3 Labor Questions You Must Answer Before You Begin Your Next Project
How to get the most from the Infrastructure Investment and Jobs Act
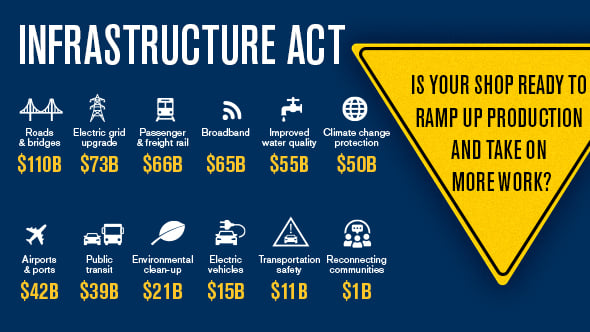
In November 2021, President Joe Biden signed the Infrastructure Investment and Jobs Act (IIJA) into law. The $1.2 trillion act earmarks $715B in infrastructure spending for transportation and roads, with an additional $550B negotiated funding for broadband access, clean water, and electric grid renewal. The most significant government investment of its kind, the IIJA provides a tremendous opportunity to grow the economy, energize manufacturing, and create jobs.
However, with progress comes growing pains — especially in a volatile business landscape. At the end of 2022, manufacturers and economists faced four weighty issues that are still top-of-mind in 2023 — inflation, recession, supply chain, and labor.
The act creates increased downstream manufacturing demand for construction services, tools, and equipment, translating to a glut of orders and a backlog up and down the supply chain. Companies struggle to hire and retain talent, and the shortage of skilled and unskilled workers is heading for a crisis level in 2023.
“By 2030, every single Boomer will have reached retirement age, and that is 74 million people …. These people will be very hard to replace, and it will be expensive.”
Dr. Chris Kuehl, managing director of Armada Corporate Intelligence
Serving 70% of the global plasma market, Hypertherm Associates™ helps manufacturers get the most out of their production and workforce. Hundreds of thousands of businesses rely on our advanced technologies and solutions — proudly made in America — to increase productivity and profitability. Worldwide, a wide variety of industries turn to Hypertherm Associates’ industrial cutting solutions to build ships, airplanes, and railcars, construct steel buildings and bridges, fabricate heavy equipment and wind turbines, and more.
When helping manufacturers leverage talent resources, Hypertherm Associates experts ask three key questions:
-
Do you have a system in place to eliminate and/or reduce secondary operations upstream and downstream of cutting operations?
-
Are your workers equipped with intuitive, easy-to-use tools, software, and equipment to:
-
increase material savings
-
boost productivity
-
lower operating costs and
-
improve part quality?
-
-
Does your business provide continuous training programs that maximize the skills of current workers?
Helping manufacturers optimize their workforce
For over fifty years, Hypertherm Associates has provided our global manufacturing customers with integrated industrial cutting solutions and best practices to succeed in a competitive market. To help manufacturers address the increasing challenge of a labor shortage of skilled and unskilled workers, we suggest a three-prong approach:
- Perform a consultation to evaluate production processes and flows to streamline your production with the right processes and tool usage to impact efficiency, lower costs, and meet timelines.
- Ensure that you utilize the latest technologies to optimize existing operations, including table uptime, consumables utilization, and proper system setup and maintenance.
- Work with manufacturing contacts to get the latest digital asset/training materials to build a training program.
Hypertherm Associates is committed to your company’s success. We can help you identify opportunities to increase production throughput and job site efficiency from building a training plan and optimizing existing equipment and processes to demonstrating the latest technology.
Let’s discuss how Hypertherm Associates can help your business reach its goals.
Contact an expert