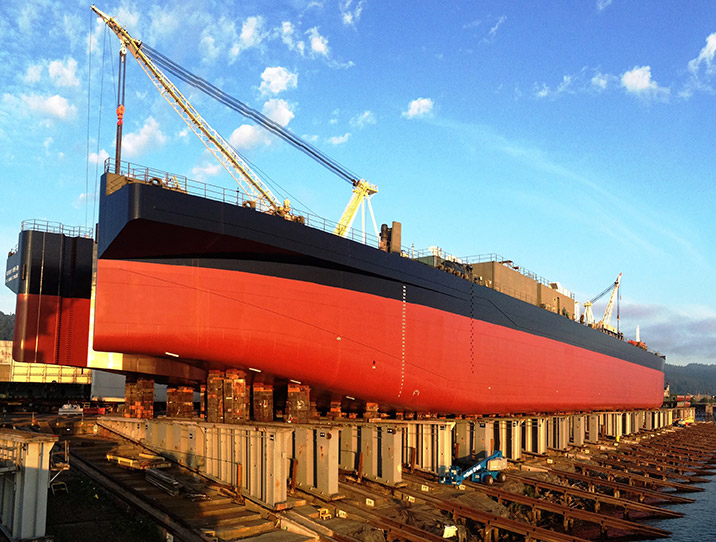
"The new system allowed us to reexamine the way we cut and attached stiffeners to our barges. We were able to change our design; the way we cut the stiffeners. The new way allowed us to increase our weld surface but decrease our weld size. We were able to speed up our welding process. Instead of a three-pass weld, we can now do a single pass weld."
Walt Stokman
Production Coordinator, Gunderson Marine
Company overview: Gunderson Marine
Operating from the largest side-launch shipyard on the West Coast of North America, Gunderson Marine is a deep-water facility, fully equipped for constructing all types of river and ocean-going barges. Gunderson Marine, now part of Oregon Green Manufacturing, LLC, operates a 58-acre industrial waterfront site in Portland, Oregon.
With up to 700 feet of capacity, the company is capable of producing large, ocean-going vessels and conventional deck barges for transporting aggregate, heavy equipment, and other industrial cargo. It has built thousands of marine vessels, including every type of barge imaginable – deck barges, dump scows, oil spill recovery vessels, crane barges, hopper barges, and numerous others.
Challenge: Hand cutting metal was not efficient
For the vast majority of Gunderson's nearly 100-year history, the company built vessels using largely manual methods. Walt Stokman, a production coordinator for the shipyard, describes the process of cutting parts.
"We would cut everything by hand, primarily with an oxy torch. We'd get the material, measure it to length, measure where cutouts needed to be, put down a template, mark the cutouts, cut everything out, and then grind to try and make the cut look halfway decent."
Gunderson managers knew that while their manual method worked, it wasn't very efficient. An initiative to modernize its facilities, coupled with concern for its workers and an ever-worsening shortage of skilled labor, resulted in Gunderson Marine looking at more automated options.
Stokman explains, "Doing all this work manually is not the best for a person's body. You're leaning out over the table, stooping, bending. We knew there were ergonomic improvements we could make. We also realized that we needed to reduce our manning requirements. It's so much more difficult to hire qualified help or even just find people willing to be trained to do this work."
The team at Gunderson knew they couldn't continue to do business the way they had for the past 90 years and stay competitive.
Solution: Hypertherm HyPerformance Plasma speeds up plate cutting
The company began its modernization efforts by adding three large CNC tables to its operation. The tables, equipped with Hypertherm HyPerformance Plasma, allowed Gunderson to significantly speed up cutting flat plate. In addition, the company replaced some of its oxyfuel hand torches with Hypertherm Powermax plasma systems.
The company's modernization efforts didn't end there. Though the three CNC plasma tables made cutting flat plate much more efficient, the company was still doing a lot of manual work. Gunderson searched for a solution that would allow it to cut the many three-dimensional shapes required when building barges, in addition to cutting flat plate.
"We researched quite a few machines, and narrowed it down to four or five before ultimately choosing a 900," Stokman says. "The winning thing for the 900 is that the robot is able to cut on all four sides of the steel, of the structure, so that was nice."
Gunderson chose the SteelPRO 900 made by lnovatech Engineering (now part of Lincoln Electric). It is a dual-purpose system offering both robotic beam line cutting and standard plate cutting. A Fanuc robot holding a Hypertherm HyPerformance Plasma torch can cut all around beams and tubing – along with structural shapes such as bulb flats (a long flat piece of steel with a short, tapered lip on one side), channels, and angles – while the table cuts flat, base, and stiffener plates.
Business impact: Increased efficiency, improved cut quality
Stockman calls the system’s flexibility a huge benefit. "It has the plate table so when we're caught up, we can cut 2-D parts on our plate machine. If we need a rush part, we can just put that on the machine really quickly, or if there is an engineering change, we can quickly cut out a one-off part without interfering. It is very versatile. We can cut just about any shape we can dream up."
The shapes cut from mild steel range from ¼ to 1 inch thick. Once cut, Y-bevels and bolt-ready holes are quickly made using Hypertherm's SureCut technology. Stokman is impressed with the cut quality. “Cut quality is very good, great actually. It exceeds all the standards we need to adhere to. Holes are nice and round; everything's even.”
A job that used to take six people now takes one. Since Gunderson is running three shifts, the savings quickly multiply. This allows Gunderson to move more people downstream – onto welding for instance – helping speed up overall production. Stokman estimates that there are days when the company is putting more than 4,000 lineal feet of material through the lnovatech machine.
The ability to work so quickly is due in large part to the software lnovatech created to work with Gunderson's ship design program. This software, which Stockman says was created for a fraction of the price other vendors wanted, allows Gunderson to easily import files. "We are able to import directly into the nesting software, and then in short order all of our nests are ready and we can cut material."
lnovatech also added code to Hypertherm's ProNest® nesting software to work with Gunderson's specialized cut list. This software alone is credited with saving the company 24 hours of office work each week, while also removing any potential for human error.
Despite all of this automation, the machine's operator still has the ability to change power levels, speed, gas settings, arc voltage, cut height, and pierce height at the operator station. lnovatech's Miquel Clement says, "The Hypertherm units are very well built, so they can change power settings on the fly."
The system is also easy to operate, and operators need very little training to use it. Stokman says, "Training is quick. We've probably trained 20 people. After just two hours, they're on their own and ready to run. It's that simple."
While Gunderson still uses oxyfuel for some jobs – such as trimming a bulkhead – and uses a chop saw for small jobs, most of its cutting is done with plasma. This includes the stiffeners that are so important when building any sort of marine vessel.
The weld is longer but thinner, which Stokman says actually makes for a stronger connection.
Gunderson's decision to continuously innovate has served the company well, and as the company begins its second century in business, Gunderson Marine is well positioned. Robotic cutting with automated plasma technology means the company is more efficient than ever, building more and better barges for years to come.
Learn how Hypertherm’s Hyperformance plasma systems can help your business increase cut speed and improve cut quality while decreasing costs. Click the button below, fill out the form, and a Hypertherm product expert will contact you.