Your guide to handheld plasma cutting
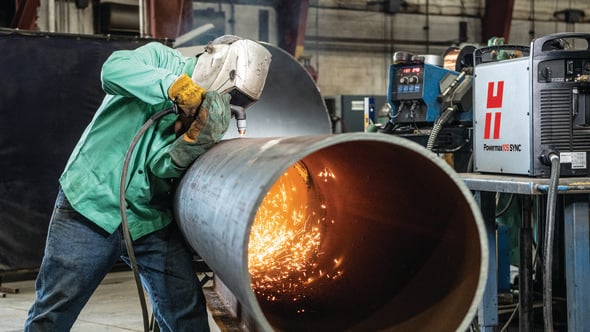
Most industries that fabricate metal products or rely on heavy equipment use handheld plasma cutters for a good reason. Work traditionally done with oxyfuel, punch presses, drills, or cutting shears is often completed faster and more efficiently using a handheld plasma cutter. For example, hand plasma cutters, such as the Hypertherm® Powermax® line, can cut carbon steel up to 2″ thick much faster than oxyfuel.
What is a handheld plasma cutter?
Particularly useful for on-site construction, repair work, and any situation where a stationary cutting machine isn’t practical, a handheld plasma cutter is a metal cutting tool that’s portable, easy to use, and versatile. It uses a high-temperature plasma arc to cut through various types of metal. Some handheld plasma cutter key features:
-
Portable: Quickly carry your handheld plasma cutter to different job sites. Compact and lightweight.
-
Ease to use: Plug in the compressed air, grab the torch, and start cutting. It’s simple.
-
Versatile: Cut sheet metal, tubing, and profiles quickly and efficiently.
Benefits of handheld plasma cutting over other cutting methods
Handheld plasma cutting offers several advantages over carbon arc, oxyfuel, and mechanical cutting methods like grinding, saws, and cutting shears. These advantages include precision and quality, speed and efficiency, versatility, safety and ease of use, and cost-effectiveness.
1. Precision and quality
-
Cleaner cuts: Plasma cutters produce more precise and cleaner cuts with better angularity and a thinner kerf, resulting in minimal dross.
-
Smaller heat-affected zone: This reduces the risk of warping the material, which is particularly beneficial for thin metals.
2. Speed and efficiency
-
No preheating required: Unlike oxyfuel, plasma cutting does not require preheating, saving time and increasing productivity.
3. Versatility
-
Cutting shapes and stacked metals: Plasma cutters can cut complex shapes and tightly stacked metals, offering more flexibility in various applications.
4. Safety and ease of use
-
Safer operation: Plasma cutting does not use flammable gases, reducing the risk of fire and explosion. The arc automatically extinguishes when the torch is removed from the metal.
- User-friendly: Plasma cutters are easier to use and require less operator skill than oxyfuel, which demands precise flame control.
5. Cost-effectiveness
Typical uses of hand plasma cutters:
Handheld plasma cutters are incredibly versatile tools for fabricating parts across various industries. Here are some ways they’re utilized:
Part fabrication
-
Cutting metal: Handheld plasma cutters can slice through different metals, including steel, aluminum, and copper, with high precision and speed. This makes them ideal for creating parts from metal sheets or plates.
-
Gouging and piercing: These tools can also be used to gouge out welding defects or to pierce holes in metal, which is essential for creating complex shapes and designs.
-
Beveling: plasma cutters can bevel edges, which helps prepare metal parts for welding or creating specific angles and shapes.
-
Portability: Their portability allows them to be used on-site, making them convenient for construction and repair work where large stationary cutting machines are impractical.
-
Efficiency: Plasma cutting does not require a preheat cycle and minimizes the heat-affected zone (HAZ), reducing the risk of warping and ensuring cleaner cuts.
-
Cost-effective: Handheld plasma cutters are a cost-effective solution for many fabrication tasks by improving productivity and lowering cutting costs.
Gouging out welding defects and back gouging
Handheld plasma cutters are highly effective for gouging out welding defects and performing back gouging. Here’s how they are used in these processes:
- Preparation: Attaching a gouging tip with a wider orifice to the plasma cutter allows a broader plasma arc to remove more material.
- Operation: Positioning the plasma cutter at an angle to the workpiece enables the plasma arc to melt the defective weld material, and the high-pressure gas blows it away.
- Control: Moving the torch along the defect and carefully controlling the depth and width of the gouge ensures only the defective material is removed.
Back Gouging
-
Setup: Like defect gouging, use a gouging tip and set the plasma cutter to the appropriate settings for the material and thickness.
-
Execution: Starting from the backside of the weld joint, the plasma arc melts the metal, and the gas pressure removes it, creating a clean groove.
-
Purpose: This process ensures complete penetration and fusion of the weld from both sides, eliminating any potential defects and increasing the strength of the joint.
Repairing heavy equipment, such as dump trucks, tractors, rail cars, and cargo trucks
Handheld plasma cutters are invaluable tools for repairing heavy equipment like dump trucks, tractors, rail cars, and cargo trucks. Here’s how they are typically used:
- Cutting and Removing Damaged Parts
-
-
Speed: They work much faster than traditional methods like oxyfuel cutting, which is crucial for minimizing downtime.
- Preparing surfaces for welding
- Beveling edges: Plasma cutters can bevel the edges of metal parts, often preparing them for welding with minimal secondary operations by creating the necessary angles for strong weld joints.
- Cleaning: They can also clean up the edges of metal parts, removing rust, paint, or other contaminants that could affect the quality of the weld.
- Gouging out defects
- Welding defects: Plasma cutters gouge out welding defects, ensuring that the repaired welds are solid and free of imperfections.
- Back gouging: This process involves removing material from the backside of a weld to ensure complete penetration and fusion, which is essential for the structural integrity of heavy equipment.
- Modifying and fitting parts
-
Creating Custom Parts: They can fabricate custom parts on-site, which is particularly useful for older equipment where replacement parts may not be readily available.
- Portability and convenience
-
On-site repairs: Handheld plasma cutters' portability allows for on-site repairs, especially for large or immobile equipment.
-
Versatility: They can cut through various types of metals, including steel, aluminum, and copper, making them versatile tools for different repair needs.
-
Trimming metal components to size or fitting up joints
Handheld plasma cutters are excellent tools for trimming metal components to size and fitting up joints. Here’s how they help:
-
Precision cutting: Plasma cutters provide precise cuts, allowing you to trim metal components to exact dimensions. This precision is crucial for ensuring that parts fit together correctly.
-
Speed and efficiency: They cut through metal quickly, which is essential for maintaining productivity in fabrication and repair tasks.
-
Clean cuts: The high-temperature plasma arc melts the metal, and the forceful gas flow blows away the molten material, leaving a clean edge with minimal dross (residual material).
-
Beveling edges: Plasma cutters can bevel the edges of metal parts, creating the necessary angles for strong weld joints. This is particularly useful for preparing parts for welding.
-
Creating custom shapes: They can cut complex shapes and contours, making it easier to fit parts together, especially in custom fabrication projects.
-
Adjustability: A plasma cutter's settings can be adjusted to accommodate different thicknesses and types of metal, ensuring that the cuts are appropriate for the specific materials being used.
Creating architectural decoration and metal art
Handheld plasma cutters are fantastic tools for creating architectural decorations and metal art due to their precision, versatility, and ease of use. Here’s how they contribute to these creative processes:
- Precision and Detail
-
Intricate designs: Plasma cutters can produce highly detailed and intricate designs essential for decorative elements and metal art. The fine control over the plasma arc allows artists to cut complex patterns and shapes with precision.
-
Clean cuts: The high-temperature plasma beam melts through metal cleanly, reducing the need for extensive post-cutting cleanup.
-
- Versatility
-
Various materials: They can cut through various metals, including steel, aluminum, and copper, making them suitable for different projects.
-
Thickness range: Plasma cutters can handle various metal thicknesses, from thin sheets used in decorative panels to thicker materials for structural elements.
-
- Creative freedom
-
Freehand cutting: Artists can use plasma cutters freehand, much like drawing with a pen, to create unique and personalized designs.
-
Templates and stencils: Artists can use templates or stencils to guide the plasma cutter for more consistent and repeatable designs.
-
- Applications in architectural decoration
-
Decorative panels: Plasma cutters create decorative metal panels for buildings, which can be used as facades, room dividers, or wall art.
-
Custom fixtures: They can be used to fabricate custom light fixtures, railings, gates, and other architectural elements that add a unique touch to buildings.
-
- Applications in metal art
-
Sculptures: Artists use plasma cutters to create metal sculptures, ranging from small decorative pieces to large public art installations.
-
Mixed media art: Plasma cutting allows for the integration of metal with other materials, such as wood or glass, to create mixed media artwork.
-
Removing lugs or cutting off tabs used for fit-up
Handheld plasma cutters are highly effective for removing lugs or cutting off tabs used for fit-up in metal fabrication. Here’s how they help:
- Removing lugs
-
Precision cutting: Plasma cutters provide precise control, allowing you to cut close to the base material without damaging it.
-
Speed: They can quickly slice through lugs, which speeds up the process compared to traditional methods like grinding.
-
Clean cuts: The plasma arc melts the metal, and the high-pressure gas blows away the molten material, leaving a clean edge with minimal dross.
-
- Cutting off tabs
-
Accuracy: Plasma cutters can accurately cut off tabs used for alignment and fit-up, ensuring the remaining material is smooth and ready for the next fabrication step. -
Versatility: They can handle various thicknesses and types of metal, making them suitable for different fabrication needs.
-
Minimal heat-affected zone: The localized heat of the plasma arc minimizes the heat-affected zone (HAZ), reducing the risk of warping or distorting the metal.
-
Industries that use handheld plasma cutters
Due to their speed, precision, and versatility, handheld plasma cutters are widely used across various industries, making them invaluable tools for multiple applications. Here are some key benefits that industries gain from using handheld plasma cutters:
Automotive
- Repair and maintenance: Ideal for cutting and shaping metal parts during vehicle repairs and custom modifications.
- Fabrication: Used in manufacturing car bodies and frames, allowing for precise cuts and efficient production.
Construction
-
On-site cutting: This tool is perfect for cutting steel beams, pipes, and other metal components directly at construction sites, enhancing flexibility and reducing downtime.
-
Demolition: Efficiently cut through metal structures during demolition projects, making the process faster and safer.
Shipbuilding
-
Component manufacturing: Used to cut and shape various metal components
-
Maintenance and repairs: Used to repair damaged sections of ships, ensuring quick and effective fixes.
Manufacturing
-
Metal fabrication: Widely used in producing metal parts and components, offering high precision and clean cuts.
-
Custom manufacturing: Enables the creation of custom metal parts with intricate designs and shapes.
Art and sculpture
-
Metal art: Artists use plasma cutters to create detailed and intricate metal sculptures and artworks.
-
Custom designs: Enables artists to cut metal into unique shapes and patterns, expanding creative possibilities.
DIY and hobbyists
-
Home projects: Popular among DIY enthusiasts for home improvement projects, metalworking, and crafting.
-
Ease of use: User-friendly and portable, making it accessible for hobbyists and small-scale projects.
What to look for when buying a new handheld plasma cutter
When buying a handheld plasma cutter, several essential factors must be considered to ensure you choose one that best suits your needs and ensures efficient, high-quality cutting for your projects.
1. Material thickness
- Cutting capacity: Determine the thickness you will most frequently cut and choose a plasma cutter that handles this thickness efficiently. The “80-20” rule is applicable here: select a cutter that can handle the metal thickness you cut 80% of the time at its recommended capacity.
2. Power output and duty cycle
-
Power output: Ensure the plasma cutter has sufficient power (measured in kilowatts
)to cut through the materials you work with. -
Duty cycle: This indicates how long the machine can operate continuously before needing to cool down. A higher duty cycle is better for longer, uninterrupted cutting sessions.
3. Cutting speed
- Efficiency: To increase productivity, look for a plasma cutter with a high cutting speed. Faster cutting speeds are particularly beneficial for large projects.
4. Portability and size
- Weight and size: If you need to move the cutter frequently, consider its weight and size. A compact and lightweight model is more accessible to transport and handle.
5. Consumables and operating costs
-
Consumable life: Check the cost and lifespan of consumables (like electrodes and nozzles). Longer-lasting consumables can reduce operating costs over time.
-
Maintenance: Consider the ease of maintenance and availability of replacement parts.
6. Ease of use
- User-friendly features: Look for easy-to-read displays, straightforward controls, and ergonomic design. These can make the cutter easier to operate, especially for beginners.
7. Versatility
-
Cutting capabilities: Some plasma cutters offer additional features like gouging, piercing, and beveling, which can be helpful for different applications.
8. Safety features
9. Price and warranty
- Budget: Balance your budget with the features you need. Sometimes, investing more upfront can save money in the long run due to better performance and durability.
A handheld plasma cutter like Hypertherm Powermax opens a world of possibilities for precision cutting
In summary, handheld plasma cutters, like Hypertherm Powermax, are versatile, efficient, and indispensable tools that significantly enhance metalworking capabilities. Whether you’re a professional fabricator or a DIY enthusiast, having one in your toolbox opens a world of possibilities for precision cutting and creative projects.
-
Versatility: Powermax® is the world’s most versatile family of portable plasma cutters, delivering maximum productivity and unmatched reliability. It cuts through various metals, including steel, aluminum, and copper, making it suitable for various projects and repairs.
-
Precision and speed: Powermax handheld plasma cutters provide precise, clean cuts quickly, enhancing productivity and reducing time spent on tasks.
-
Portability: Powermax portability enables on-site work, making them ideal for field repairs and adjustments.
-
Efficiency: Powermax minimizes the heat-affected zone, reducing the risk of warping and ensuring high-quality cuts.
-
Cost-effective: Powermax plasma cutters deliver superior cut quality and minimized secondary operations―at a lower total cost of ownership.