Jak poprawić rentowność?
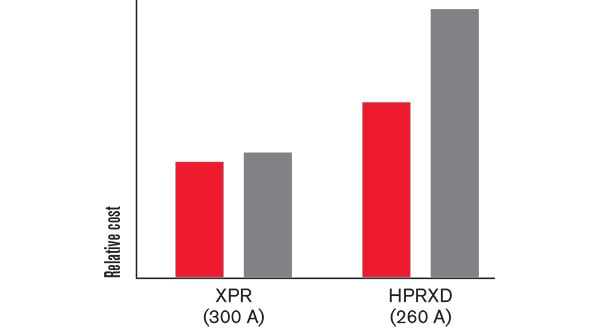
Powszechnym nurtem postępu technologicznego w branży cięcia plazmowego od samego początku jest nieustanne zmniejszanie kosztu jednego metra ciętego metalu. Ten koszt, znacznie zmniejszony w systemie XPR300™, to główny czynnik poprawiający rentowność użytkowników. Oferowane przez system XPR300 istotne zmniejszenie kosztów eksploatacji zależy od takich kilku czynników, jak szybkość cięcia, trwałość materiałów eksploatacyjnych oraz jakość cięcia.
Pierwszy czynnik to szybkość cięcia. System XPR300 tnie o 10–20% szybciej niż jego poprzednicy w przypadku najważniejszych grubości oraz niemal 50% szybciej przy grubościach materiału przekraczających 50 mm.
Thickness | XPR300 | HPR260XD | HPR400XD |
XPR300 |
HPR400XD i XPR300 % |
|
15 mm | 3440 | 3130 | 3950 | 10% | 15% | |
20 mm | 2550 | 2170 | 2805 | 18% | 10% | |
25 mm | 1950 | 1685 | 2210 | 16% | 13% | |
30 mm | 1530 | 1290 | 1790 | 19% | 17% | |
40 mm | 940 | 790 | 1160 | 19% | 23% | |
50 mm | 560 | 405 | 795 | 38% | 42% | |
60 mm | 385 | 258 | 580 | 49% | 51% | |
70 mm | 250 | N/A | 380 | N/A | 52% |
Szybkość cięcia (mm/min)
Należy również zwrócić uwagę, że system XPR300 jest bardziej efektywny, ponieważ do uzyskania podobnych efektów wymaga mniejszego natężenia prądu niż jego poprzednicy. Jak widać na poniższym wykresie, system XPR jest ustawiony na 170 A, jednak osiąga szybkość cięcia porównywalną z systemem HPR, w którym prąd wyjściowy wynosi 200 A.
Drugim kluczowym czynnikiem wpływającym na koszt eksploatacji jest trwałość materiałów eksploatacyjnych. W testach laboratoryjnych inżynierom Hypertherm udało się uzyskać niemal o 50% więcej cięć niż dotychczas. Podczas gdy dawniej jeden zestaw materiałów eksploatacyjnych wystarczał na około 1000 cięć, materiały dostępne do systemu XPR wystarczają w przypadku cięć 20-sekundowych stali miękkiej o grubości ¾ cala nawet na 1400 rozruchów. Jedną z przyczyn takiego wzrostu trwałości materiałów eksploatacyjnych jest bardzo zaawansowana konstrukcja systemu. W zasilaczu systemu zastosowano technologię Arc Response Technology, która automatycznie zapobiega zdarzeniom, które mogą doprowadzić do uszkodzenia systemu i zmniejszenia trwałości materiałów eksploatacyjnych.
Przyjrzyjmy się na przykład błędom zamknięcia. Występują one, gdy łuk jest gaszony w niekontrolowany sposób poprzez zejście z płyty lub odpadnięcie wewnętrznego profilu (na przykład otworu lub szczeliny), i są bardzo groźne dla materiałów eksploatacyjnych. Wynika to z faktu, że umieszczony w końcówce każdej elektrody emiter z hafnu nie może ponownie się zestalić po „pęknięciu” łuku. W efekcie przy każdym błędzie zamknięcia fragment hafnu jest wyrzucany z elektrody, co przyspiesza zużycie materiałów eksploatacyjnych.
Zasilacz XPR300 radzi sobie z tym problemem dzięki zastosowaniu zaawansowanej funkcji automatycznego wykrywania. System wykrywa zbliżający się błąd zamknięcia i gwałtownie wygasza łuk w kontrolowany sposób, znacznie wydłużając okres eksploatacji elektrody i dyszy. Podczas gdy w większości systemów plazmowych błędy zamknięcia skracają okres użytkowania materiałów eksploatacyjnych o około 50%, w systemie XPR300 wskaźnik ten wynosi zaledwie 10%. Przekłada się to na rzeczywistą korzyści w postaci trzykrotnie wyższej trwałości materiałów eksploatacyjnych.
Kolejnym istotnym czynnikiem jest jakość cięcia. System XPR300 oferuje całkiem nową klasę cięcia, którą nazwano X-Definition. Takie nowości, jak technologia Cool nozzle™, technologia Advanced arc stability, możliwość cięcia metali nieżelaznych w jakości HyDefinition, Vented Water Injection (VWI), funkcja mieszania gazów (H2, Ar, N2), technologia Vent-to-shield oraz technologia tłumienia plazmy, w której komora w dyszy pochłania fluktuacje ciśnienia i przepływu, pozwalają uzyskać wyjątkowo jednorodną jakość cięcia w bardzo długim okresie użytkowania.
Podczas gdy systemy HyPerformance HPR osiągały powtarzalną jakość cięcia części w zakresie ISO 4, system XPR300 zapewnia jakość w zakresie ISO 3, a w przypadku cieńszych materiałów — nawet w zakresie ISO 2.
Ta znaczna poprawa jakości cięcia stali miękkiej, a szczególnie stali nierdzewnej i aluminium, umożliwia wytwórcom wykonywanie na miejscu prac, które uprzednio były zlecane specjalistycznym centrom cięcia lub zewnętrznym firmom wycinającym laserowo. Dzięki temu mogą oni znacznie zmniejszyć koszty, poprawić efektywność łańcucha dostaw (produkować w systemie JIT), szybciej realizować prace oraz zyskać ogólnie lepszą rentowność.
Jakość krawędzi aluminium z zastosowaniem oferowanego przez system XPR300 i oczekującego
na opatentowanie procesu VWI
Jakość krawędzi stali nierdzewnej uzyskana dzięki wyjątkowej zdolności systemu XPR300 do mieszania gazów H2-Ar-N2 jako gazów plazmowych w konsoli OptiMix
Podsumowując, połączenie wyższej szybkości cięcia, wyższej trwałości materiałów eksploatacyjnych wynikającej z ochrony przed błędami zamknięcia, poprawionej jakości cięcia oraz znacznie lepszej powtarzalności cięcia prowadzi do obniżenia kosztów eksploatacji oraz poprawienia rentowności. W rzeczywistości przy prądzie 300 A system XPR300 może zmniejszyć względne koszty ciętego metra o ponad 50%.