What is the Powermax SYNC plasma cutting system?
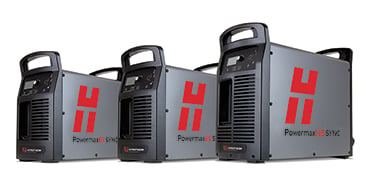
The Powermax SYNC® is a new air plasma platform from Hypertherm. There are three systems in all – the Powermax65 SYNC®, Powermax85 SYNC®, and Powermax105 SYNC®. The Powermax65 SYNC is designed for gouging and cutting up to 20 mm (3/4 inch), the Powermax85 SYNC is designed for gouging and cutting up to 25 mm (1 inch), and the Powermax105 SYNC is designed for gouging and cutting up to 32 mm (1 ¼ inches). Typical applications include drag cutting, bevel cutting, fine feature cutting, extended reach cutting, and gouging.
Powermax SYNC makes plasma cutting easier
Powermax SYNC plasma systems feature built-in intelligence and a revolutionary single-piece cartridge consumable, simplifying system operation, streamlining consumable inventory, lowering operating costs, and maximizing cutting performance.
Instead of five consumable parts, Powermax SYNC systems with their included SmartSYNC® torch need only one! You don’t need to worry about finding and grabbing the right consumable parts. All you need to do is grab ONE color-coded cartridge, screw it onto your torch, and start cutting. Your SmartSYNC torch will automatically adjust the amperage and choose the right cutting or gouging mode. Your torch will also tell you when the cartridge consumable is worn out and needs to be replaced. You no longer need to check by unscrewing the stack-up and looking at the electrode.
Easy to use
-
One-piece cartridge eliminates consumable confusion and makes inventory management easier.
-
Color coding helps you easily locate the consumable cartridge you need.
-
SmartSYNC torcheliminates errors by automatically setting the correct amperage and operating mode.
-
End-of-life detection lets you know when a new cartridge is needed.
Minimizes operating costs
-
Simplified operation cuts down on downtime, troubleshooting, waste, and training time.
-
Cartridge provides up to twice the life for handheld cutting and improved, consistent cut quality in mechanized setups.
-
Cartridge data helps you track performance and analyze usage patterns.
Maximizes performance
-
Interchangeable torches and application-specific cartridges allow you to tackle a range of jobs.
-
Time-saving controls directly on the torch allow you to adjust amperage and change the cartridge consumable without returning to the power supply.
-
Each cartridge has been designed to optimize the cutting or gouging process for the best performance possible.
-
Cartridge reader accessory pairs with Powermax SYNC smartphone app to analyze performance data such as starts, transfers, and arc-on time.
Industry-leading reliability
-
Engineered for rugged, industrial environments.
-
SpringStart™ technology ensures consistent starting and a more reliable torch.
SmartSYNC torches
With simple, twist-on consumable installation, and convenient power and amperage adjustment controls on handheld models, SmartSYNC torches allow the operator to change consumables and applications without returning to the power supply. This reduces consumable change time to about 10 seconds and automatically sets the system for the cartridge – minimizing downtime, troubleshooting, waste, and training time.
SmartSYNC 75° and 15° hand torches are well-suited for a variety of applications, such as gouging, fine feature cutting, extended reach cutting, and flush cutting.
Hypertherm’s revolutionary cartridge consumables
Hypertherm cartridge consumables replace traditional five-piece consumable stack-ups with one-piece, color-coded, application-specific cartridges. Technology embedded in each cartridge automatically sets the correct amperage, air pressure, and operating mode for that cartridge’s application, eliminating setup errors.
Each cartridge is manufactured as a single piece, so everything within it is perfectly aligned and optimized. All consumable components in the cartridge wear at the same rate. As a result, Hypertherm cartridges last up to twice as long and deliver cleaner cuts versus traditional consumables. The cartridge can even track data, like starts and arc-on time, to identify trends and make a user’s operation more efficient.
Hand cutting with yellow cartridges
Yellow cartridges are designed for hand cutting, including drag cutting and FineCut®. With drag cutting, the operator can drag the torch right on the metal using Hypertherm shielded consumables. The operator does not have to worry about having a steady hand and can simply drag the torch along a straight edge or template – in most cases, resulting in a more accurately cut piece.
FineCut consumables are ideal for cutting intricate, fine-featured shapes out of thin sheet metal. They are specifically engineered to provide squarer edges, tighter tolerances, and a narrower kerf on thin metals and are used by artists and job shops with intricate, custom jobs.
Gouging with green cartridges
Green cartridges are used for gouging applications. Plasma gouging melts surface metal while a gas jet blows the molten metal away from the workpiece without piercing or severing it. Gouging is frequently used to remove unwanted metal in preparation for welding and casting.
-
Maximum Control cartridges are used for more precise metal removal, light material washing, and when a shallow gouge is desired.
-
Maximum Removal cartridges are used for aggressive metal removal applications, deep gouge profiles, and extreme metal washing.
Flush cutting with black cartridges
Black cartridges are used for flush cutting and other specialty applications. Flush cutting is used to remove attachments, protrusions, or fixtures from the surface of a base material without cutting or damaging the base material. Typical applications include removing lifting lugs, pad eyes, and temporary welded supports used for material handling; end cap removal; bolt and rivet removal; and removing work platforms and ground attachments.
Mechanized cutting with gray cartridges
Gray cartridges are for mechanized applications or if you prefer to hold a manual stand-off when hand cutting. Mechanized applications can increase the productivity of cutting operations because mechanized cutting equipment can operate at faster speeds than manual cutting tools. They can also improve cut quality and consistency since programmed machines can repeatedly make precise, consistent cuts.
Learn how Powermax SYNC’s built-in intelligence and revolutionary single-piece cartridge consumable enable simpler, more efficient, and more profitable cutting operations. Click the button below, fill out the form, and a Hypertherm product expert will contact you.
Contact an expert