Cięcie plazmowe w porównaniu z cięciem laserem światłowodowym
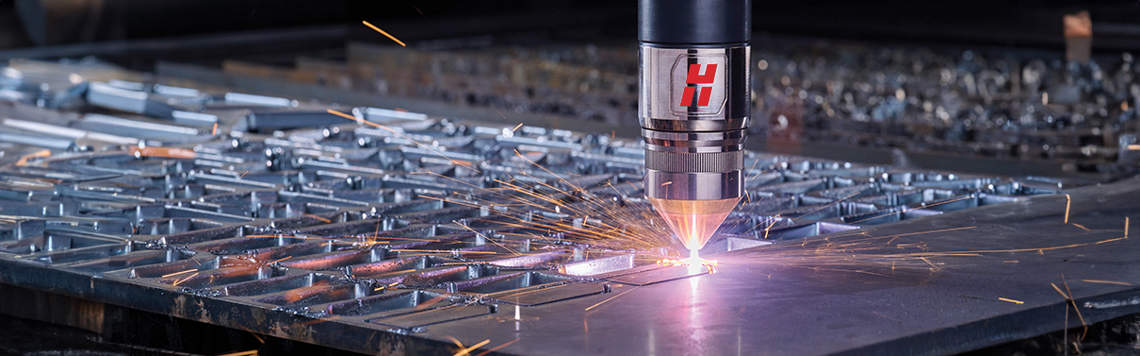
Porównując technologię plazmową z laserową, należy zauważyć, że plazma lepiej nadaje się do cięcia metalu o grubości od 6 mm do 50 mm ze względu na wyższą szybkość cięcia, niższy koszt zakupu i eksploatacji, a także większą elastyczność przy pracy z niedoskonałym lub odbijającym światło metalem. Ponadto, z wykorzystaniem plazmy można ciąć pod kątem bez konieczności wykonywania dodatkowych operacji.
Korzyści z wyboru cięcia plazmowego zamiast cięcia laserowego
Plazma i laser światłowodowy to produktywne technologie cięcia przemysłowego, które mają zalety i wady. Wybór technologii zależy od konkretnego zadania i wyników cięcia, które najlepiej odpowiadają indywidualnym wymogom. Ponieważ laser światłowodowy to nowsza technologia, czasami uważa się, że jest lepszy i bardziej nowoczesny. Mimo że laser światłowodowy zaczęto stosować dopiero niedawno do cięcia metali przekraczających grubość blachy, w ciągu ostatnich kilkudziesięciu lat systemy plazmowe zostały tak udoskonalone, że zapewniają wysokiej jakości wyniki cięcia przy mniejszych początkowych kosztach inwestycji i eksploatacji. Co najważniejsze, przed wyborem technologii odpowiedniej do realizowanych operacji należy wziąć pod uwagę następujące kwestie:
-
Grubość materiału
-
Jakość cięcia
-
Szybkości cięcia
-
Koszty eksploatacji
-
Inwestycja początkowa
-
Stan elementu obrabianego
-
Konserwacja
Plazma zapewnia doskonałą jakość cięcia
Różnica w jakości cięcia między technologią plazmową X-Definition® a technologią cięcia laserem jest niewielka. Systemy plazmowe Hypertherm XPR170® i XPR300® X-Definition oferują gładsze wykończenie powierzchni niż w systemach lasera światłowodowego przy cięciu materiałów o grubości przekraczającej 16 mm oraz zapewniają powtarzalną i wysoką jakości krawędzi w całym okresie eksploatacji zestawu materiałów eksploatacyjnych. Procesy plazmy X-Definition mogą zapewnić jakość cięcia porównywalną z systemami laserowymi w przypadku stali miękkiej, stali nierdzewnej i aluminium.
Aby łatwiej porównać jakość cięcia oferowaną przez te dwie technologie, warto przywołać normę ISO 9013, określającą międzynarodowe standardy klasyfikacji jakości części wycinanych w dowolnym procesie termicznym. Norma ISO 9013 definiuje kątowość metody, czyli odchylenie od linii prostopadłej, w zakresie od 1 (najmniejsze odchylenie) do 5 (największe odchylenie).W połączeniu z systemem cięcia o doskonałych możliwościach przesuwu system plazmy X-Definition zapewnia jakość cięcia cienkiej stali miękkiej (o grubości mniejszej niż 10 mm) w zakresie 2, a w przypadku grubszych metali — w zakresie 3 wspomnianej klasyfikacji.
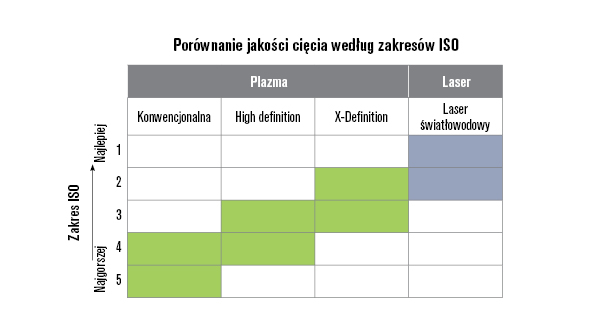
Plazma wycina otwory pod śruby i ukosy gotowe do spawania
W połączeniu z oprogramowaniem typu CAD/CAM, na przykład ProNest®, możliwe jest radykalne obniżenie kosztów robocizny i czynników ograniczających wydajność. Aplikacje korzystające z technologii SureCut™ pozwalają uzyskać wysokiej jakości cięcia — przy jednoczesnym ograniczeniu konieczności konfiguracji i testowania — dzięki wbudowaniu w nie specjalistycznej wiedzy na temat plazmy i parametrów procesu. Ogranicza to konieczność skomplikowanego programowania, stosowania metody prób i błędów oraz interwencji operatora.
Oto, jak procesy SureCut pomagają maksymalizować wydajność systemów plazmowych Hypertherm:
-
True Hole® zapewnia bardziej precyzyjne i lepiej zdefiniowane otwory o znacznie mniejszej stożkowatości i minimalnych śladach ścieżek wejścia oraz wyjścia cięcia. Technologia True Hole umożliwia tworzenie otworów gotowych na śruby bezpośrednio na stole do cięcia plazmowego, co eliminuje konieczność wiercenia otworów w oddzielnym kroku.
-
True Bevel™ automatycznie stosuje prawidłowe parametry cięcia, dzięki czemu operatorzy są w stanie ukosować krawędzie przy pierwszym podejściu, bez konieczności wykonywania drugiego kroku, który jest zwykle wymagany w przypadku konkurencyjnych technologii. Spawacze nie muszą już ręcznie przycinać ani szlifować krawędzi ukośnych pod określonym kątem.
-
Rapid Part™ optymalizuje etapy procesu, które nie wnoszą wartości dodanej. Obejmuje to czas wymagany na wycofanie i przemieszczenie palnika plazmowego oraz takie etapy, jak przepływ wstępny gazu. Skracając lub eliminując czas przestoju między cięciami, operatorzy mogą ciąć więcej części — czasem dwa razy więcej — w tym samym czasie.
-
Plate Saver™ to połączenie stabilności łuku systemu XPR® i możliwości specjalistycznego oprogramowania, które umożliwia znaczną poprawę wykorzystania materiału.
Tolerancje systemów klasy laserowej wiążą się z kompromisem po stronie kosztów
Różnica w zakresie tolerancji lasera i plazmy jest mniejsza niż mogłoby się wydawać — około 0,25 mm, czyli mniej więcej tyle, ile wynosi grubość wizytówki. Jak wyjaśniono w tym artykule na temat zakresów tolerancji systemów laserowych, ściślejsze tolerancje często wiążą się z kompromisem po stronie kosztów. Mimo że szerokość szczeliny podczas cięcia laserem światłowodowym może zapewniać korzyści, może także zakłócać przebieg produkcji podczas cięcia grubszych metali. Cienka szczelina może powodować łatwe stapianie się części, co uniemożliwia ich uwolnienie ze szkieletu i spowalnia w ten sposób przepływ produkcji oraz skutkuje koniecznością interwencji operatora.
System plazmowy jest szybki
Szczególnie przy cięciu metali o grubości powyżej 16 mm system plazmowy tnie szybciej niż system lasera światłowodowego. Przekłada się to na lepszą produktywność, mniej wąskich gardeł, lepszą terminowość dostaw oraz większy przepływ środków pieniężnych i potencjał rozwoju firmy.
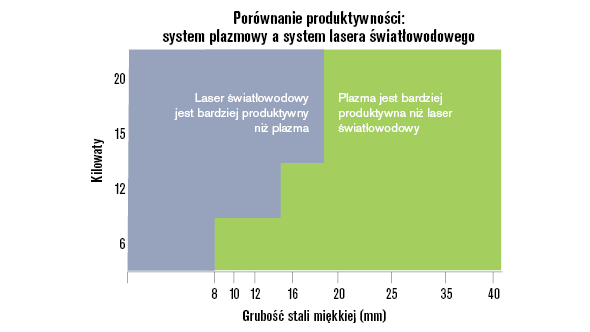
System plazmowy to niższe koszty
Na koszty operacji cięcia składa się wiele czynników, w tym gaz, energia elektryczna, materiały eksploatacyjne, konserwacja, robocizna, odpady i początkowe inwestycje w maszyny. Idealnie byłoby, gdyby materiały eksploatacyjne zapewniały spójne efekty obróbki i jednakowo długi okres eksploatacji nawet przy cięciu różnych metali różnych typów i grubości, gdyż przekładałoby się to na niższe koszty gotowego produktu i mniejsze ilości odpadów.
Biorąc pod uwagę bezpośrednie koszty operacji cięcia, system plazmowy często zapewnia niższe koszty na metr w przypadku grubszych metali ze względu na udoskonalone procesy i zmniejszone zużycie gazu. Nawet tam, gdzie bezpośrednie koszty operacyjne systemu lasera światłowodowego są niższe, jak w przypadku cienkich metali, należy obliczyć wymagania dotyczące zużycia energii elektrycznej i gazu przez taki system. Klienci często są zaskoczeni wysokim zużyciem tych surowców i koniecznością instalowania systemów masowego magazynowania gazu lub zakupu systemów wytwarzania azotu.
Początkowa inwestycja w maszynę do cięcia plazmowego jest zwykle 2–5 razy mniejsza niż w przypadku systemu cięcia laserem światłowodowym. Choć może się to wydawać kosztem jednorazowym, opłaty amortyzacyjne w rachunku zysków i strat firmy znacznie zwiększą całkowity koszt posiadania (TCO) systemu lasera światłowodowego w nadchodzących latach. Jeśli laser światłowodowy nie jest wykorzystywany w dużym stopniu, zwrot z inwestycji jest mało prawdopodobny.
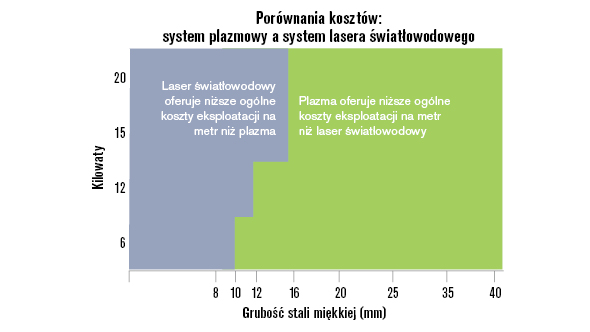
System plazmowy jest wszechstronny
System plazmowy jest bardziej tolerancyjny w przypadku kondycji ciętego metalu. Niezależnie od tego, czy metal jest utleniony, lakierowany, czy ma różną grubość w zależności od rodzaju cięcia, plazma tnie niezawodnie. Wcześniej cięcie laserem wymagało, aby arkusz był konkretnego gatunku, był przechowywany w pomieszczeniu i/lub czyszczony przed operacją cięcia. Mimo że zdolność lasera do radzenia sobie z tymi niekorzystnymi warunkami materiałowymi ulega poprawie, cięcie laserem zwykle obejmuje dodatkowe etapy obróbki, takie jak przejście odparowujące szeroką wiązką, co wydłuża czas cykli procesu.
System plazmowy jest wytrzymały i niezawodny
Klienci wielokrotnie zgłaszają, że najważniejszymi cechami systemu plazmowego jest jego prostota, wytrzymałość i niezawodność. Jego Konserwacja jest prosta i zwykle wewnętrzne działy serwisu mogą z łatwością zarządzać wszystkimi procedurami — oprócz tych najbardziej złożonych. W przeszłości lasery CO2 miały opinię wymagających. Nie były niezawodne, a koszty ich utrzymania były wysokie. Laser światłowodowy, wyposażony w mniej komponentów źródła zasilania, jest znacznie bardziej niezawodny niż starsze technologie laserowe. Mimo to w przypadku tych systemów konserwacja ma kluczowe znaczenie. Wymagają one regularnych kontroli, regulacji i konserwacji przez wyspecjalizowanych techników. Ponieważ koszt i delikatność niektórych komponentów — na przykład laserowej głowicy tnącej — może opiewać na dziesiątki tysięcy dolarów, jednostki te są często wymieniane i zwracane do naprawy w pomieszczeniu czystym.
Ostatnio w wielu regionach odnotowuje się napływ tanich systemów laserowych oferujących to, co najlepsze z obu technologii: dobrą jakość cięcia i niski koszt inwestycji początkowej. Jeśli coś brzmi zbyt dobrze, aby mogło być prawdziwe, prawdopodobnie nie jest prawdziwe. Warto sprawdzić koszty posiadania jednego z takich systemów laserowych. Niezadowalający poziom obsługi, niska niezawodność, długi czas realizacji w przypadku części zamiennych i brak obsługi klienta mogą być trudnościami, jakim trzeba będzie stawić czoła w związku z początkową dobrą ofertą.
ThPowyższe kluczowe czynniki należy traktować jako "praktyczną zasadę" przy porównywaniu plazmowych i światłowodowych systemów cięcia laserem o mocy do 20 kW. Podobnie jak w przypadku każdego porównania, przed zakupem należy użyć rzeczywistych danych wejściowych dla konkretnego sprzętu, zastosowania i lokalizacji