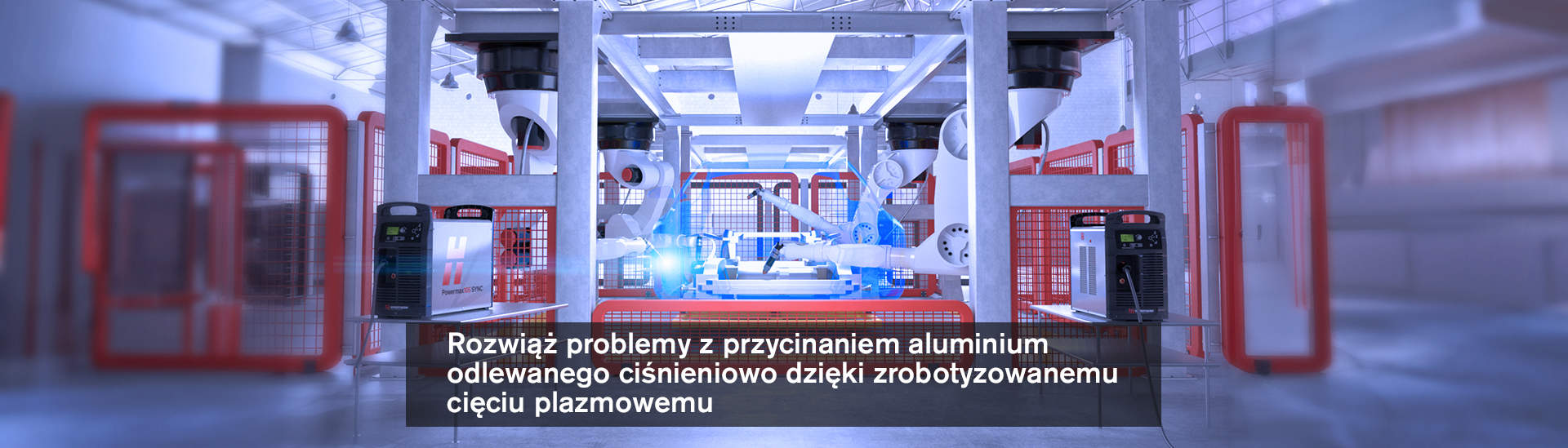
Aby zachować konkurencyjność, producenci samochodów muszą zapewniać najwyższą jakość i wydajność oraz obniżać koszty. Rentowność zależy od zidentyfikowania możliwości poprawy wydajności. Dlatego właśnie globalni producenci samochodów coraz częściej stosują technologię giga casting — wytwarzanie wielkogabarytowych części z jednego odlewu — która eliminuje potrzebę spawania dziesiątek części nadwozia. Mniejsza liczba części zmniejsza masę pojazdów i zużycie paliwa oraz umożliwia wyjście naprzeciw rosnącemu zapotrzebowaniu na pojazdy elektryczne zasilane akumulatorowo i bardziej wydajne pojazdy wyposażone w silnik spalinowy.
Nadmiar materiału z formy należy usunąć po wyjęciu części odlewanej z prasy. Właśnie tu technologia zrobotyzowana cięcia plazmowego pomaga zrewolucjonizować produkcję automatyczną.
REUTERS
„Producenci samochodów korzystający z maszyn do odlewania aluminium twierdzą, że mogą zmniejszyć o 40% inwestycje niezbędne do produkcji nadwozia — drugiego najdroższego komponentu pojazdu po silniku”
Riccardo Ferrario,
Dyrektor generalny, IDRA Group
Wyzwania, z którymi zmagają się producenci z branży motoryzacyjnej
-
Tradycyjne metody usuwania materiału, takie jak okrawarki, często ograniczają możliwości projektowania produktów, wiążą się z wysokimi początkowymi kosztami inwestycyjnymi, długim czasem przezbrojenia oraz większym poziomem odpadów ze względu na różnice w częściach.
-
Niedobór wykwalifikowanych pracowników zwiększa koszty i zmniejsza produktywność, szczególnie w przypadku jakości usuwania materiału.
-
Zmiany formy skutkują kosztownymi modyfikacjami narzędzi.
-
Czasochłonne metody usuwania zalewek/materiału wpływają na czas między cięciami.
-
Metody ręczne i półautomatyczne powodują powstawanie opiłków, w tym opiłków o dużej zawartości metalu, co może prowadzić do wydłużenia przestojów i negatywnie wpływać na integralność ostatecznego odlewu.
-
Ręczna praca zwiększa ryzyko urazów w miejscu pracy.
Wyzwania związane z okrawarkami i rozwiązaniami do zrobotyzowanego cięcia plazmowego.
Wyzwania | Rozwiązania |
---|---|
Różnice w odlewanych częściach mogą powodować ich blokowanie się w okrawarce. | Dzięki niewielkim zmianom w narzędziach można zaprogramować nową ścieżkę robota do okrawania dowolnej części. |
Nie dostosowuje się szybko do różnych kształtów części / geometrii obrabianych przez maszynę odlewniczą. | Zrobotyzowane cięcie plazmowe można szybko zaprogramować do cięcia nowych części i kształtów, zyskując w ten sposób elastyczną komórkę do okrawania, która może obsługiwać wiele projektów odlewniczych. |
Wąskie tolerancje powodują powstawanie bezwymiarowych części trafiających na złom. | Cięcie plazmowe zapewnia większe odsunięcie narzędzia od części w celu uniknięcia kolizji. |
Ogromne okrawarki zajmują cenną powierzchnię warsztatową. | Przecinarka plazmowa zajmuje minimalną powierzchnię warsztatową, łatwo zintegrować ją z robotami, wymaga niewielkiej konserwacji i charakteryzuje się długim okresem eksploatacji. |
Systemy plazmowe Hypertherm to niezawodny wybór dla producentów z branży motoryzacyjnej
Systemy Powermax SYNC® zaprojektowano tak, by z łatwością integrowały się ze stacjami zrobotyzowanymi do cięcia odlewanych części metalowych. Znacznie skracają czas, nakład pracy i koszty eksploatacji w porównaniu z alternatywnymi technologiami. System Powermax wyróżnia się na tle konkurencyjnych systemów i innych technologii kluczowymi cechami, które sprawiają, że jest on chętnie wybierany przez czołowych producentów samochodów i pojazdów elektrycznych poruszających się obecnie po drogach.
Cechy wyróżniające rozwiązanie Powermax SYNC
Szybka wymiana części oszczędza czas i zmniejsza koszty robocizny
Niezależnie od wariacji odlewu czy różnic w geometrii części, nową ścieżkę robota można zaprogramować tak, aby przycinała dowolną część i kształt w zrobotyzowanej komórce okrawającej.
Większy odstęp między narzędziem a częścią upraszcza programowanie robota.
Większe odstępy między narzędziem a częścią niż w przypadku lasera światłowodowego sprawiają, że technologia plazmowa lepiej nadaje się do zastosowań zrobotyzowanych, w których spodziewana jest zmienność części, co pozwala zapobiec kosztownym przestojom spowodowanym kolizjami narzędzia z częścią.
WYBÓR JEST PROSTY
Czołowi producenci z branży motoryzacyjnej przetestowali bardziej znane technologie, w tym laser światłowodowy, i odkryli, że najlepszym rozwiązaniem jest system plazmowy Powermax do końcowej obróbki odlewów aluminiowych.
Opatentowane materiały eksploatacyjne w formie jednoczęściowych wkładów z możliwością zapisu danych eliminują błędy operatora.
Dzięki wbudowanemu układowi logicznemu RFID i rewolucyjnym materiałom eksploatacyjnym w formie jednoczęściowych wkładów z zaawansowanymi funkcjami wymiany danych z palnikiem SmartSYNC możliwa jest analiza wydajności pod kątem liczby rozruchów i transferów oraz czasu pracy łuku.
-
Nasza opatentowana technologia umożliwia szybką wymianę narzędzi i praktycznie eliminuje przestoje.
-
Inteligentny jednoczęściowy materiał eksploatacyjny wskazuje źródło zasilania typu wkładu zamontowanego na palniku.
-
System cięcia automatycznie ustawia prawidłowy prąd i gaz, co optymalizuje proces cięcia i eliminuje konieczność ingerencji operatora.
-
Materiały eksploatacyjne w formie jednoczęściowych wkładów są ekonomicznym rozwiązaniem i nadają się do recyklingu.
Unikatowy jednoczęściowy wkład z wbudowanym układem logicznym
System Powermax SYNC z wbudowanym układem logicznym i rewolucyjnymi materiałami eksploatacyjnymi w formie jednoczęściowych wkładów z zaawansowanymi funkcjami wymiany danych z palnikiem poprawia wydajność, upraszcza zarządzanie zapasami i skraca czas przestojów. Dzięki danym dotyczącym wydajności pochodzącym z aplikacji obsługującej wkłady, interfejsu użytkownika systemu i zgodnego systemu CNC możesz podejmować świadome decyzje, które pomogą Ci usprawnić proces cięcia.
Dlaczego Hypertherm Associates
We wszystkim, co robimy, wierzymy w kwestionowanie tego, co uznawane jest za niemożliwe. Pobudzając wyobraźnię — naszą i naszych klientów — projektujemy produkty, które kształtują globalny krajobraz i są przyjazne użytkownikom oraz środowisku. Nasze sprawdzone technologie cięcia i kształtowania pomagają budować bardziej połączony i ciekawy świat.
Omówmy Twoje potrzeby w zakresie końcowej obróbki odlewów
Nasz proces komunikacji:
Twój dedykowany opiekun skontaktuje się z Tobą, aby zrozumieć Twój projekt i wyzwania, z którymi się mierzysz. Następnie zorganizuje dalsze działania, które obejmą zapewnienie bezpośredniego dostępu do naszego zespołu inżynierów, specjalizującego się w aplikacjach związanych z końcową obróbką odlewów.
Następne kroki mogą obejmować:
-
Testowanie produktu
-
Testowanie weryfikacyjne procesu
-
Współpraca między producentami samochodów a preferowanymi partnerami