10 najczęstszych błędów związanych z cięciem plazmowym
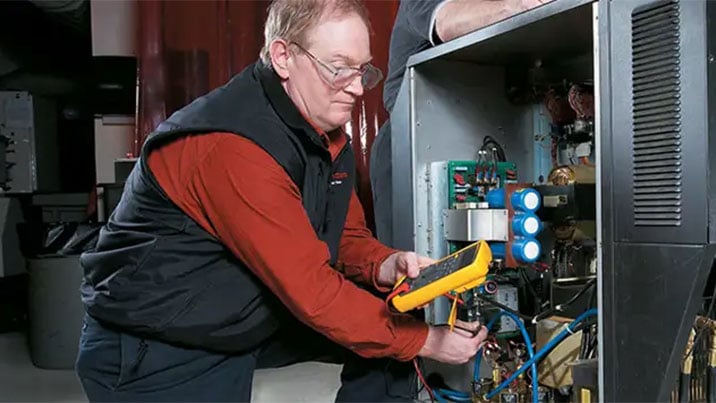
Dobry operator dysponujący należycie serwisowanym systemem PAC może zaoszczędzić warsztatowi wiele godzin czasu przestoju oraz tysiące dolarów wydatków operacyjnych. Te oszczędności przekładają się na większe zyski z operacji cięcia oraz lepszą rentowność firmy. Unikaj tych częstych błędów:
- Używanie materiałów eksploatacyjnych do ich „wydmuchania”
W pojemniku ze zużytymi częściami prawdopodobnie można znaleźć części, które były używane do samego końca trwałości. Używanie bardzo zużytych materiałów eksploatacyjnych może prowadzić nie tylko do zniszczenia dobrego arkusza metalu, lecz skutkować także kosztowną usterką palnika oraz niepotrzebnym czasem przestoju w pracy. Używanie części do momentu awarii to kwestia, której łatwo uniknąć. Zużycie materiału eksploatacyjnego można rozpoznać na kilka sposobów. Doświadczony operator może to stwierdzić na podstawie wydawanego dźwięku lub koloru łuku albo subtelnych zmian w wysokości palnika. Jednak najlepszą metodą oceny stanu części palnika jest okresowe sprawdzanie jakości ciętej krawędzi metalu oraz kontrolowanie części palnika wtedy, gdy jakość ulega pogorszeniu. Należy prowadzić dokumentację zmieniającej się w czasie średniej trwałości części eksploatacyjnych (wyrażonej w liczbie startów lub czasu pracy łuku) oraz opracować wytyczne oczekiwanej trwałości na bazie natężenia prądu, materiału i grubości. Po ustaleniu średniej trwałości części eksploatacyjnych operator będzie wiedzieć, kiedy skontrolować lub wymienić część i zapobiec w ten sposób bardzo poważnej usterce. - Zmiana materiałów eksploatacyjnych
Całkowitą przeciwnością są materiały eksploatacyjne, które są wymieniane zbyt często. Zamiast wymieniać materiały eksploatacyjne po upływie zdefiniowanej liczby godzin, operator powinien przyjrzeć się stopniowi ich zużycia. Czy na wewnętrznej lub zewnętrznej powierzchni dyszy są widoczne wgłębienia? Czy końcówka nie jest już okrągła? Jeśli odpowiedzi brzmią „tak”, materiał nadaje się do wymiany. W przeciwnym razie można z niego nadal korzystać. Aby stwierdzić, czy elektroda jest zużyta, należy sprawdzić wgłębienie na samym środku wkładki z hafnu. Jeśli jest zbyt duże, elektroda nadaje się do wymiany. Pierścienie zawirowujące gaz powinny być wymieniane wyłącznie wtedy, gdy szczegółowa kontrola wykaże obecność brudu lub smaru w otworach, pęknięcia, przepalenia łuku lub nadmierne zużycie. To samo dotyczy osłon, które powinny być wymieniane tylko wtedy, gdy wykazują objawy uszkodzeń fizycznych. Osłony często można wyczyścić z odprysków metalu i ponownie wykorzystać. - Stosowanie nieprawidłowych parametrów i części
Dobór materiału eksploatacyjnego zależy od ciętego materiału i jego grubości, natężenia prądu i gazu plazmowego oraz innych parametrów cięcia. W podręczniku operatora znajdują się informacje o materiałach eksploatacyjnych pasujących do różnych prac cięcia. Stosowanie nieodpowiednich materiałów eksploatacyjnych może skutkować zmniejszeniem trwałości części oraz pogorszeniem jakości cięcia.
Szczególnie ważne jest używanie części przy odpowiednim natężeniu prądu. Najlepszą jakość cięcia oraz trwałość części eksploatacyjnych można zwykle uzyskać wtedy, gdy natężenie prądu jest ustawione na 95% wartości znamionowej dyszy. Jeśli prąd będzie zbyt mały, cięcie będzie kiepskie, natomiast gdy prąd będzie zbyt duży, ucierpi trwałość dyszy. - Nieprawidłowe zmontowanie palnika
Palnik należy zmontować w taki sposób, aby wszystkie części dokładnie do siebie pasowały i były prawidłowo wyosiowane. Wtedy można uzyskać dobry styk elektryczny oraz prawidłowy przepływ gazu i płynu chłodzącego przez palnik. Podczas wymiany części materiały eksploatacyjne należy trzymać na czystej szmacie warsztatowej, aby zapobiec zanieczyszczeniu palnika brudem i pyłem metalicznym. Zachowanie czystości podczas montażu palnika jest bardzo ważne i często zaniedbywane. Podczas smarowania pierścienia uszczelniającego o przekroju okrągłym należy nałożyć tylko tyle smaru, aby pierścień błyszczał. Za duża ilość smaru może skutkować zapychaniem elementu zawirowującego gaz oraz zanieczyszczeniem palnika pyłem metalicznym. To z kolei może prowadzić do niekontrolowanego zapłonu łuku w komorze plazmy oraz do ewentualnego uszkodzenia palnika. Smaru nigdy nie należy nakładać na palniki. Może to skutkować szkodliwym zapłonem łuku oraz zapłonem wewnątrz palnika. - Zaniedbywanie rutynowej konserwacji
W przypadku odpowiedniej dbałości palniki mogą wytrzymać miesiące, a nawet lata pracy. Gwinty palnika powinny być zawsze czyste, a powierzchnie montażowe sprawdzone pod względem zanieczyszczeń i uszkodzeń mechanicznych. Wszelki brud, pył metaliczny i nadmiar smaru na pierścieniu uszczelniającym o przekroju okrągłym należy usuwać. Do czyszczenia palnika używać bawełnianego wacika oraz środka do czyszczenia styków elektrycznych lub nadtlenku wodoru. - Niesprawdzanie przepływu płynu chłodzącego i przepływu gazu
Przepływ i ciśnienie gazu oraz płynu chłodzącego należy sprawdzać codziennie. Niedostateczny przepływ sprawia, że materiały eksploatacyjne są nienależycie chłodzone, co prowadzi do zmniejszenia trwałości części eksploatacyjnych. Nieprawidłowy przepływ chłodziwa wynikający ze zużycia pompy, zapchania filtrów, niskiego poziomu płynu chłodzącego itd. to częsta przyczyna uszkodzenia części i palnika. Aby utrzymać łuk tnący, należy zachować stałe ciśnienie gazu. Zbyt duże ciśnienie gazu to częsta przyczyna „trudnego rozruchu”, czyli sytuacji, w której palnik nie może zapalić łuku mimo spełnienia wszystkich pozostałych warunków prawidłowej pracy. Za duże ciśnienie gazu powoduje także gwałtowne zużywanie się elektrody. Podobnie gaz plazmowy musi być utrzymywany w czystości, aby zapobiec zmniejszeniu trwałości materiałów eksploatacyjnych i palnika. Systemy sprężonego powietrza są szczególnie narażone na zanieczyszczenie olejem, wilgocią i cząstkami. - Przebijanie zbyt nisko
Odsunięcie palnika, czyli odległość od końcówki dyszy do elementu obrabianego, ma krytyczne znaczenie pod względem jakość cięcia oraz trwałości części eksploatacyjnych. Nawet niewielka odchyłka wysokości palnika może mieć wpływ na kątowość ciętej powierzchni. Szczególnie ważna podczas przebijania jest wysokość palnika. Bardzo powszechnym błędem jest przebijanie zbyt nisko. Wtedy stopiony metal rozpryskuje się z przodu dyszy i osłony, powodując uszkodzenie części i związane z tym problemy z jakością cięcia. Jeśli palnik przebija po dotknięciu metal albo jest przeciągany wzdłuż powierzchni podczas cięcia, może nawet dochodzić do „gaśnięcia” łuku. Gdy łuk „gaśnie”, może dojść do uszkodzenia elektrody, dyszy, elementu zawirowującego, a nawet palnika. Przebijanie na wysokości 1,5–2 razy wyższej niż zalecana chroni palnik i części przed uszkodzeniem. - Cięcie zbyt szybko albo zbyt wolno
Cięcie zbyt szybko lub zbyt wolno skutkuje problemami z jakością cięcia. Jeśli szybkość jest zbyt mała, na odciętych fragmentach można dostrzec „żużel wolnobieżny”, czyli nagromadzenie grudek żużlu wzdłuż dolnej krawędzi. Małe szybkości mogą także powodować poszerzenie szczeliny oraz powstawanie nadmiernej ilości rozprysków na górze. Jeśli szybkość jest zbyt duża, łuk opóźnia się w szczelinie, powodując ukosowanie krawędzi, wąską szczelinę oraz małe i twarde grudki żużlu wzdłuż dolnej krawędzi odcinanego fragmentu. Żużel szybkobieżny jest trudny do usunięcia. Przy prawidłowo dobranej szybkość cięcia ilość żużlu jest minimalna. Przekłada się to na czystą krawędź, która praktycznie nie wymaga obróbki końcowej przed przekazaniem do dalszego etapu produkcji. - „Rozciąganie” łuku
Rozciąganie łuku następuje na początku i na końcu cięcia, gdy łuk musi się „rozciągnąć” (tj. odchylić od prostej, prostopadłej ścieżki) w celu odnalezienia metalu. Rozciąganie łuku może skutkować cięciem przez łuk bocznych ścianek dyszy. Podczas startu od krawędzi łuk plazmowy powinien być aktywowany, gdy otwór dyszy jest wyśrodkowany dokładnie nad krawędzią elementu obrabianego. Należy o tym pamiętać podczas operacji przebijania przebijarką/plazmą (odchylenie od prostej, prostopadłej ścieżki). Rozciąganie łuku może skutkować cięciem przez łuk bocznych ścianek dyszy. Podczas startu od krawędzi łuk plazmowy powinien być aktywowany, gdy otwór dyszy jest wyśrodkowany dokładnie nad krawędzią elementu obrabianego. Należy o tym pamiętać podczas operacji przebijania przebijarką/plazmą, gdy łuk jest uruchamiany od przebitego otworu. W tym zastosowaniu łuk należy uruchomić od krawędzi, a nie od środka przebitego otworu. Rozciągnięcie łuku może również nastąpić na końcu cięcia, gdy palnik jest zaprogramowany do przejścia za płytę z włączonym łukiem albo gdy „wyprowadzenie cięcia” podąża za szczeliną uprzednio odciętego metalu. W celu zminimalizowania tego efektu można zmienić moment wysłania sygnału wyłączenia łuku oraz sposób programowania wyprowadzenia cięcia. - Zderzenie palnika
Upadki i zderzenia mogą skutkować nieodwracalnym uszkodzeniem palnika. Kolizjom palnika z elementem obrabianym można zapobiec, programując system cięcia kształtów w taki sposób, aby palnik przemieszczał się wokół ciętych części (a nie nad nimi). Czujniki wysokości palnika często chronią przed zderzeniami palnika, uwzględniając zmianę charakterystyki materiału. Jednak kontrolery wysokości z regulacją napięcia nie gwarantują całkowitej ochrony palnika. Na końcu cięcia występuje na przykład często „nurkowanie palnika”, gdy palnik podąża zbyt długo za szczeliną. (Kontroler wysokości palnika zmniejsza wysokość, aby skompensować wzrost napięcia towarzyszący rozciągnięciu łuku). W celu zminimalizowania tego efektu można zmienić program wyprowadzenia cięcia oraz parametry kontrolera wysokości palnika. Wreszcie, w zapobieganiu uszkodzeniom palnika wynikającym ze zderzenia pomagają urządzenia mocujące palnik z funkcją odłączenia.