The role of a CAD/CAM software solution in smart factory transformation
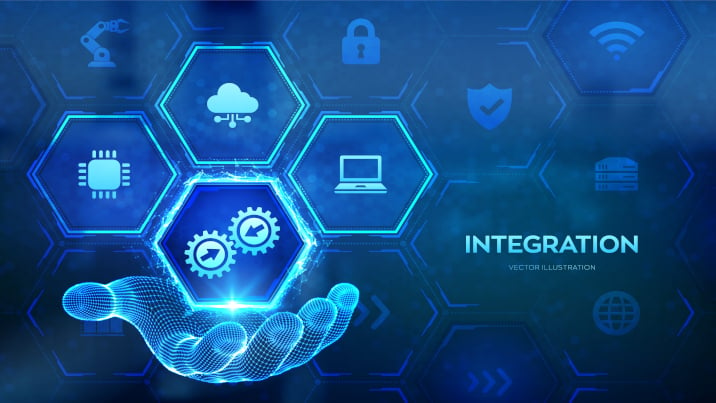
In today’s rapidly advancing industrial landscape, smart factories are at the forefront of manufacturing technology innovation. There are several components such as Internet of Things (IoT), big data and analytics, artificial intelligence (AI), automation, robotics, and digital connectedness that work cohesively to drive a smart factory operation. However, due to limitations of infrastructure, cost, and resources, manufacturing businesses may be at various implementation stages. There is no end point for a smart factory operation. Rather, it is an ongoing process of evolution and improvement.
Integrating a robust CAD/CAM nesting software with Enterprise Resource Planning (ERP systems), Manufacturing Resource Planning (MRP), or Manufacturing Execution Systems (MES) is one step towards facilitating this transformation. This integration not only streamlines the manufacturing operation, but also enhances productivity, reduces costs, and improves overall product quality.
Let’s explore further why investing in a good nesting program can progress your smart factory journey.
What is CAD/CAM part nesting software solution?
A CAD/CAM part nesting software helps manufacturers streamline the process of designing and producing products. A powerful nesting software optimizes the arrangement of different parts to be cut from raw material sheets, maximizing material usage and reducing waste. This process is crucial in industries like metal fabrication, woodworking, and textile manufacturing, where material costs constitute a significant portion of the overall production cost.
The power of integration
- Enhanced data accuracy and consistency
Integrating CAD/CAM part nesting software with ERP software ensures that all data is synchronized across platforms. This eliminates the need for manual data entry, reducing the risk of errors and ensuring that all departments have access to the most up-to-date information. Accurate data is crucial for making informed decisions and maintaining consistency throughout the manufacturing processes.
- Improved production planning and scheduling
With integrated systems, production planning and scheduling become more efficient. The CAD/CAM software can automatically generate nesting plans based on real-time data from the ERP software. This allows for better resource allocation, reduced lead times, and more accurate delivery schedules. Manufacturers can respond more quickly to changes in demand and optimize the production processes.
- Increased material utilization and cost savings
One of the primary benefits of CAD/CAM part nesting software is its ability to maximize material utilization. By integrating this software with ERP/MRP/MES systems, manufacturers can track material usage in real-time and adjust nesting plans accordingly. This leads to significant cost savings by reducing material waste and ensuring that resources are used as efficiently as possible.
- Streamlined workflow and reduced downtime
Integration streamlines the workflow by automating many of the manual processes involved in production. This reduces the likelihood of bottlenecks and minimizes downtime. For example, when a nesting plan is generated, it can be automatically sent to the MES system for execution, ensuring that production continues smoothly without interruptions.
- Enhanced traceability and compliance
In industries where traceability and compliance are critical, integrated systems provide a comprehensive solution. By linking CAD/CAM part nesting software with ERP/MRP/MES systems, manufacturers can maintain detailed records of every step in the production process. This ensures compliance with industry standards and regulations, and provides a clear audit trail for quality control purposes
ProNest CAD/CAM part nesting software
ProNest CAD/CAM part nesting software is designed to meet the needs of the advanced mechanized cutting system customers. ProNest includes powerful features that help manage the entire cutting operation and can be integrated with virtually any third-party ERP/MRP/MES systems. Some examples of successful ProNest integrations include: Abas, Eci JobBOSS, Epicor®, Global Shop Solutions®, Oracle®, Sage™, SAP®, Tekla® PowerFab® and STRUMIS™.
How to integrate with ProNest software
There are several optional modules available in ProNest that are used to enable and support ERP/MRP/MES integration:
Data Sync
Links ProNest to ERP/MRP/MES software, providing the communication framework needed to exchange job information (parts and plates) in real time. Inside the ProNest part list and plate list, users may work with the data supplied from ERP/MRP/MES, and then may return updated part and plate information to ERP/MRP/MES. Data Sync provides plug-and-play integration and setup can be completed in as little as 15 minutes. (Some integrations may take longer, or require custom development work.)
Tekla PowerFab or STRUMIS Connectors
Similar to Data Sync, the Tekla® PowerFab® or STRUMIS™ Connectors link your steel fabrication management software directly to ProNest for seamless data exchange. But even better, these dedicated integrations utilize the software platform’s API for improved performance.
Work Order Processing
Allows for the exchange of all work order related information (in addition to parts and plates). All work order information may then be viewed and managed inside of ProNest, for the most efficient nesting. The ProNest Work Order Processing interface allows for sorting, grouping, combining, and tracking of all work order data, including change orders.
Plate Inventory
Maintains a database in ProNest to store, track, and utilize all of the plate information that has been imported from ERP/MRP/MES system. After job completion, remnants are stored for future use and all plate usage data is reported back to ERP/MRP/MES system.
Practical examples
STRUMIS is a comprehensive software solution designed for the steel fabrication industry. It helps manage and streamline various aspects of steel fabrication projects, including:
-
Project traceability: Ensures complete traceability of all project components
-
Error reduction: Minimizes errors through integrated processes
-
Efficiency improvement: Enhances overall efficiency by connecting and optimizing resources
-
Cost management: Provides tools for effective cost management and budget tracking
The integration between STRUMIS and ProNest offers several practical benefits. Here are some examples of how they work together:
-
Seamless data transfer: STRUMIS can send nesting and ordering data directly to ProNest, eliminating the need for manual file transfers. This ensures that the latest project data is always used for nesting.
-
Material efficiency: Advanced nesting algorithms in ProNest help maximize material usage by efficiently arranging parts on the material sheet. This reduces waste and lowers material costs.
-
Automated nesting: Users can select items to nest within STRUMIS, and ProNest will automatically open, nest the required parts, and return the remaining material to inventory if desired.
-
Integration with CAD software: ProNest can nest parts supplied from major CAD authoring packages, allowing for true shape recognition of components and sheets.
-
Support for multiple cutting technologies: ProNest supports various cutting technologies, including plasma, laser, waterjet, and oxyfuel, making it versatile for different fabrication needs.
These software integrations help streamline the fabrication process, improve efficiency, and reduce operating costs.
Conclusion
Manufacturing companies must prioritize and recognize the importance of digital automation processes, especially in a competitive industry. With rising material costs, limited resources, and rapidly evolving technology, an integrated system becomes essential in running an efficient operation. By continuing to invest and refine, manufacturers can truly leverage smart factory technologies to drive sustainable growth.