Powermax outperforms disc cutters and oxyfuel for TEi
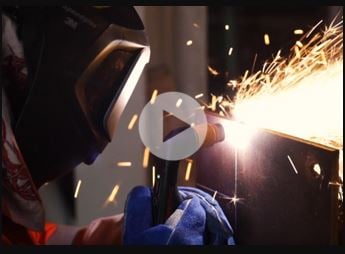
Company Background
Tei, Ltd. is a leading UK engineering construction organization specializing in design, supply, repair, maintenance, and site installation in the power generation and petrochemical industries. TEi has its headquarters in Wakefield and regional offices in South Wales and Kent that provide clients with local access to the complete TEi portfolio.
Challenge: Company experienced cutting challenges using a grinder or oxyfuel
TEi platers face different cutting challenges on worksites based on the type of material they are cutting, the thickness of the material, and the location where they are cutting. Some jobs require cutting on top of machinery like boilers or operating in dead space.
Two of the more common methods of cutting material on worksites are using a disc cutter on a grinder or using an oxyfuel torch. Both of these cutting methods have limitations, so TEi was looking for a better solution.
Using a disc cutter on a grinder can cause permanent damage to operators
Using a disc cutter on a grinder for long periods of time can trigger hand-arm vibration syndrome (HAVS). HAVS is caused by repeated and frequent use of hand-held vibrating tools. It causes changes in the sensation of the operator’s fingers and can lead to permanent numbness of fingers, muscle weakness, bouts of white finger (Raynaud's), and aches and pains in hands and lower arms. The operator may also experience weakening in grip strength.
Oxyfuel is slower, more dangerous, and can’t cut all materials
Oxyfuel can only cut ferrous metal, so it cannot cut materials like stainless steel, aluminum, and nichrome. Oxyfuel cutting is a chemical reaction between pure oxygen and steel to form iron oxide. Cutting with oxyfuel requires the use of a highly flammable fuel gas and an open flame to raise the steel’s surface temperature to approximately 962° C (1,800° F).
Oxyfuel cutting is relatively slow, because each workpiece must be preheated before cutting, reducing productivity. There are also safety issues associated with the use of highly flammable and unstable acetylene, the most common fuel gas used with this process.
Excessive slag is common due to the high temperature required to reach the chemical reaction, and that slag must be removed before parts can be used. Parts cut with oxyfuel can be distorted out of tolerances by the heat, requiring substantial corrections to part geometry. Long and costly secondary processes such as manual grinding and use of filler materials decrease efficiency and part quality.
Solution: Powermax SYNC delivers flexible, efficient cutting
Sunbelt Rentals helped TEi find the right solution, the Powermax SYNC® plasma system. The Powermax SYNC offered the flexibility TEi was looking for and helped overcome the challenges TEi faced cutting a variety of different materials in sometimes challenging locations.
The Powermax SYNC
Powermax SYNC plasma systems feature built-in intelligence and a revolutionary single-piece cartridge consumable, simplifying system operation, streamlining consumable inventory, lowering operating costs, and maximizing cutting performance.
Hypertherm’s single-piece cartridge replaces a traditional five-piece stack-up with one cartridge, making change-outs faster, ordering easier, and inventory tracking simpler. Cartridges are color coded by application, preventing consumable mix-ups and simplifying consumable management. The cartridges also last longer than standard handheld cutting consumables.
The Powermax SYNC uses SmartSYNC® torches. These innovative torches have controls right on the torch, so operators can change cartridges and applications or adjust the amperage without walking back to the power supply. SmartSYNC torches with the Hypertherm cartridge automatically set the correct amperage and operating mode based on the cartridge installed, eliminating setup errors.
Every time the system is used, the torch records information on starts, stops, arc-on time, etc. and sends this information back to the system. Operators can track and analyze usage patterns and use this data to improve cutting operations and identify opportunities for operator training.
Additional Powermax SYNC benefits include:
-
Easily interchangeable torch styles and application-specific cartridge consumables enable a wide range of cutting and gouging applications.
-
Simplified operation minimizes downtime, troubleshooting, waste, and training time.
-
The end-of-life detection feature lets operators know when it is time to change the cartridge consumables.
-
The advanced cartridge consumables last twice as long as traditional consumables for hand cutting.
-
Each application-specific cartridge has been designed to optimize the cutting or gouging process for the best performance possible.
-
The cartridge reader accessory pairs with the Powermax SYNC phone app to analyze performance data such as starts, transfers, and arc-on time.
Business impact: Powermax SYNC’s flexibility overcomes cutting challenges
The Powermax SYNC completely rectifies the problems TEi had using oxyfuel and disc cutters. It is lightweight and portable, so operators are not at risk for HAVS, and they can use the Powermax SYNC in tight spots and challenging locations.
The Powermax SYNC is easy to use with simple automatic system setup. It can cut a wide variety of materials in a wide range of thicknesses – from stainless steel to P91 to aluminum and carbon steel – and supports a variety of applications.
Tom Holloway of Plater said: “The first time I used it, I was cutting some 12 mm carbon steel and then the next piece of material I needed to cut was a 38 mm thick P91 pipe. And it cut both as efficiently and effectively.”
The Powermax SYNC is faster than oxyfuel and grinders, and the quality of the cut is excellent. It is also safer, since it does not require using a highly flammable gas.
“The quality of the cut is excellent, too. It’s very efficient. I find it a lot quicker than using the oxyfuel and the grinder. And it is a lot safer. I am extremely impressed with the Hypertherm Powermax. I believe it is a machine that can be used efficiently and effectively all across the world.”
Tom Holloway,
Plater, TEI
The torch is another thing the TEi team really likes. On most plasma systems, changing nozzles can be tricky. With the Powermax SYNC, the consumables are all in one cartridge. When Tei platers are on a job and they need to change to a different cartridge, even if they are changing from a cutting cartridge to a gouging cartridge, the plater simply takes off the old cartridge, attaches the new one, and it’s done. They don’t have to worry about changing five or six different components.
Hypertherm Powermax also has a QR code right on the system that operators can scan at any time to bring up the website, tutorials, setup instructions, consumables, specifications, and other helpful information. The TEi team appreciates the quick and easy access to helpful information from any location where they are working.
Learn how the Powermax SYNC can help your business strike the perfect balance between cut quality, cut speed, and cost. Click the button below, fill out the form, and a Hypertherm product expert will contact you.
Contact an expert