Study proves the efficiency of plasma cutting in the maintenance of oil and gas refineries
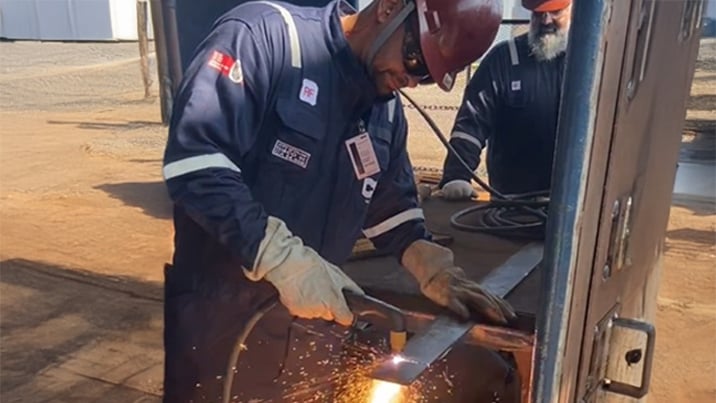
The study prepared by Hypertherm field research, in conjunction with Hypertherm Associates, concludes that processes using plasma technology are 8 times faster and provide safer working conditions when compared to other technologies.
The oil and gas sector has been one of the main pillars of the economy. In this scenario, there is an increasing search for solutions and processes that meet the demands for safety, efficiency, and productivity gains.
In 2024, Hypertherm Associates participated in a study that proves that the use of plasma cutting, compared to oxyfuel cutting and abrasive discs, in the maintenance of tanks in oil refineries can improve productivity and safety, help reduce costs, and improve worker health.
“The study shows that in terms of productivity, plasma cutting is up to 8 times faster than oxyfuel cutting. A process normally taking 6 hours can be completed in 18 minutes. We are talking about saving time and resources and improving quality because plasma also provides quality cutting,” says Gerson Santos, Strategic Manager at Hypertherm Associates. “Today, approximately 90% of cutting operations in refineries use oxyfuel cutting and 10% use abrasive discs for maintenance. Plasma can be used more efficiently in all of these processes.”
Other benefits of plasma cutting in refinery maintenance
The study also provides other essential indicators, including plasma cutting, which enables less exposure to particles and helps workers avoid health problems such as bronchitis, dizziness, lung diseases, and even carbon monoxide poisoning. The technology also prevents injuries due to lower weight and eliminates the risk of accidents due to possible breakage of the discs.
Furthermore, replacing oxyfuel cutting with plasma cutting offers other significant advantages:
-
Cut quality: Plasma cutting provides cleaner, more accurate cuts, reducing the need for rework and finishing.
-
Material versatility: Can cut a wide variety of metals, including stainless steel and aluminum
-
Reduced Heat Affected Zone (HAZ): Generates less heat, minimizing thermal distortion and preserving the mechanical properties of the material.
-
Safety and handling: Does not require flammable gases, which increases operational safety.
-
Operating cost: Lower long-term costs due to reduced maintenance.
-
Automation: Easily integrated with automated and robotic systems, increasing consistency and efficiency.
-
Waste reduction: Plasma cutting’s precision reduces material waste.
These factors underscore the importance of investing in advanced technologies that improve productivity and safety and promote a more sustainable and economically viable operation.
Implementation and adaptation
To maximize the benefits of plasma cutting, oil refineries and other gas facilities must adopt appropriate training programs for their operators. This ensures that staff are well-prepared to utilize the technology efficiently and safely. Additionally, preventative maintenance and regular calibration of plasma cutting equipment are crucial to ensuring longevity and optimal performance.
Economic and environmental
From an economic perspective, transitioning to plasma cutting technology can represent a significant initial investment. However, the long-term benefits, such as reduced operating costs and improved productivity, more than offset this investment. Reduced material waste also contributes to a more cost-effective operation and reduces environmental impact, aligning with corporate responsibility and sustainability practices.
Industry feedback
Several companies in the oil and gas industry have already begun to experience the benefits of plasma cutting. Field reports indicate general satisfaction with the improved efficiency and safety of processes. Specific case studies reveal that companies that have adopted plasma cutting technology have reported a significant reduction in downtime and an increase in the quality of their end products.
Vision for the future
As plasma cutting technology evolves, the oil and gas industry must remain open to innovation and adaptation. Integration with emerging technologies such as artificial intelligence and automation can provide new opportunities to improve the efficiency and safety of operations further.
In short, by adopting plasma cutting technology, oil and gas refineries can position themselves at the forefront of industrial innovation, ensuring more efficient, safer, and sustainable operations. This is a key step in ensuring that the industry thrives in an increasingly competitive and regulated global environment.
With the growing demand for efficiency and safety, plasma cutting is emerging as an essential technology for oil and gas refineries. By adopting this technology, the industry can ensure a safer, more productive, and sustainable future, benefiting companies, workers, and society.
For the oil and gas sector to take full advantage of the advances provided by plasma cutting, ongoing collaboration between companies, regulatory bodies, and research institutions is essential. This synergy will help develop and implement standards and best practices and promote the education and training needed to optimize the use of this technology.
Next steps
Oil refineries and other gas facilities looking to migrate to plasma cutting technology should consider the following steps:
-
Needs assessment: Conduct a detailed analysis of current operations to identify areas where plasma cutting can be most beneficial.
-
Training investment: Provide comprehensive training for operators and technicians, ensuring they are well-informed on best practices and safety procedures.
-
Maintenance and support: Establish a preventative maintenance plan for plasma cutting equipment to ensure its longevity and efficiency.
-
Technology integration: Explore opportunities to integrate plasma cutting with automated and robotic systems, further increasing the efficiency and accuracy of operations.
-
Performance monitoring: Implement monitoring systems to continually assess plasma cutting performance, identifying opportunities for continuous improvement.
By following these steps, oil and gas refineries can accelerate the adoption of plasma cutting technology, reaping substantial productivity, safety, and sustainability benefits.