A nova definição do corte por plasma
A nova geração de corte plasma da Hypertherm
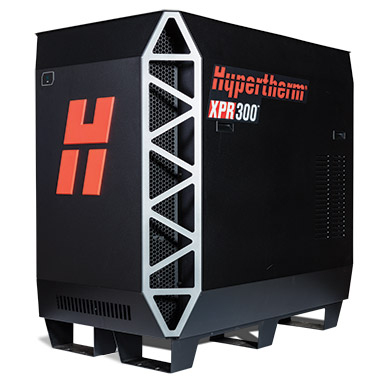
Hoje em dia, a indústria metalmecânica conta com diversas soluções para o corte de metais, como o plasma, laser, jato d´água e oxicombustível, além de uma variedade imensa de modalidades de corte mecânico. Embora todos os processos mencionados já estejam bem estabelecidos e com um bom histórico em nosso mercado, cada um possui seus benefícios e deficiências que devem ser considerados ao decidir qual método de corte utilizar para uma determinada aplicação.
No Brasil e em toda América do Sul, o Plasma vem rapidamente se tornando uma das escolhas mais populares entre os fabricantes modernos, especialmente quando falamos da fabricação de produtos metálicos que podem não obter os melhores resultados quando se utilizam outros métodos de corte tradicionais. Não só o plasma proporciona um bom equilíbrio em termos de custos de investimento e operacional, como também é a combinação ideal de qualidade, extrema versatilidade e altas velocidades de corte.
Então, o que é plasma? De uma maneira simplificada, o corte por plasma é uma tecnologia que usa um gás ionizado de alta temperatura para produzir um arco elétrico muito quente e com alta densidade de energia, que pode cortar qualquer material eletricamente condutivo. A corrente do plasma é tipicamente criada forçando os gases como nitrogênio e oxigênio, ou mesmo ar comprimido, através de um bico com um orifício estreito, enquanto uma corrente elétrica produzida por uma fonte de alimentação externa adiciona energia suficiente para ionizar o fluxo de gás, transformando-o em um arco de plasma com temperaturas que podem chegar facilmente aos 25.000 ˚C. Daí, o arco de plasma derrete e corte o metal. Esse é o principal processo para sistemas de corte manual e mecanizado.
A vantagem do plasma
Sistema de corte plasma a ar comprimido Hypertherm Powermax85
No que diz respeito ao corte de metais, diversos fatores podem afetar a eficiência, sendo um fator crítico a velocidade de corte. Nos processos de fabricação, tal fator é extremamente importante, considerando que a velocidade de corte é diretamente proporcional ao ritmo produtivo. Ou seja, quanto maior a velocidade de corte, maior a produtividade. Comparado a outros processos de corte, o plasma corta com maior velocidade, sendo o mais rápido para chapas de 6 a 76 mm devido à capacidade de derreter o metal quase que instantaneamente após o contato. As velocidades de corte também aumentam à medida que a espessura do material diminui, e esse aumento de velocidade quer dizer que o operador pode cortar mais peças em menos tempo.
A qualidade de corte é outro fator crítico para as empresas quando precisam selecionar um equipamento para cortar metais. O corte por plasma, particularmente o Plasma de Alta Performance, é capaz de produzir bordas relativamente lisas e com pouco enrijecimento, o que permite uma excelente soldabilidade após o corte. Além disso, produz uma escória mímina, reduzindo a necessidade de processos secundários de limpeza e preparação, como o esmerilhamento. Em geral, o plasma produz cortes de alta qualidade, mais limpos e mais precisos se comparados ao oxicombustível.
Nos últimos anos, a facilidade de operação dos processos técnicos também vem ganhando importância como um fator decisivo no que tange ao investimento tecnológico, principalmente por minimizar a necessidade de treinamentos, melhorar a segurança e, sobretudo, aumentar a lucratividade. Em conjunto com a última palavra em CNC e software, o plasma torna-se um processo extremamente fácil de aprender e usar com os parâmetros pré-definidos e incorporados pelo Software de Aproveitamento (CAM), minimizando a necessidade da experiência prévia do operador. Mais: os sistemas manuais de corte por plasma são altamente portáteis graças a seu tamanho e peso relativamente compactos.
Outra grande vantagem do corte por plasma é a versatilidade. Na medida em que usa um arco elétrico de gás ionizado de alta temperatura para cortar todo material eletricamente condutivo, pode ser usado para o corte de materiais ferrosos e não-ferrosos, bem como para metais que estejam em qualquer condição, mesmo pintados ou enferrujados. Isso confere um maior grau de flexibilidade ao trabalho de corte, pois o plasma permite cortar uma ampla gama de tipos e espessuras de materiais. A versatilidade dos sistemas de corte por plasma pode ainda ser aumentada quando combinada com tochas e consumíveis específicos. Diversas opções de tocha estão disponíveis, variando em comprimento e ângulo para atender diferentes necessidades de aplicações industriais. O plasma pode ser utilizado por arraste (bico de contato tocando a chapa para guiar o operador), distanciado (sem tocar a peça para acesso a locais mais difíceis) e, até para obter cortes mais delicados e com alta qualidade em materiais mais finos, simplesmente substituindo alguns consumíveis da tocha. Essa é uma característica muito atraente, pois um único sistema de corte por plasma pode ser empregado em uma variedade de aplicações com mudanças simples para adequar aos processos industriais, sem ter que alternar entre várias ferramentas para completar o trabalho.
Além do corte, os sistemas de plasma podem também realizar outras tarefas alternativas ao mesmo tempo. Um exemplo muito comum é a goivagem e aplicações típicas, que incluem a remoção de uma solda pré-existente durante um serviço de reparo, desmontagem com remoção de soldas ou, ainda, limpeza de raiz ou passes de solda para processos de múltiplas camadas de solda. O corte por plasma é, portanto, capaz de satisfazer as necessidades de corte e goivagem em uma ampla gama de aplicações industriais, seja para metais mais finos ou mais espessos, ferrosos ou não-ferrosos.
O plasma pode ser utilizado também para marcar materiais, seja com letras e números para identificação de peças cortadas ou simplesmente para marcar linhas de solda ou dobra na continuação do processo de fabricação. Os sistemas automáticos modernos permitem que você corte e marque utilizando os mesmos consumíveis, o que aumenta consideravelmente a produtividade.
Conforme ilustramos acima, o plasma oferece uma combinação ideal entre qualidade e produtividade, conveniência e versatilidade, seja para aços-carbonos e inoxidáveis ou alumínio em uma ampla gama de espessuras. Os sistemas de plasma são muito eficientes, mas os fabricantes têm buscado nos últimos anos ainda melhores resultados. Juntamente com o advento da tecnologia, temos agora uma crescente demanda por sistemas de corte mais desenvolvidos e sofisticados, que atendem às necessidades da fabricação moderna.
Com isso em mente, a Hypertherm lançou recentemente o seu mais avançado sistema de corte mecanizado, a XPR300TM.
Conheça o novo plasma
Equipamento único em seu segmento, a XPR300 representa o avanço mais significativo na tecnologia de corte por plasma mecanizado. Comparada ao sistema antecessor e líder do setor – a linha HPRXD® – a novidade apresenta um salto no desempenho de corte e na relação custo-benefício. Oferece uma qualidade de corte inigualável em vários metais (aço-carbono, inoxidável e alumínio), aumentando a velocidade de corte, melhorando a produtividade e reduzindo em até 50% os custos operacionais. Além disso, os novos recursos de facilidade de uso e otimização do sistema de engenharia tornam a XPR300 mais fácil de utilizar com a mínima intervenção do operador, ao mesmo tempo em que garante um desempenho otimizado e maior confiabilidade.
Esses avanços são atribuídos a uma série de novas tecnologias de processo que a Hypertherm nomeou como corte “X-Definition” (veja a tabela 1)
Maior produtividade e rentabilidade
Para a maioria dos fabricantes na indústria, existem dois benefícios mais procurados em um equipamento de corte por plasma: melhor desempenho e melhor custo-benefício. São essas as principais áreas que a Hypertherm procurou atingir com a introdução da XPR300.
Quando se trata de corte industrial, produtividade e rentabilidade – ou a falta de ambos –, pode ser resumida em alguns pontos: Velocidade de Corte, Qualidade de Corte, Vida Útil dos Consumíveis e Tempo de Atividade do Sistema. A XPR300 aborda esses quatro aspectos com um sistema que permite cortar mais rápido, melhor e de forma mais eficiente, com a utilização de uma tecnologia “inteligente” e de alguns passos que visam a economizar tempo.
Velocidade de corte – com 300 ampéres e 63 Kw de potência, em comparação com os 260 ampéres e 45.4 Kw oferecidos por sua antecessora (HPR260XD), a XPR300 pode cortar mais rápido. O aumento específico na velocidade depende da espessura do material, porém, os usuários podem esperar um aumento entre 10 e 20% em materiais entre 15 e 40 mm de espessura, 39% em materiais de 50 mm e quase 50% em 60 mm de espessura. Essas melhorias na velocidade de corte se traduzem em maior produtividade e rentabilidade, uma vez que é possível completar mais trabalhos no mesmo espaço de tempo.
Espessura | Vel. de corte (mm/min) | |||
XPR300 | HPR260XD |
XPR300 |
||
15 mm | 3440 | 3130 | 10% | |
20 mm | 2550 | 2170 | 18% | |
25 mm | 1950 | 1685 | 16% | |
30 mm | 1530 | 1290 | 19% | |
40 mm | 940 | 790 | 19% | |
50 mm | 560 | 405 | 38% | |
60 mm | 385 | 258 | 49% |
A XPR300 corta de 10 a 20% mais rápido do que sua antecessora em metais de até 40 mm de espessura e, aproximadamente, 50% mais rápido em materiais com espessuras acima de 50 mm.
Além das maiores velocidades de corte, a XPR300 é mais eficiente do que a HPR260XD® . Por exemplo, a XPR300 requer apenas 170 ampéres para atingir a mesma velocidade de corte de uma HPR260XD a 200 ampéres. Isso não só permite um corte mais rápido, mas a XPR300 também consome menos energia no processo de corte.
A velocidade de corte de uma XPR300 a 170 A é comparável à de uma HPR usando 200 A de corrente de corte.
Qualidade de corte – O fator de diferenciação está no exclusivo corte “X-Definition” da Hypertherm, que melhora a capacidade do plasma em lidar com aplicações de alta precisão. Essa classe de corte melhora a qualidade do serviço quando medida utilizando a norma ISO9013, padrão internacional que define a qualidade de corte para os processos de corte térmico. A norma usa uma escala de 1 a 5, sendo 1 considerado o melhor. A nova XPR300 entrega qualidade de corte na escala 3 (ISO Range 3) durante toda a vida do consumível, enquanto o corte em aço-carbono fino (abaixo de 6 mm) fica consistentemente dentro da escala 2 (ISO Range 2). Em comparação, os sistemas HPRXD da Hypertherm tendem a entregar os cortes na escala 4 (ISO Range 4).
O processo de corte de aço-carbono com 300 A da XPR300 se mantém na ISO Range 3 por, praticamente, toda a vida do consumível – 1368 cortes de 20 s em chapa de 20 mm, comparado à ISO Range 4 de sua antecessora (HPRXD).
O processo de corte de aço carbono com 80 A da XPR300 se mantém na ISO Range 2 por, aproximadamente, 1.300 cortes de 20 s em chapa de 6 mm, antes de se mover para a ISO Range 3.
ISO Range 2 em aço-carbono
Amostra apresentando a qualidade de corte e a borda afiada no corte de aço inoxidável, usando a capacidade da XPR300 de misturar gases de plasma (H2-Ar-N2) com o console OptiMix.
Em conjunto com o aumento na qualidade de corte, outro aspecto notável é a consistência do corte. A XPR pode produzir peças com qualidade uniforme de corte, resultado obtido graças a diversas novas tecnologias patenteadas pela Hypertherm. Dentre elas, citamos a injeção ventilada de água (VWI), que combina o nitrogênio como gás plasma com a proteção de um spray de água para melhor alinhar e focar o arco plasma. Uma segunda tecnologia, chamada “Vent-to-Shield”, recupera o hidrogênio do gás plasma e o mistura ao gás de proteção. Somadas, essas duas tecnologias são capazes de produzir bordas mais afiadas, com menor angularidade e uma superfície de corte com acabamento otimizado quando comparado ao dos sistemas HPRXD. A XPR também utiliza um processo chamado “Advanced Arc Stability”, projetado para estabilizar o arco plasma desde o momento da perfuração da chapa, além de novos protocolos de segmentação para furos que ultrapassam o processo de True Hole®, da Hypertherm, e já existente nos sistemas HPRXD. Isso permite que a XPR300 produza furos prontos para passar parafusos até uma proporção de diâmetro/espessura de 1:1.
À medida que a qualidade de corte é aprimorada, os cortes então terceirizados para empresas que cortam com laser ou outros processos especializados podem ser realizados dentro de sua própria fábrica, reduzindo tempo de fabricação e custos adicionais com corte e logística. Com uma tocha projetada para atingir a melhor performance, também foi melhorado o desempenho em cortes especiais, com aplicações de corte 3D, robótico e chanfrado. Com o maior ângulo de ataque, as operações que exigem maior movimentação e angularidade da tocha ficaram ainda mais fáceis, reduzindo custos operacionais.
Durabilidade dos consumíveis –
A XPR300 vem equipada com um recurso de patente pendente chamado Cool Nozzle, que leva refrigeração líquida diretamente ao corpo do bocal de corte, aumentando a vida útil dos consumiveis. Durante os testes de laboratório, chegamos ao número de 1.400 cortes de 20 s em chapa de aço-carbono de 19 mm, o que representa 50% de melhoria. O aumento da vida útil dos consumíveis é ainda melhorado através da nova Tecnologia de Resposta do Arco, que consiste em dois recursos específicos: Proteção Automática da Tocha e Proteção Automática contra Erros de Rampa.
No corte, os erros de rampa são considerados os vilões quando se trata da vida útil dos consumíveis. Esses erros ocorrem quando o arco é encerrado de maneira descontrolada ao sair da chapa ou, no corte de furos, apagando o arco pela falta de material. Quando isso acontece, o inserto de háfnio localizado na ponta dos eletrodos não consegue se ressolidificar quando o arco se apaga. Como resultado, cada vez que ocorre um erro de rampa, um pouco desse háfnio é ejetado do eletrodo, acelerando o desgaste do consumível.
A fonte de energia XPR300 controla esse problema ao utilizar a Proteção Automática contra Erros de Rampa, que detecta automaticamente quando um erro de rampa irá ocorrer e encerra o arco de forma controlada, permitindo que o háfnio se ressolidifique, prolongando a vida útil do eletrodo e do bico de corte. Embora a maioria dos sistemas de plasma apresente redução de cerca de 50% na vida dos consumíveis por erros de rampa, com a XPR300 essa taxa é diminuída para menos de 10%. Isso equivale a um ganho real na vida dos consumíveis de quase três vezes, o que é traduzido em redução de custos para o cliente final.
Tempo de atividade do sistema – as melhorias na vida útil dos consumíveis mencionadas anteriormente também contribuem para o tempo de atividade do sistema. A tecnologia patenteada “Power Pierce” leva refrigeração líquida até o escudo protetor, o que ajuda a repelir o metal derretido que retorna no momento da perfuração de chapas mais espessas, evitando, assim, que o escudo seja prematuramente danificado. Com menos tempo utilizado na troca de consumíveis, os operadores ganham mais tempo para cortar e realizar outras atividades.
A XPR300 é um dos sistemas mecanizados de corte por plasma mais inteligentes já lançados até o momento. Os sensores instalados em diversos pontos do equipamento monitoram continuamente a corrente, pressão, fluxo de gases e temperatura. A seguir, as comparam com as especificações durante a operação, para garantir o melhor tempo de atividade do sistema.
Com a combinação de velocidades de corte mais rápidas, qualidade de corte melhorada, maior vida útil dos consumíveis e maior tempo de atividade do sistema, a XPR representa maior produtividade e menor custo operacional.
Comparativo de custos por metro de corte entre a XPR300 e sua antecessora HPRXD.
Recursos focados no usuário
Apesar do grande volume de tecnologias encontradas na XPR300, o sistema é surpreendentemente descomplicado e fácil de usar. Os sensores da fonte de energia fornecem códigos de diagnóstico refinados e informações de monitoramento do sistema bastante aprimoradas. Esses recursos permitem reduzir o tempo para solução de problemas e fornecem dados que otimizam a condição geral do sistema.
Além do monitoramento automático, a XPR possui vários outros recursos que redefinem a facilidade de uso. Por um lado, o sistema é projetado com menos consoles e conexões, para que os operadores gastem menos tempo de configuração e mais tempo cortando. Outros recursos importantes são o dispositivo de conexão da tocha “Easy Connect”, que permite ao operador conectar o cabo da tocha no console sem o uso de ferramentas, e o eletrodo “Quick Lock”, com patente pendente e que possibilita a substituição do eletrodo sem ferramentas e com apenas ¼ de volta, reduzindo ainda mais o tempo de configuração do sistema.
A nova XPR300 inclui também a capacidade de conexão Wi-Fi incorporada na fonte de energia. Os proprietários, gerentes e operadores podem usar esse recurso para monitorar o sistema ou executar tarefas de configuração de processo utilizando um smartphone, tablet ou outros dispositivos portáteis. O Wi-Fi pode também ser conectado a uma rede local para rastreamento e controle de múltiplos sistemas. Com certeza, a XPR300 adequa-se à Indústria 4.0.
Conclusão
A XPR300, da Hypertherm, representa a próxima geração de sistemas de cortes mecanizados líderes da indústria. Ao combinar inovação tecnológica e design inteligente, oferece o mais alto padrão de desempenho em aço-carbono, inoxidável e alumínio, expandindo as possibilidades e capacidades de corte de uma maneira anteriormente impossível.
Última Tecnologia de Processo | Detalhes |
---|---|
Vortex de Alto Fluxo ou Tecnologia de Bocal Ventilado | Bico ventilado de duas peças com design exclusivo, que alinha e concentra o arco de plasma para aumentar a estabilidade do arco e a densidade de energia, resultando em uma qualidade de borda mais afiada, nítida e consistente em todos os materiais, incluindo aço inoxidável e alumínio. |
Injeção Ventilada de Água (VWI) | Processo com patente pendente que contempla N2 como gás de plasma e H2O como proteção para menor angularidade e bordas mais afiadas em cortes de aços inoxidáveis e, principalmente, alumínio. |
Vent-to-Shield | Processo no qual o hidrogênio do gás de plasma é recuperado e misturado novamente ao gás de proteção, reduzindo a angularidade e proporcionando cortes e bordas mais consistentes em aços inoxidáveis até 12 mm. |
Plasma Dampening | Recurso que adiciona uma câmara no bocal para absorver as flutuações de pressão e fluxo dos gases que criam instabilidade de arco ao cortar com baixas correntes e arcos muito constringidos, requeridos para corte de inoxidáveis de baixa espessura. Isso elimina a irregularidade e ondulação da superfície de corte. |
Cool Nozzle | Recurso de patente pendente no processo de corte de 300 A com O2 e ar comprimido, no qual o resfriamento líquido é levado até o orifício do bico de corte, aumentando a qualidade de corte duranta a vida dos consumíveis em mais de 40%. |
Estabilidade de Arco Avançada | Tecnologia que reduz o impacto do gás de proteção para melhorar a estabilidade de arco na perfuração ou ângulos agudos. Pode resultar na redução das entradas de corte. |