W Olympic Steel oprogramowanie ProNest do rozmieszczania dla systemów laserowych było na wagę złota
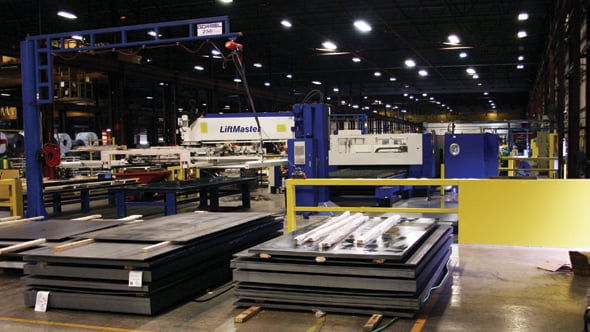
Firma i produkty
Olympic Steel to firma z siedzibą w Cleveland w stanie Ohio, zarządzająca 15 placówkami w Stanach Zjednoczonych. Jest wartościowym dostawcą płaskiej stali walcowanej. Dużą część działalności firmy stanowi obróbka typu „cut-to-shape” (przycinanie na wymiar), która jest wykonywana na ponad 30 maszynach do cięcia laserem, gazem i plazmą, pochodzących od różnych producentów.
Problem
Mimo że proces laserowego przycinania na wymiar znacznie przyczynił się do rozwoju i poprawy rentowności firmy Olympic w ostatnich latach, stosunkowo wysoki koszt zakupu sprzętu oferującego technologię CO2 oznacza, iż w celu osiągnięcia odpowiedniego zwrotu z inwestycji konieczny jest wysoki poziom produktywności. Kluczową rolę w zapewnieniu tego zwrotu z inwestycji odgrywa proces programowania CAM. Po dodaniu funkcji obróbki laserowej firma Olympic zaczęła szybko używać różnorodnych programów CAM — nie tylko producentów OEM, lecz również innych dostawców.
W związku z tym programiści CAM musieli odbywać szkolenia z obsługi wielu programów do rozmieszczania dla systemów laserowych, a firma musiała każdego roku mierzyć się z kosztami aktualizacji i utrzymania oprogramowania. Podjęto strategiczną decyzję, aby znaleźć i wdrożyć bardziej globalne i korporacyjne podejście do programowania CAM, które pomogłoby firmie Olympic Steel osiągnąć założone cele produktywności.
Rozwiązanie
Po wyczerpującym okresie analizy dostępnych rozwiązań dla operacji cięcia blach i arkuszy CNC w całym kraju firma zdecydowała się wdrożyć oprogramowanie ProNest®. Cory DeWitte, specjalista ds. planowania operacji CNC, mówi: „ProNest oferuje niesamowicie dużo fantastycznych i praktycznych funkcji — w szczególności dla naszych systemów laserowych”.Dodaje: „Moduł Unikanie kolizji dostępny w oprogramowaniu ProNest zapewnił nam ogromne korzyści, szczególnie w przypadku starszych laserów, w których podnoszenie i opuszczanie głowic odbywa się wolniej. Teraz między poszczególnymi operacjami wycinania otworów możemy przesuwać system z opuszczoną głowicą tnącą — bez konieczności pełnego cofania głowicy. Pozwoliło nam to zaoszczędzić nieco ponad godzinę czasu produkcji dziennie na każdy laser, co jest po prostu niesamowite! Obecnie obserwujemy znacznie mniejsze zużycie maszyn laserowych, co zmniejsza nasze koszty”.
Korzyści
Poprawa szybkości i wykorzystania materiału jest znaczna, co znakomicie przekłada się na ostateczną rentowność. DeWitte kontynuuje: „Z ProNest mogę teraz zaprogramować każdego dnia osiem różnych maszyn, co podwoiło moją wydajność programistyczną. Ponadto praktycznie zawsze osiągamy co najmniej siedemdziesiąt procent wykorzystania płaszczyzny, nawet w przypadku najbardziej wymagających kształtów części. Dodaje: „Moduł Cięcie na wspólnej linii dostępny w oprogramowaniu ProNest skrócił czas produkcji od dwunastu do nawet czterdziestu procent”.