What plasma technology delivers better cut quality than CNC high definition plasma cutting machines?
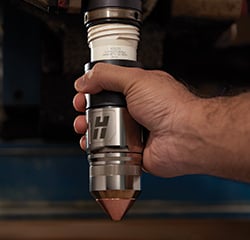
For about thirty years now, since the early 1990’s, high definition plasma was the best plasma you could buy. It provided the very best cut quality, fastest cut speeds, and lowest operating cost among CNC plasma cutters. If you were a high-volume fabricator needing to cut a lot of parts, you needed a CNC high definition plasma cutting machine. Not anymore. A newer plasma technology called X-Definition® plasma is now the best you can get.
Hypertherm’s X-Definition plasma, found in the XPR300™ represents the most significant advance in plasma cutting technology ever. The system offers unmatched cut quality on mild steel, stainless steel and aluminum, increased cut speed, dramatically improved productivity and a 50% operating cost reduction. In addition, new ease-of-use features and engineered system optimization make the XPR300 easier to run with minimal operator intervention, while also ensuring optimal performance and reliability.
These advances are due to an array of new process technologies that build upon the CNC high definition plasma cutting machines found in manufacturing facilities around the world. Here’s a look at some of these key processes.
- HyFlow vortex or vented nozzle technology – A unique two-piece vented nozzle design that aligns and focuses the plasma arc for increased arc stability and energy density resulting in a cleaner, sharper, more consistent edge quality on all steel including stainless steel and aluminum
- Vented Water Injection (VWI) – Patent pending process featuring a vented N2 plasma gas and H2O shield gas for less angularity and squarer cut edges on stainless steel and especially aluminum.
- Vent-to-shield – Technology in which hydrogen from the vented plasma gas is reclaimed and mixed with the shield gas, reducing angularity and delivering more consistent edge color on stainless steel up to 12 mm.
- Plasma dampening – Patent pending technology adds a chamber in the nozzle to absorb the pressure and flow fluctuations that create arc instability during cutting with lower current, highly constricted arcs required for thin stainless applications. This eliminates wavy and irregular cut surfaces.
- Cool nozzle™ – Patent pending feature on the 300-amp oxygen process in which liquid cooling is sent directly to the nozzle bore, increasing cut quality over the life of the consumables by more than 40%.
- Advanced arc stability – Technology that modifies impingement of the shield gas for improved arc stability when coming out of a pierce hole or out of an acute angle for reduced lead-in lengths and improved cut quality.
Another innovative feature is something called Arc response technology™ that senses what is happening with the plasma arc and automatically intervenes to reduce the impact of an electrode blow-out and possible torch failure. This feature can also sense when the arc is about to terminate in an uncontrolled manner. The XPR300 power supply senses when a ramp down error is about to occur and rapidly terminates the arc in a controlled manner for a threefold increase in realized consumable life.
The XPR300 also includes WiFi capability built into the power supply. Owners and operators can use this feature to monitor the system and even perform process set-up tasks from a phone, tablet, or other portable device. The WiFi can also connect to a LAN for users who want to monitor multiple systems at once.
Built in WiFi capability enables connectivity to your smart device for convenient system monitoring, process set up and connectivity to the LAN for multiple system tracking.
In addition to automatic system monitoring, the XPR contains a number of other features to redefine ease-of-use. These features include a patent-pending QuickLock™ electrode in which the electrode is tightened and loosened in a ¼ turn, an EasyConnect™ tool-less connection to the TorchConnect™ console, and a torch design that enables one handed torch change-outs.
QuickLock electrode enables easy, ¼ turn insertion and removal capability.
The XPR300 torch can be easily inserted or removed with one hand and only 1-¼ turns
The XPR300 EasyConnect fitting makes installing or replacing the torch lead simple and easy