Plasma cutting vs laser cutting: a guide
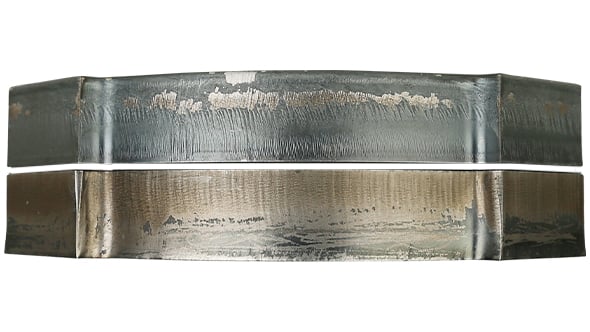
If you’re thinking about purchasing a plasma cutter or fiber laser cutter, there are several factors in determining which cutting technology is best suited for your production environment, including capital investment, metal thickness, cut quality, and speed. Additionally, surface, maintenance, and operating costs should be considered. Depending on the job, plasma cutting and fiber laser cutting each offer advantages.
First, let’s understand what makes cutting technologies different.
What is plasma cutting?
Plasma cuts through electrically conductive materials like steel, aluminum, and other conductive metals by creating an intense heat, ionized gas known as plasma, capable of melting and blowing away the cut material. This is typically achieved using a plasma torch that directs the high-velocity plasma electric arc onto the workpiece, resulting in precise and efficient metal cutting. Plasma cutting is a metal fabrication process commonly used in manufacturing, construction, and automotive industries for its speed and accuracy. Plasma cutting can be accomplished with handheld torches or using a computer numeric control (CNC) with a table for automated cutting.
Types of plasma cutting
Each method of plasma cutting has its advantages and is chosen based on the specific requirements of the cutting application, the material being cut, and the desired cut quality.
Conventional plasma cutting
Conventional plasma is the most common type of plasma cutting and is when a plasma arc is generated between a negatively charged electrode and a positively charged workpiece.
Precision plasma cutting
Precision plasma cutting is a more refined version of conventional plasma cutting. It provides a narrower and more precise cut, making it suitable for applications requiring tight tolerances, such as automotive and aerospace industries.
High-definition plasma
High-definition plasma cutting is often used for applications that demand the highest level of precision. It uses advanced technology to produce high-quality cuts with narrower kerfs and reduced bevel.
Water-injected plasma cutting
Water-injected plasma cutting injects water into the plasma arc, which cools the electrode and nozzle, extends consumable life, and reduces fumes and noise. It’s often used when cutting materials prone to warping or requiring minimal heat-affected zones.
Dual-gas plasma cutting
Dual-gas plasma cutting enhances cutting speed and quality when working with steel. It uses oxygen as a secondary gas to aid in cutting ferrous types of metals (e.g., steel), while the primary plasma gas (typically nitrogen or air) creates the plasma arc.
Fine plasma cutting
Fine plasma cutting utilizes a small nozzle and a low-power plasma arc to make precise cuts. This method is commonly used in applications like artwork and small-scale metalworking.
What conditions make plasma a strong cutting choice?
Plasma cutting is a versatile and effective method that excels in many cutting applications. Its suitability is influenced by factors such as the material to be cut, the thickness of the material, the required precision, and the desired cutting speed. Evaluating these conditions and requirements will help determine whether plasma cutting is the right tool for a particular cutting task.
Some of the conditions that make plasma cutting a preferred choice include:
Electrically conductive materials
Plasma cutting is highly effective on electrically conductive materials such as steel, stainless steel, aluminum, copper, brass, and other metals.
Thickness of materials
Plasma cutting is well-suited for cutting a wide range of material thicknesses, from thin sheets to thick plates, and excels over fiber laser at cutting thicknesses over 16 mm (5/8”).
High cutting speed
In high-volume production environments or when rapid cutting is required, plasma cutting is an excellent choice. Its high cutting speed can significantly increase productivity.
Precise and intricate cuts
Plasma cutting can achieve high levels of precision and make intricate cuts with minimal kerf width, making it suitable for applications that demand accuracy and complex shapes.
Minimal heat-affected zone (HAZ)
When minimizing the heat-affected zone, which can lead to material warping or distortion, plasma cutting's ability to produce a relatively small HAZ is advantageous. This is especially true when using water-injected plasma cutting.
Clean cuts
Plasma cutting produces sharp cuts with minimal dross (residue). This produces a better surface finish, reducing extensive post-cutting cleaning or finishing processes and minimizing material waste.
Versatility
Plasma cutting can handle straight-line cuts to bevels, holes, and shapes. Its adaptability to different applications and variety of materials makes it a valuable choice for flexibility.
Portability
Portable plasma cutting systems allow for on-site cutting and repair work. This portability is valuable in construction, shipbuilding, maintenance, and repair operations.
Automation
Plasma cutting can be easily integrated with CNC systems for automated and precise cutting of complex shapes and patterns. This is ideal for industries that require high-volume production or customized components.
Cost effective
Plasma-cutting equipment is cost-effective compared to some other cutting methods. The consumables, such as electrodes and nozzles, are often more affordable. The high cutting speed and minimal post-processing also help reduce production costs.
Safety
Plasma cutting is considered a safer method than some alternatives, including fiber laser, as it doesn't rely on flammable gases for cutting and carries less risk of eye damage.
Environmental considerations
Plasma cutting generates less smoke and fumes than other cutting methods, making it a more environmentally friendly choice regarding air quality and workplace safety.
What is fiber laser cutting?
Laser cutting is a high-precision and versatile technology that uses a focused beam of light (or laser beam) to cut, engrave, or mark various materials. It’s widely used in industrial, commercial, and even hobbyist settings for applications ranging from cutting metal and plastics to etching intricate designs on wood or ceramics. Fiber laser is an improvement on the older technology of Co2 laser.
Types of fiber laser cutting
Several types of fiber laser cutting are based on different factors, including the power output, capabilities, and specific applications. Here are some of the common types of lasers:
High-power fiber laser
High-power fiber laser cutting machines typically have laser sources with power outputs ranging from 1,000 to 15,000 watts or more. These machines can cut thick materials, including steel and aluminum, at high speeds.
Medium-power fiber laser
Medium-power fiber laser cutting machines have power outputs of 300 to 1,000 watts and can handle various materials and thicknesses.
Low-power fiber laser
Low-power fiber laser cutting machines have power outputs below 300 watts and are well-suited for applications that require high precision and fine detail.
High-speed fiber laser
Some fiber laser cutting machines are specifically optimized for cutting thin sheet metals. They’re designed to provide high-speed and high precision cutting for materials like thin metals, plastics, and foils.
What conditions make fiber laser a strong cutting choice?
Fiber laser cutting is a good choice for some cutting applications. It excels in very specific conditions and situations.
Here are the conditions that make fiber laser cutting a strong choice:
Material compatibility
Fiber laser cutting is effective on various materials, including metals (steel, aluminum, copper), non-metals (plastics, composites), and some reflective materials.
Precision and accuracy
Fiber lasers offer high precision and accuracy, making them ideal for applications requiring fine detail, tight tolerances, and intricate cuts.
Speed
Fiber laser cutting can be faster than other cutting methods for thin-thickness materials.
Versatility
Fiber lasers can handle a broad range of thicknesses, from thin foils to thick plates. They’re versatile enough to cut, engrave, and mark materials, offering a variety of applications within a single machine.
Minimal heat-affected zone (HAZ)
Fiber lasers produce a small HAZ, which reduces the risk of material distortion or warping. This is crucial for heat-sensitive materials like thin metals or precision components.
Complex Shapes
Fiber lasers can cut complex and intricate shapes, making them a valuable choice for industries that require customized parts and designs.
Automation
Fiber laser cutting systems can be integrated with CNC systems for automated, repeatable, and efficient cutting processes. This is beneficial for high-volume production and minimizes human error.
Reduced Material Waste
The precision of fiber lasers minimizes material waste, making it a cost-effective choice for companies looking to reduce material costs and environmental impact.
Non-Contact Cutting
Fiber laser cutting doesn't involve physical contact with the material, reducing wear and tear on cutting tools and eliminating the need for tool changes.
When to choose plasma cutting over laser cutting
Choosing between plasma cutting and laser cutting depends on several factors, and it's essential to consider the specific requirements of your project, the materials you are working with, and your budget.
Here are key factors when plasma cutting is the better choice over fiber laser:
Metal Thickness
Plasma excels over fiber laser in thicknesses over 16 mm (5/8″).
Cutting Speed
Especially when cutting metals over 16 mm (5/8”), plasma cuts faster than fiber laser. This translates to higher productivity, fewer bottlenecks, better on-time delivery, greater cash flow, and potential for business growth.
Cutting Surface
Plasma delivers a surface finish that’s generally smoother than fiber laser in thicknesses over 16 mm (5/8″) and has consistent cut edge quality over the life of a consumable set.
Cut Quality
Plasma can achieve cut quality that rivals laser across mild steel, stainless steel, and aluminum.
Maintenance
Plasma’s most significant attributes are its simplicity, robustness, and reliability. Maintenance is straightforward, and typically, in-house maintenance departments can easily manage all but the most complex procedures. You can expect a long machine life when you purchase a high-quality plasma cutter. Fiber laser, with fewer power source components, is more reliable than older laser technologies. Still, maintenance is critical for these machines and requires specialized technicians to inspect, adjust, and maintain the system regularly.
Capital Investment
The initial investment for a plasma cutting machine is typically 2-5 times less than a fiber laser cutting system. While that may seem like a one-time cost, the depreciation charges to your firm’s income statement will significantly increase your fiber laser system's total cost of ownership (TCO) for years.
Consumables & Operating Cost
When considering the direct operating costs of a cutting operation, plasma typically costs less per foot/meter for thicker materials due to refined processes and reduced gas consumption. Even where fiber laser direct operating costs are lower, as with thin metals, the electricity consumption and gas consumption requirements of the fiber laser system will cost more vs. plasma cutting systems.
How X-Definition plasma changes the equation
The Hypertherm XPR® plasma family represents the most significant advancement in mechanized plasma cutting technology. X-Definition® technology significantly enhances the capability of Hypertherm plasma to deliver significant gains in cut quality on mild steel and expand the cutting outcomes on a broad range of stainless steel and aluminum applications.
Benefits of XPR plasma cutting systems
- Industry-leading cut quality with X-Definition
- Optimized productivity and lower operating costs
- Engineered system optimization