Things to consider when shopping for a cheap plasma cutter
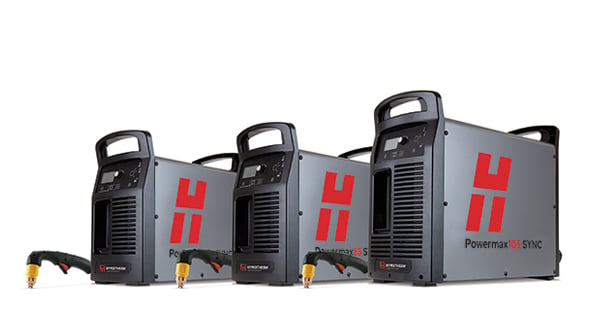
There are many things to consider when buying tools for your trade, and a plasma cutter is no exception. But before you buy the cheapest plasma cutter you can find, you should consider a few critical factors. Whether you are a hobbyist or a professional, this article will cover the key elements you should keep in mind when shopping for the best cheap plasma cutter on the market.
How much does a plasma cutter cost?
The price range for air plasma cutters can vary from a couple hundred to several thousand dollars, so before we review the things you should look for when buying a plasma cutter, let’s begin by explaining why there is a such a wide range in prices.
Power supply design
Typically higher quality systems – like Hypertherm’s Powermax® brand of plasma cutters – are designed with fewer parts, more robust components, and a design that separates sensitive components from metal dust that can cause premature wear. In other words, these systems are built to last and provide good value for your money. Cheap plasma cutters on the other hand use cheaper components that are nowhere near as robust as those found in higher quality systems.
If you were to remove the metal cover from one of Hypertherm’s Powermax plasma cutters you will quickly notice a couple of things. You’ll notice how empty the inside looks. There actually aren’t a lot of parts inside it. This is because the system is engineered using a methodology called Design for Manufacture and Assembly or DFMA. DFMA calls for engineers to identify, quantify, and eliminate waste or inefficiency in a product design. In addition, you’ll notice that the system has two sides, a clean side where the control board is located, and a dirty side where the fan is located.
Because there are so many cheap plasma cutters on the market, it is impossible to describe the inside of every single one of these systems. Generally though, the inside of these systems can resemble a birds nest with a tangle of parts and wires. Now, you might be thinking, “So what? Why does it matter what the inside of my plasma cutter looks like?” It matters because more parts means that you have more parts that can fail. And when a part does fail, it’s going to be much more difficult to fix because you’ll need to sort through a tangle of components to find the part that needs to be replaced.
Torch and consumables
Another big difference between the cheaper plasma cutters and more expensive ones are the torch and consumables. Cheap, low-cost plasma cutters use older—in some cases 30-year-old—torch and consumable technology. If you were to look closely at the torches of the best cheap plasma cutters, you’d notice that they all look the same. The torches might have different colors, but the underlying design is the same. The torch and consumables on higher quality systems are engineered to work together with the plasma system it was designed for. They are tested with the power supply and optimized to work best with the power supply’s output characteristics. This is important because of the extremely high temperatures created when plasma cutting.
Unless you have a Powermax SYNC™ plasma or Hypertherm adapter that allows you to use a single-piece cartridge consumable, you will need to install the following five consumable parts onto the end of the plasma torch:
- Electrode
- Nozzle
- Shield cap
- Swirl ring
- Retaining cap
Once your parts are on the torch, and you squeeze the trigger, an ionized gas arc will form between the electrode and nozzle. Energy is then added to that electrical arc to increase the temperature up to 13,871 degrees Celsius (25,000 degrees Fahrenheit.) After that, the arc is forced through a copper orifice to make the arc perfectly round and increase its velocity. The consumables you use need to withstand these hot temperatures without melting. Cheap consumables are cheap because they are not thoughtfully designed or carefully manufactured. They are not manufactured with the tolerances needed to ensure the consumables can withstand the extremely high temperatures caused by a plasma arc, and as such, wear out very quickly, typically after 120 to 250 starts. Consumables on more expensive, high-quality systems will withstand thousands of starts before needing to be replaced. Bottom line: Although cheap consumables cost less, they will cost you more in the long-run because you need to buy many more sets to equal the life of one good quality consumable set.
Consumable life-span is just the beginning though. You also need to consider cut quality. To do that, let’s explain how the arc impacts each of the five consumable parts. As mentioned earlier, when plasma cutting, you have a 13,871 degrees Celsius (25,000 degrees Fahrenheit) plasma arc passing through a tiny hole in a copper nozzle. Copper melts at about 593 degrees Celsius (1,100 degrees Fahrenheit) so high-quality torches are designed so the air flow that goes through the swirl ring and enters the inner chamber of the nozzle provides a unique and accurate gas swirl pattern. This acts as a centrifuge, slinging the cooler and heavier molecules of gas to the outside of the nozzle bore where they create a cool, nonconductive boundary layer that protects the copper nozzle from melting. There is an attempt to do this with the older technology torches, but it does not work nearly as well as a great deal of engineering expertise is required. In addition, higher-quality torches use a patented technology called conical flow technology. This technology cools the orifice exit and increases the arc energy density which results in a narrower, more concentrated arc and therefore better cut quality.
The electrode is another critical part. During steady state cutting the electrode emitter, which is a small slug of hafnium, remains in a molten state. When you release the trigger after a cut the post flow cooling air pulls a small slug of that molten hafnium and spits it out through the nozzle orifice. After 120 to 250 cycles with a cheap plasma cutter torch, most of this hafnium is gone. You’ll start seeing cuts with a lot more angularity and dross, and soon after that, a green flame emitting from the torch when the copper part of the electrode is consumed. High quality systems are designed to ramp the air pressure up and down and minimize thermal shock to the electrode when it goes from room temperature to 1,648 degrees Celsius (3,000 degrees Fahrenheit) at the beginning of a cut. If does something similar at the end of the cut. It ramps down at the trigger release so that the hafnium can re-solidify. Each power level and power supply / torch design require different microprocessor-controlled profiles, and that is one reason why torches and power supplies should be jointly designed by the same team of engineers. It helps to ensure longer consumable life and better cut quality.
Durability and reliability
Now, let’s talk about durability and reliability. Hypertherm’s Powermax systems are industrial machines designed to withstand harsh conditions and last for decades. When engineering a new system, alpha units undergo months of reliability testing. Technicians in our reliability labs modify the systems so the amperage is 10 percent higher than what the units are designed to withstand. These systems are then subjected to temperatures and humidity levels that are up to 30 percent higher than the design specifications. In addition, all of these units undergo a series of tests. We shake them, bake them, introduce large amounts of dust, and then drop them. All of these units are fired up and do actual plasma cutting under these conditions. Our technicians purposely stress these units until they fail. They then dissect the failure, re-engineer parts if needed, and return the unit to the testing chamber and repeat the same tests. These torture tests continue for upwards of 18 months until there are no more failures. This makes for long new product development cycles, but very reliable products.
In summary, all plasma cutters have one thing in common, they cut metal rather fast and rather economically. However, there is a wide performance and reliability delta between the best cheap plasma cutters and high-quality plasma cutters like those from Hypertherm.
Does everyone need a high-quality plasma cutter for their hobby shop? No. The purpose of this article isn’t to convince you otherwise. Rather, it is to ensure you understand what you are buying if you choose to buy a cheap plasma cutter.
Factors to consider when buying a plasma cutter
Picking the right system from the fairly wide price range will depend on the intended use and the frequency of use. Do you need a system to complete an occasional project around the home or do you need something capable of withstanding regular use? Here’s a look at the factors you should consider when out shopping for the best cheap plasma cutter. The following assumes you already have a general idea of the type and size of plasma cutter you need. If not, you may want to start by reading how to choose the best plasma cutter for your needs.
Starting method
There are two main methods used to start a plasma arc. Plasma systems will either use a high-frequency start or a so-called blow-back start. The high-frequency start is the older and less desirable method because it can interfere with sensitive electronic equipment, such as a computer, and poses a risk of electrocution. For these reasons, the most common method used today, and the method you want, is the second method. The blow-back start method uses air pressure to push the electrode back toward the nozzle and create the plasma pilot arc. It is much safer and more reliable than other methods which is why most plasma cutters, even cheap plasma cutters, will use this method. Still be careful when shopping, as you will occasionally find cheap plasma cutters that still use a high-frequency start.
Power output
When buying a plasma cutter, manufacturers and shoppers tend to focus on amperage. The thinking is that amperage defines the relative cutting power of a system and that all 40-amp systems will have roughly the same amount of power. Unfortunately, this thinking is flawed. In reality, the true power of a plasma cutter is determined by the wattage. Though manufacturers rarely advertise the wattage, it is easy calculate. All you need to do is multiply the amperage by the load voltage capacity of the plasma power supply. Here’s what that looks like.
amps x volts = watts
This is good to know when shopping for a cheap plasma cutter or any plasma cutter, actually. Let’s say you come across a 40-amp plasma cutter on Amazon. When you read the fine print, you’ll notice that it can provide a safe load voltage of 96 volts. Here’s the math:
40 amps x 96 volts = 3,840 watts
Now, let’s look at the cheapest and smallest amperage plasma cutter that Hypertherm makes: the Powermax30® XP. That system has 30 amps and 125 volts which, when multiplied, equals 3,750 watts. Despite, having 10 more amps, you’ll see that the 40-amp plasma cutter actually has almost the same amount of power as the 30-amp Hypertherm.
The same is true of the Powermax45® XP. Though you might be tempted to compare the Powermax45 XP to a 40-amp system when shopping, in truth, Hypertherm’s 45-amp plasma cutter is more similar to a 60-amp system from most manufacturers. In fact, the Powermax45 XP has a higher wattage output than almost all of the 60-amp cheap plasma cutters available today. This wattage is what controls the effective length of the cutting arc and the thickness you can cut.
Duty Cycle
After the starting method and wattage, you will want to consider the duty cycle, which is the amount of time you can continuously use a system before taking a break. In theory, a system with a 100 percent duty cycle can run for 10 out of 10 minutes, while a system with a 50 percent duty cycle is designed to run for 5 out of 10 minutes, and so on. Unfortunately, determining the true duty cycle of any system is tricky because there is no agreed upon standard among manufacturers. Though many use International Electrotechnical Commission standards, there is no law that says they must. Two different manufacturers can come up with different duty cycle ratings for the exact same system. We are not in the position to speak for other manufacturers, however, do have the following guidance: When shopping for a cheap plasma cutter, ask how the manufacturer arrived at their advertised duty cycle. This is the best way to know if you are truly getting what you are paying for.
Ease of service and part availability
One last consideration you want to consider when out shopping for the best cheap plasma cutter is ease of service and part availability. You need to ask yourself how easy will it be to fix this system when something goes wrong. In most cases, you’ll discover a cheap plasma cutter is not easy or worth the money to fix. You are likely better off returning it if it’s still under warranty, or scrapping it and buying a new cheap system. As far as part availability, we are talking specifically about consumables. How easy will it be to find consumables for the system you buy? Does the manufacturer seem stable? Do you expect it will continue to manufacture consumables for your system? As an aside, Hypertherm guarantees it will support all of our plasma systems for at least seven years from the date a system is discontinued. Further, we often introduce retrofit torches and adapters that will allow owners of older systems to enjoy at least some of the benefits of our newest technology like the Hypertherm cartridge consumable shown above.