How does a plasma cutter work
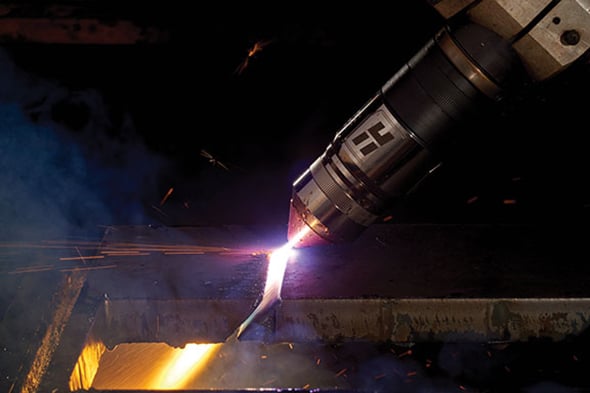
What is plasma cutting?
Plasma cutting is a process that utilizes a high-velocity jet of ionized gas, known as plasma, to cut through conductive materials. Plasma is considered the fourth state of matter - with liquid, solid, and gas being the original three states. Using plasma to cut is widely used in metal fabrication due to its precision, efficiency, and ability to cut various metals. Plasma is created by an electric arc passing through a gas, such as argon, nitrogen, or compressed air. This ionizes the gas, forming a plasma jet capable of cutting through metals like stainless steel and mild steel.
The plasma cutting process involves several key components and steps. First, an electric arc is generated between an electrode and the workpiece. This arc ionizes the gas, creating a plasma jet that reaches extremely high temperatures. The high-velocity plasma jet melts the metal, and the molten material is blown away by the force of the compressed gas, resulting in a clean cut.
Plasma cutting is known for making precise cuts with a smaller heat-affected zone than other methods like oxyfuel, which helps maintain the integrity of the metal being cut. This makes it an ideal choice for applications requiring high-quality and accurate cuts.
The history of plasma arc cutting
The plasma arc cutting process was developed in the 1950s as an alternative to oxyfuel cutting. Initially, it was used primarily for cutting stainless steel and aluminum, as these materials were difficult to cut with traditional methods. Over time, advancements in technology and the development of new plasma cutting systems have expanded the range of materials that can be cut using this process.
In the early days of plasma cutting, the equipment was large and expensive, limiting its use to industrial applications. However, with CNC (computer numerical control) machines and automation, plasma cutting has become more accessible and versatile. CNC plasma cutting machines allow for precise control over the cutting process, enabling the creation of complex shapes and patterns with high accuracy.
Today, plasma cutting is used in various industries, including automotive, aerospace, construction, and metal fabrication. The ability to cut various metals quickly and accurately has made plasma cutting an essential tool in modern manufacturing.
Metals you can cut with plasma
Plasma cutting is a versatile process that can cut various conductive metals. Some of the most common metals that can be cut with plasma include:
-
Stainless steel: Known for its corrosion resistance and strength, stainless steel is commonly used in various industries, including food processing, medical equipment, and construction.
-
Mild steel: Mild steel is also known as carbon steel, and it is widely used in construction, automotive, and manufacturing due to its strength and affordability.
-
Aluminum: Lightweight and corrosion-resistant, aluminum is used in aerospace, automotive, and construction applications.
-
Copper: Known for its excellent electrical conductivity, copper is used in electrical wiring, plumbing, and industrial machinery.
-
Brass: An alloy of copper and zinc, brass is used in decorative applications, plumbing, and musical instruments.
-
Alloys: Various metal alloys, such as titanium and nickel-based alloys, can also be cut using plasma.
The ability to cut a wide range of metals makes plasma cutting a valuable tool in metalworking and fabrication.
Welders and plasma cutting
Welders play a crucial role in metal fabrication, often working alongside CNC plasma machines to create and assemble metal structures. Welding involves joining metal parts by melting and fusing them, typically using a filler material. Various welding techniques are suited for different applications and materials, including MIG (Metal Inert Gas), TIG (Tungsten Inert Gas), and stick welding.
In plasma cutting work, welders often prepare the metal pieces by cutting them to the required shapes and sizes using CNC plasma cutting machines. The precision and efficiency of CNC plasma cutting make it an ideal method for creating the components needed for welding projects. After cutting, welders can join these pieces to form the final product, whether a structural frame, a piece of machinery, or an artistic sculpture.
Types of Plasma Cutters
-
Handheld portable plasma cutters: Handheld portable plasma cutters are designed for ease of use and portability. These cutters are ideal for DIY projects, small-scale metalworking, and on-site repairs. They are lightweight and compact, making them easy to transport and operate. Handheld plasma cutters are suitable for cutting thin to moderately thick metals and are commonly used by hobbyists, artists, and small business owners.
-
CNC plasma cutters: CNC plasma cutters are computer-controlled machines with high precision and automation. These cutters are used in industrial settings for cutting complex shapes and large quantities of metal. CNC plasma cutting machines have a control system that allows the operator to program the cutting path and parameters, ensuring consistent and accurate cuts.
-
CNC machines: CNC machines can cut various materials, including stainless steel, mild steel, aluminum, and alloys. Cutting tables are used in various industries, such as automotive, aerospace, and construction, where precision and efficiency are critical.
-
High-frequency vs low-frequency: Plasma cutters can be classified based on the frequency of the arc starting method. High-frequency plasma cutters use a high-voltage spark to initiate the plasma arc, while low-frequency cutters use a pilot arc. High-frequency cutters are more common in industrial applications because they can cut thicker metals and provide a more stable arc. On the other hand, low-frequency plasma cutters are often used in applications where high-frequency interference could be an issue, such as in electronic manufacturing or near sensitive equipment.
-
Robotic plasma cutting: Robotic plasma cutting involves using robotic arms to perform precise cuts on metal workpieces. This method is highly efficient and is used in automated manufacturing processes. Robotic plasma cutting systems have advanced control systems that allow precise control over the cutting process, ensuring consistent and accurate cuts. Robotic plasma cutting is commonly used in the automotive, aerospace, and shipbuilding industries, where precision and efficiency are essential. Using robotics in plasma cutting also reduces the need for manual labor, improving safety and productivity.
Parts of a plasma cutter
Power supply: The power supply is a critical component of a plasma cutter, providing the necessary electrical energy to create the plasma arc. It converts AC power from the mains supply to the appropriate DC voltage and current required for cutting. The power supply must deliver a stable and consistent output to ensure smooth and efficient cutting.
Power supply console: The power supply console houses the controls and settings for the plasma cutter. It allows the operator to adjust parameters such as amperage, cutting speed, and gas flow. The console also includes safety features and indicators to monitor the status of the cutting process.
Plasma torch: The plasma torch is the tool that directs the plasma jet onto the workpiece. It contains consumables such as electrodes, nozzles, and swirl rings that must be replaced periodically. The torch's design and the consumables' quality play a significant role in determining the cut quality and efficiency of the plasma cutting process.
Gases: Different gases can be used in plasma cutting, including argon, nitrogen, and compressed air. The choice of plasma gas depends on the material being cut and the desired cut quality. For example, argon is often used for cutting stainless steel, while compressed air is commonly used for cutting mild steel. The gas flow rate and pressure must be carefully controlled to ensure optimal cutting performance.
Cutting and gouging with a plasma cutter
Creating the Arc: The plasma arc is created by establishing an electric arc between the electrode and the workpiece. This arc ionizes the gas, forming a plasma jet. The arc is initiated by a high-voltage spark or a pilot arc, depending on the type of plasma cutter used.
Forming the plasma jet: The plasma jet is formed by the high-velocity flow of ionized gas through the torch nozzle. This jet reaches temperatures high enough to melt the metal being cut. The shape and size of the plasma jet are determined by the design of the nozzle and the gas flow rate.
Gas Compression: Compressed gas blows the molten metal away from the cut, ensuring a clean and precise cut. The gas flow rate and pressure must be carefully controlled to achieve the desired cut quality. Compressed gas also helps to cool the torch and prevent overheating.
Molten metal removal: The molten metal is removed from the cut area by the plasma jet's force and the compressed gas flow. This leaves a clean edge on the workpiece, with minimal dross or slag. Properly removing molten metal is essential for achieving high-quality cuts and preventing damage to the workpiece.
Other technologies
Waterjet cutting is another popular method for cutting materials, using a high-pressure jet of water mixed with an abrasive substance to cut through a wide range of materials, including metals, stone, glass, and composites. This highly precise process produces a clean cut with minimal heat-affected zones, making it suitable for applications where material integrity is critical.
Waterjet cutting is particularly advantageous for cutting thick materials and intricate shapes that might be challenging for other cutting methods. It is commonly used in aerospace, automotive, and manufacturing industries, where precision and versatility are essential.
Laser cutting utilizes a focused beam of light to cut through materials with high precision and speed. This method produces clean, accurate cuts with minimal material waste. Laser cutting suits various materials, including metals, plastics, wood, and textiles.
There are two main types of laser cutting: CO2 laser cutting and fiber laser cutting. CO2 lasers are typically used for cutting non-metal materials, while fiber lasers are more efficient for cutting metals. Laser cutting is widely used in electronics, automotive, and signage industries, where precision and efficiency are paramount.
Plasma cutting, in short...
Plasma cutting is a versatile and efficient method for cutting a wide range of metals, offering precision and high-quality results. From its origins in the 1950s to the advanced CNC and robotic systems used today, plasma cutting has evolved significantly. Whether you're working with stainless steel, mild steel, or other conductive materials, plasma cutting provides a reliable solution for industrial and DIY applications. Understanding the components and processes involved, such as the power supply, plasma torch, and gas flow, can help you achieve optimal results in your metal fabrication projects. As technology continues to advance, plasma cutting will remain a crucial tool in the field of metalworking.