Sometimes when troubleshooting plasma cut quality, it's not the plasma that’s the problem
Five reasons why table slats are so important
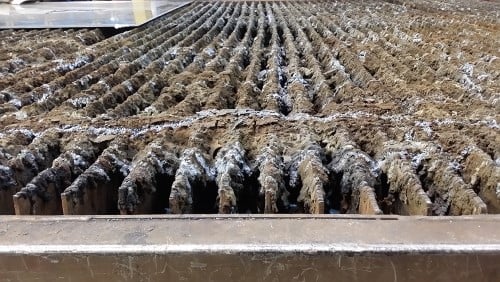
None of us want to sleep on a lumpy mattress, and if we did, we wouldn’t expect to get a good night’s sleep. It’s the same with cutting beds. When slats are worn, bent, or covered in dross, the plate isn't level, so it’s impossible to get a good cut.
Table slats are just strips of metal. Their functionality is basic in comparison to the operation of a plasma system, nevertheless, table slats impact plasma system performance almost as much as the plasma arc itself. That’s because smooth slats support and level your metal plate, and they are critical for maintaining the proper torch height and cut angle throughout the cut. Plus, when the torch-to-work distance is accurate, you avoid torch collisions to maximize cut speed and eliminate rework when the plate comes off the table.
The truth about slats
Table slats are perfectly smooth and level when a new cutting machine arrives, but with use, molten metal gradually forms along the top and sides of the slats. This metal or slag build-up creates peaks and valleys that can destabilize the plate, making it impossible to level. Then there is the general weight of plate metal. A heavy plate will cause slats to bow, bend, and warp. Lastly, if you are cutting standard parts in the same position, over the same slats, the repeated cut path will remove the slat’s top edge completely, making it useless.
The benefits of maintaining your slats
Slats are literally the foundation of plasma cutting and no amount of plasma optimization can counteract an offset plate. Therefore, it’s critical for owners and operators to regularly clean the slats, and to replace them when there is excessive wear or distortion. Getting into the habit of inspecting your slats is an important part of plasma cutting and your routine maintenance schedule. A commitment to maintaining your slats will benefit you and your business in several ways:
-
Better cut quality - You will reduce angularity for consistently straighter cuts.
-
Better system performance - Your torch-height-control can maintain the proper torch-to-work distance for better cut quality.
-
Longer consumable life - Consumable life will not be wasted on slag, misfires, or bad cuts. Good consumables will not be damaged prematurely by molten metal blowing back on the shield or through collisions with the plate.
-
Greater productivity - You will reduce processing time and material waste.
-
Lower operating costs - You will save money on consumables, materials, and labor.
Some best practices
There are some practices that will keep your table slats in optimum shape. The first step is to do a quick visual inspection before you even put a plate on the slats. If you have a water table, you may need to siphon off some of the water so you can see your slats. Then remove slag and replace slats that are bent or worn.
Step two, before cutting begins, think about your nest arrangement and pay attention to the cut path throughout the nest. It might make sense to reconfigure the parts between plates, so the cut paths are varied. If you have a much larger cutting area, you can move the plate to different spots on the bed to avoid always cutting in the same place.
Third, put your plate on clean and level slats. We admit slat maintenance isn’t a fun task, but we hope the list of benefits will help make the value of that work more obvious. Your table manufacturer should have more specific advice on how to maintain your table’s slats. Reach out to them for their suggestions.
Fourth, always keep a full set of replacement slats on-hand. You can buy new slats directly from your table manufacturer or even make your own. If you choose to make your own, we suggest first contacting your OEM for the fabrication specifications and requirements.
Still have questions?
We hope this post provided some solid insights. The condition of your slats will impact the plasma cutting process, and with routine maintenance, you will save money and yourself from unwanted headaches.
If you do still have questions, please contact your table manufacturer for assistance.