Dzięki oprogramowaniu ProNest firma Craig Manufacturing może sprostać każdemu wyzwaniu
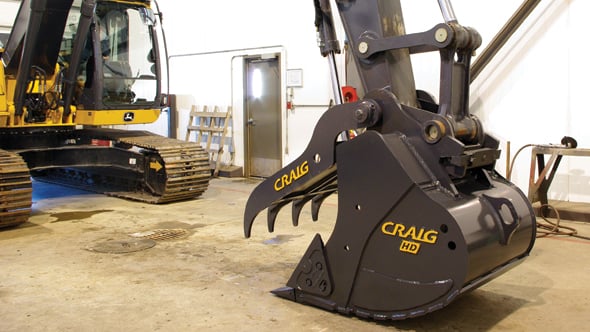
Firma i produkty
Craig Manufacturing z Hartland w New Brunswick, w Kanadzie, to największy prywatny producent sprzętu ciężkiego w Ameryce Północnej. Firma realizuje swoje operacje specjalistycznej produkcji i dystrybucji w niezwykle nowoczesnym zakładzie o powierzchni 71 000 stóp kwadratowych w Hartland, a także w dodatkowej placówce o powierzchni 15 000 stóp kwadratowych w Cambridge w Ontario.
Problem
Wraz z rozwojem działalności Craig Manufacturing pojawiła się potrzeba zwiększenia wydajności cięcia. „Nasz dotychczasowy program do rozmieszczania miał pewne ograniczenia. Tworzenie płaszczyzn było często czasochłonnym procesem. Każda godzina spędzona na rozmieszczaniu przekładała się na zaledwie około jedną godzinę cięcia. Oprogramowanie nie oferowało zbyt wielu funkcji automatycznych, dlatego na początku procesu powstało wąskie gardło” — powiedział Colden Wetmore, kierownik ds. operacji.
Rozwiązanie
Zespół decyzyjny przyjrzał się bliżej najnowszym rozwiązaniom Hypertherm, w tym oprogramowaniu CAD/CAM o nazwie ProNest® . Byli szczególnie zainteresowani tym, jak ProNest będzie współpracować z ich oprogramowaniem SOLIDWORKS® 3D CAD oraz jak będzie pasować do ich specyficznego przepływu pracy. Chcieli również poprawić jakość otworów, a ponieważ ProNest obsługuje technologię True Hole firmy® Hypertherm, była to dodatkowa zaleta.
Niewiele później w Craig Manufacturing pojawił się nowy stół plazmowy EBF. Wyposażony był w system cięcia HPR400XD, system sterowania numerycznego EDGE® Pro CNC, kontroler ArcGlide® THC oraz oprogramowanie do rozmieszczania ProNest.
„W przypadku naszego starego oprogramowania strojenie parametrów cięcia zajęło nam sześć lat, a mimo to nigdy nie udało nam się ich perfekcyjnie ustawić” — powiedział Wetmore. „Teraz na szczęście pojawia się ProNest, w którym wszystkie ustawienia parametrów są już wbudowane”.
Korzyści
Teraz, zamiast jednej godziny cięcia na jedną godzinę rozmieszczania, uzyskujemy 19 godzin cięcia, co oznacza 19-krotny wzrost wydajności! Ponadto poprawa dokładności i jakości dzięki technologii True Hole pozwoliły znacznie zmniejszyć liczbę operacji wtórnego szlifowania.
Wetmore dodaje: „Ponieważ zainstalowaliśmy nowy stół, oferujący technologię Rapid Part™, nawet nasz bardzo doświadczony operator nie nadąża za zwiększonymi wymaganiami załadunku i rozładunku arkuszy. Aby dopasować się do nowych warunków, musieliśmy zmienić nasz przepływ pracy”.Firma dostrzega również znacznie lepsze wykorzystanie materiałów. „Zredukowaliśmy nasz zapas surowców o połowę. Dzięki ProNest dzisiaj kierownictwo naszej firmy ma więcej powodów do zadowolenia, ponieważ udało się zmniejszyć ilość gotówki zamrożonej w przechowywanych arkuszach blachy bez rezygnacji z dostaw”.