Jak zwiększyć produktywność?
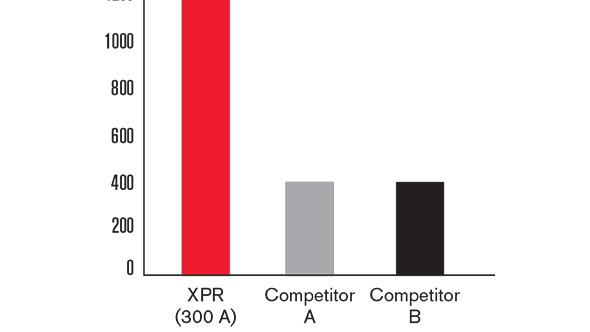
W przypadku cięcia przemysłowego na produktywność — albo jej brak — składają się trzy elementy. Są to szybkość cięcia, jakość cięcia i czas pracy systemu. Nowy system XPR300™ firmy Hypertherm doskonale radzi sobie z tymi trzema aspektami produktywności, ponieważ tnie szybciej, zapewnia jakość cięcia ograniczającą (a nawet eliminującą) dodatkowe operacje oraz wydłuża czas pracy systemu dzięki zastosowaniu „inteligentnych” technologii oraz funkcji oszczędzających czas.
Szybkość cięcia
Ponieważ system XPR300 ma do dyspozycji prąd o natężeniu 300 A oraz 63 kilowaty mocy, a jego poprzednik — jedynie 260 A, po prostu musi ciąć szybciej. Dokładny wzrost szybkości zależy od grubości ciętego materiału, jednak zwykle wzrost ten wynosi od 10 do 20% w przypadku materiałów o grubości 15–40 mm, 38% w przypadku materiałów o grubości 50 mm oraz prawie 50% z materiałami o grubości 60 mm.
Thickness | XPR300 | HPR260XD | HPR400XD |
XPR300 |
HPR400XD i XPR300 % |
|
15 mm | 3440 | 3130 | 3950 | 10% | 15% | |
20 mm | 2550 | 2170 | 2805 | 18% | 10% | |
25 mm | 1950 | 1685 | 2210 | 16% | 13% | |
30 mm | 1530 | 1290 | 1790 | 19% | 17% | |
40 mm | 940 | 790 | 1160 | 19% | 23% | |
50 mm | 560 | 405 | 795 | 38% | 42% | |
60 mm | 385 | 258 | 580 | 49% | 51% | |
70 mm | 250 | N/A | 380 | N/A | 52% |
Szybkość cięcia (mm/min)
System XPR nie tylko jest szybszy od HPR260XD®, lecz również bardziej efektywny. Jak widać na poniższych wykresach, system XPR300 wymaga jedynie 170 A, aby uzyskać szybkość cięcia, którą system HPR260XD osiąga przy 200 A. Teraz nie tylko można ciąć szybciej, lecz również zużywać w tym procesie mniej energii.
Jakość cięcia
W kontekście jakości cięcia system XPR300 oferuje całkiem nową klasę cięcia, którą nazwano
X-Definition™. Poprawia ona jakość cięcia, mierzoną za pomocą międzynarodowej normy ISO 9013, która określa jakość cięcia części wycinanych termicznie. W tej normie zastosowano skalę od 1 do 5, przy czym zakres 1 jest uznawany za najlepszy. Nowy system XPR gwarantuje jakość cięcia w zakresie ISO 3 w niemal całym okresie użytkowania materiałów eksploatacyjnych. Dla porównania system HPRXD firmy Hypertherm zapewnia jakość cięcia w zakresie 4, jak pokazano niżej.
Mimo że na powyższym wykresie przedstawiono efekty cięcia stali miękkiej o grubości 12 mm, testy laboratoryjne wykazały, że w przypadku cięcia cienkiej stali miękkiej z niższymi natężeniami prądu można uzyskać jakość w zakresie 2. Oprócz lepszej jakości cięcia warto także zwrócić uwagę na powtarzalność. Jak widać na powyższym wykresie, podczas testów laboratoryjnych z cięciami 20-sekundowymi jakość cięcia była niesamowicie jednorodna. Część wycięta przy użyciu całkiem nowych materiałów eksploatacyjnych wyglądała niemal tak samo jak część wycięta za pomocą materiałów, które mają za sobą ponad 1000 rozruchów.
Znaczna poprawa jakości cięcia jest obserwowana nie tylko podczas cięcia stali miękkiej, lecz również stali nierdzewnej i aluminium. Jest efektem zastosowania kilku nowych, oczekujących na opatentowanie technologii. Jedną z nich jest proces Vented Water Injection, który łączy azotowy gaz plazmowy z osłoną wodną w celu lepszego wyrównania i skoncentrowania łuku plazmowego. Druga to technologia wentylowanej osłony Vent-to-Shield, która odzyskuje wodór z wentylowanego gazu plazmowego, a następnie miesza go z gazem osłonowym. Efektem użycia obu tych technologii są bardziej prostokątne krawędzie cięcia, mniejsza kątowość oraz lepsze wykończenie powierzchni w porównaniu do systemu HPR. System XPR wykorzystuje również proces zaawansowanej stabilizacji łuku plazmowego Advanced Arc Stability oraz nowe protokoły segmentacji łuku do wycinania otworów, które oferują jakość przewyższającą czołowy proces branżowy True Hole firmy Hypertherm.
Czas pracy systemu
Mimo tego, że w systemie XPR zastosowano wiele technologii, w rzeczywistości jest on mniej skomplikowany niż jego poprzednicy. Czujniki zainstalowane w zasilaczu przekazują ulepszone kody diagnostyczne i znacznie więcej danych monitorowania systemu. Dzięki temu skraca się czas rozwiązywania problemów, a operator ma do dyspozycji aktywne dane pozwalające lepiej optymalizować pracę systemu.
Ponadto system zaprojektowano tak, aby korzystał z mniejszej liczby konsol i połączeń. Operatorzy nie muszą dzięki temu spędzać dużo czasu na ustawianiu i mogą skoncentrować się na cięciu. Pomocne funkcje to między innymi system EasyConnect™, dzięki któremu operator może szybko podłączyć palnik do konsoli palnika bez użycia żadnych narzędzi. Oczekująca na opatentowanie technologia mocowania elektrody QuickLock™ sprawia, że do montażu wystarczy zaledwie ¼ obrotu, co skraca prace związane z ustawianiem. Z kolei nowa konstrukcja palnika pozwala operatorom szybko wymieniać palniki za pomocą jednej dłoni. Wszystkie konsole są wyposażone w zaawansowane funkcje automatycznej kontroli gazu, dzięki którym operatorzy mogą wybierać i uruchamiać wszystkie prace cięcia bezpośrednio z systemu CNC. Zasilacz zawiera z kolei moduł łączności bezprzewodowej umożliwiający zdalne monitorowanie parametrów systemu (lub wielu systemów).
Czas pracy bez przestojów, nie wspominając o kosztach eksploatacji, poprawiono jeszcze bardziej dzięki zwiększeniu trwałości materiałów eksploatacyjnych. Oczekująca na opatentowanie funkcja o nazwie Cool nozzle™ podaje płyn chłodzący bezpośrednio do dyszy, zapewniając 40-procentowe zwiększenie okresu użytkowania materiałów eksploatacyjnych. Opatentowana technologia PowerPierce® realizuje zasadniczo tę samą funkcję w przypadku osłony. Przekazuje do osłony płyn chłodzący, który zapobiega uszkodzeniu osłony poprzez chronienie jej przed stopionymi odpryskami metalu powstającymi podczas przebijania. Zawór w gniazdku palnika gwarantuje szybszą i bardziej precyzyjną kontrolę przepływu gazu,
co znacznie wydłuża czas użytkowania procesu tlenu i istotnie przyspiesza proces zamknięcia prądu. Uzyskane dzięki temu ograniczenie liczby błędów zamknięcia w większości zastosowań przekłada się na niemal 3-krotnie większą trwałość materiałów eksploatacyjnych niż w innych systemach, co pokazano niżej. Mniej czasu poświęcanego na wymianę materiałów eksploatacyjnych oznacza więcej czasu na cięcie oraz brak dodatkowych czynności.
Teraz wiadomo już wszystko. System XPR300 zawdzięcza znakomitą produktywność połączeniu wyższej szybkości cięcia, poprawionej jakości cięcia oraz dłuższego czasu pracy.
Jak zwiększyć produktywność?