How to choose the best plasma cutter for your needs
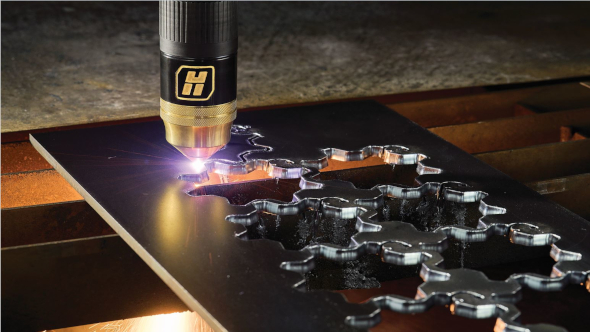
Selecting a new plasma cutter to meet your needs involves carefully considering several factors across many equipment varieties and brands. Weighing the elements below will help you make an informed decision that ensures optimal performance.
Evaluating different models and understanding their unique features, power aspects, and cutting capabilities will allow you to identify a plasma cutter that best aligns with your requirements. When it comes to plasma cutting, the quality of the product is essential―a low-cost machine may seem fine at first, but over the long haul, the better investment is on a high-quality machine.
Additionally, it is critical to determine whether a portable plasma cutter or a high-definition mechanized plasma cutter is suitable for your tasks. Will you use air or a gas? How will you get compressed air? Do you need an air compressor built in, or will you purchase an external one? For hand-held applications, the convenience and maneuverability of a handheld portable unit can significantly impact your workflow, especially in applications that require precision and flexibility.
Versatility is another important consideration. The best plasma-cutting machine for you should be versatile enough to handle a variety of materials, thicknesses, and cutting processes. This ensures you can handle different projects without multiple tools, increasing efficiency and cost-effectiveness.
Collecting information from reliable sources such as product reviews, user testimonials, and expert recommendations is advisable to make the selection process smoother. This wealth of knowledge will help you to make a well-informed decision based on the real-world experiences of others who have used the equipment for similar purposes.
You can confidently choose equipment that aligns with your specific needs and the workpieces you create by considering the best plasma cutting system, portable capacity, and versatility in your decision-making process. This careful consideration ensures that you invest in a high-quality plasma cutter and improve your work's overall efficiency and output
Thickness of the Material Being Cut
The ideal plasma cutting torch should be adaptable enough to handle various materials and thicknesses, providing a clean cut. The adaptability of the plasma cutter ensures you can handle different projects without multiple tools, thus increasing efficiency and cost-effectiveness.
When thinking about cutting thickness, it is recommended that you follow the “80-20” rule. You want to look for a plasma cutter that can handle the metal thickness you cut 80% of the time at the recommended cut capacity. If you occasionally cut thicker materials (20% of the time), ensure that this thickness is at the severance cut capacity of the machine (or lower). This rule will help ensure your plasma cutter can always get the job done, but it is designed to cut the thickness you need the most.
Type of metal
Beyond the thickness of the metal, different types of metal require varying cutting speeds and amperages. For example, cutting aluminum requires a different amperage than cutting steel.
Be sure to select a plasma cutter designed to cut the type of metal you will be working with, considering metals such as stainless steel, mild steel, and aluminum. The type of material plays a significant role in determining the appropriate amperage and cutting speed for efficient and accurate cutting. Choosing a plasma cutter that aligns with the specific characteristics of the metal ensures optimal performance and preserves the integrity of the equipment and material being cut.
Cut quality
When selecting a plasma cutter, achieving the best cut quality is a crucial factor.
If you want a clean and precise cut, you will need a plasma cutter with a higher amperage and use consumables that produce a narrower cut. On the other hand, if a rougher cut is acceptable, a lower amperage plasma cutter may suffice and save some money on initial costs.
Furthermore, the type of operation plays a key role; whether manual cutting, mechanized cutting, using a CNC, or 3D robotic cutting.
Ensuring you use the machine correctly when using any plasma cutter is also essential. Get cutting tips from YouTube or the free Hypertherm Cutting Institute
Available input power
Considering available input power is crucial when selecting a plasma cutter.
Choose a plasma cutter compatible with your work area's power supply and electricity. It is essential that your infrastructure can supply enough amps, volts, and high voltage to provide the output power for the equipment adequately. This ensures the smooth functioning of the plasma cutter and helps avoid problems with its performance and the quality of the cuts.
Consider factors such as cutting capacity, power output, and specific power source requirements of the plasma cutter. This comprehensive approach ensures that the plasma cutter you choose aligns with your cutting needs and integrates seamlessly into your workspace's power infrastructure.
Plasma cutter price
The price of a plasma cutter is another factor to consider. Ensure the plasma cutter you select fits your budget and meets your needs.
However, it is essential to look beyond the initial price of a plasma cutter and consider the overall long-term costs of the system. This involves evaluating consumables (such as electrodes or one-piece cartridges) and considering their life. Monitoring price trends and reviews over time can provide insights into the cost-effectiveness of equipment, considering factors such as increased productivity, improved plasma cutting quality, and reduced material waste. But, like the plasma cutter itself, the consumable price is not the only factor to look at. For example, Hypertherm SYNC® cartridges cost more than a traditional consumable stack-up, but they last up to 5x longer than competitors, making them a better value in the long run.
Other factors you should consider when determining if the price of a plasma cutter is worth it in the long term include:
-
Reliability: Is the machine going to break? How long does the machine last before it needs to be replaced? What is the warranty?
-
Long-term support: Is there support available for this product if it breaks or something goes wrong? Can I get help if I need it?
-
Ease of use: How difficult is learning to use a particular plasma cutter? Can a new operator be up and running quickly?
-
Operating costs: How much does it cost to run this machine? What is gas consumption and cost? What is the electricity cost?
By taking a comprehensive approach to cost considerations, considering consumable life, and keeping an eye on technological advances, you can make an informed decision that aligns with your budget and maximizes the value of your investment in a plasma cutter.
Brand reputation
Brand reputation plays a significant role in the selection process. While there are well-known and reputable brands in the plasma cutting industry, evaluating the brand reputation of any plasma cutter you are considering is essential.
Reputable brands are recognized for producing high-quality plasma cutters specializing in metal cutting for various industrial applications. These companies offer specific solutions that meet the most diverse demands, offering options such as plasma, water jet, robotic, CNC, and manual metal cutting. Additionally, they can provide complementary software solutions such as CAD/CAM and robotic cutting software.
When evaluating plasma cutters, it is essential to delve into specific features like pilot arc versus non-pilot arc technology and considerations like high frequency. Understanding these characteristics becomes crucial when comparing different brands, as some inferior products may claim a certain amperage but fail to deliver the expected performance.
Invest in a brand you can trust: Hypertherm
Considering these crucial factors, you can confidently select a Hypertherm cutting solution that meets your specific metal-cutting needs. The Hypertherm brand’s reputation for excellence in the industry adds another layer of security to your decision-making process.
Distinguished by its commitment to innovation, reliability, and cutting-edge technology, Hypertherm plasma cutters consistently deliver beyond expectations.
Powermax plasma cutters last 10+ years in the harshest environments―this can significantly affect the overall cost of your plasma-cutting operations in the long run.
Whether it is optimal amperage balance, the ability to handle multiple metal thicknesses, compatibility with different operating modes, versatility across materials, fit with your available power infrastructure, a comprehensive assessment of overall system costs, or the company's reputation, Hypertherm Associates stands out for its dedication to precision, performance, and profitability.
To find out more and discover the best plasma cutter for your needs, speak to a Hypertherm expert.
Contact an expert
Want to discuss your needs and get more information on our solutions? Talk to one of our experts.