연안경비대를 지원하기 위한 정확한 일정 관리
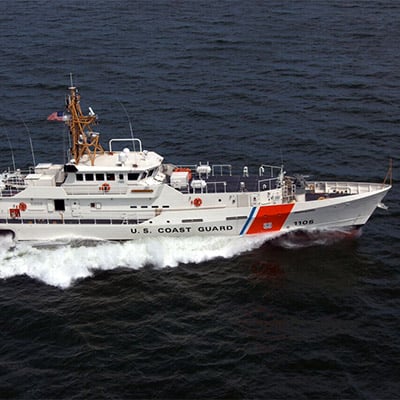
루이지애나, 바이우 라푸쉐의 강둑에서는 교향곡이 울려 퍼집니다. 이 교향곡은 선박이 건조되는 소리입니다. 이곳에서는 미 육군을 위해 육상 이중 선체 바지선, 해안 유조선, 터그 보트, 굴착 장치, 리프트 보트, 푸시 보트 및 순찰 보트 등의 배가 만들어지고 있습니다. Bollinger Shipyards는 제2차세계대전에 참전했던 도널드 볼링거(Donald Bollinger)의 삼형제가 창립한 70년 전통의 조선소입니다.
Bollinger의 조선 작업은 일반적으로 네덜란드에 기반을 둔 국제적 조선 및 설계기업인 Darnen 그룹으로부터 설계 라이선스를 획득하면서 시작됩니다. Darnen의 설계는 실제로 가장 최근의 연안경비대 관련 작업이었던 38 Sentinel급 고속 응답 커터의 기반을 이루고 있습니다. 이 작업은 길이 154 피트, 너비 26 피트인 Darnen 스탠 순찰 선박을 기준으로 합니다. Bollinger는 현재까지 23척의 커터를 납품했고, 가장 최근에는 USCGC 벤자민 데일리(Benjamin Dailey)가 플로리다 주 키웨스트의 연안경비대에 인도되었습니다. Bollinger는 지난 30년간 연안경비대에 약 150척의 선박을 인도했습니다.
Bollinger의 신축 생산 부서의 대니 리차델(Danny Richardel) 부사장은 보트를 생산하는 모든 조선 작업에는 엄밀하게 조정된 작업팀이 필요하다고 설명합니다. Bollinger의 엔지니어들은 고객과 긴밀하게 협력하여 최종 제품을 구성할 금속의 절단 및 용접을 시작하기 전에 선박의 정체성을 확인하고 필요한 수정 작업을 진행합니다. Bollinger는 설계 엔지니어 팀 외에도 기계, 전기, 용접 엔지니어와 프로젝트 관리자, 자재 관리자, 회계사, 전기사, 목수, 제작사, 용접사들을 다양하게 고용하고 있습니다. 모두 일주일에 5일을 일하며, 최대 2교대, 도색팀 같은 일부 작업자들의 경우에는 필요하면 주말에도 일을 합니다.
Bollinger 교향곡이 완벽한 화음을 내기 위해서는 일정을 정확히 지키는 것이 매우 중요합니다. 작은 실수 하나로도 신중하게 계획된 프로젝트를 위태롭게 할 수 있으며, 완공 일자가 미뤄지거나 예산 급증 등의 결과를 초래할 수 있습니다. 이러한 위험을 최소로 유지하기 위해 Bollinger는 자사의 ISO-9001 시설에서 군더더기 없는 제조 방식만을 고집합니다. 걸프만에 위치한 많은 시설들 중 하나인 루이지애나, 락포트에 위치한 250 에이커의 조선소, Bollinger는 Hypertherm 제품들에 의지하고 있습니다. HyPerformance® HPR260 플라즈마 시스템, MAX200® 컨벤셔널 플라즈마, HyPrecision® 50 워터젯 펌프와 이 모든 장비를 하나로 이어주는 ProNest CAD/CAM 네스팅 소프트웨어가 그것입니다.
Bollinger의 첫 플라즈마 시스템은 Hypertherm의 제품이 아니었습니다. 불행히도 그 결과는 만족스럽지 않았습니다. 절단 품질이 기준에 미치지 못하여 직원들이 2차 작업에 많은 시간을 낭비해야만 했습니다. 이에 불만족한 Bollinger는 락포트에 있는 기존의 CNC 테이블에 새로운 Hypertherm 플라즈마 시스템을 도입할 것을 권유한 ALLtra Corporation의 제안에 관심을 가졌습니다. Bollinger는 제안에 동의했고 결과에 매우 만족했습니다.
“절단 공정의 속도와 작업량은 우리에게 매우 중요합니다. 절단 공정은 신속해야 하며 동시에 정확하고 깔끔해야 합니다.”품질 관리 시스템 부사장인 데니스 팬가이(Dennis Fanguy)는 이렇게 설명했습니다. “HyPerformance 플라즈마는 2차 연마 작업의 필요성을 제거해주는 훌륭한 일꾼입니다. 이제 절단된 부품을 곧바로 사용할 수 있으며, 부품 번호를 붙일 수 있습니다.”
Bollinger는 여러 유형의 금속을 절단하고 있습니다. 일반적으로 보트 선체는 강도를 위해 연강으로 제작되지만, 상부 구조는 더 가벼운 알루미늄으로 제작됩니다. Bollinger는 주로 5086 및 5456 등급의 알루미늄과 AH36 및 A36 연강, 때로는 스테인리스 강까지 플라즈마로 절단합니다. 파이프, 파이프 새들 및 구멍도 플라즈마로 절단합니다. 이 회사는 워싱턴 주에 있는 Jesse Co.의 MAX200을 8축 로봇 파이프 새들와 홀 절단 장비에 사용합니다. 플라즈마로 절단할 수 없는 부품도 있습니다. 수밀 도어에 사용되는 작고 복잡한 부품은 매우 높은 수준의 정밀도와 별도의 공정을 필요로 합니다.
“우리는 항상 비용을 관리하고 지출을 절감할 방법을 찾고 있습니다. 과거에는 수밀 도어를 자체 제작했지만 전문 기술을 상실하고 해당 품목을 구매하기 시작했습니다.”라고 리차델은 설명했습니다. 하지만 거기에 문제가 있었습니다. 도어와 해치의 구입 비용이 너무 컸기 때문입니다. 아웃소싱도 시도했지만 품질과 일정 문제에 부딪혔습니다. 리차델 부사장은 “아웃소싱으로 인해 작업 속도가 느려졌습니다. 프로젝트의 여러 가지 문제로 인해 작업 시간이 지연되었고, 고객사는 품질에 만족하지 못 했습니다”라고 설명합니다. Bollinger 팀은 사내에서 작업을 다시 시작하기로 결정했습니다.
회사는 Koike Aronson에 의뢰하여 Hypertherm HyPrecision 펌프가 장착된 K-젯 6 12 시스템을 설치하기로 결정했습니다. 지난 10월에 시스템을 설치한 후 회사는 자체 수밀 도어 및 해치를 제작 중입니다. 리차델 부사장은 “도어는 워터젯 구매를 위한 촉매제 역할을 해주었지만, 실제로도 우리는 사내에서 더 많은 작업을 하고 싶었습니다”라고 말합니다. 팬가이 부사장은 “워터젯은 매우 정확합니다. 부품에는 열에 영향을 받는 부분이 없으며 기계 설정이 빠릅니다. 또 금속, 플라스틱, 고무 등의 다양한 재료를 절단할 수 있습니다”라고 덧붙입니다.
Bollinger는 또한 예상치 못한 이점을 발견했습니다. K-젯 시스템은 매우 효율적이기 때문에 Bollinger는 다른 조선소에 제조한 도어를 판매하여 회사의 또 다른 수익원을 창출하고 있습니다. “하루 종일 워터젯의 ROI를 예측했고 결과는 긍정적이었습니다”라고 리차델 부사장은 말합니다. 그는 투자에 대한 수익 회수에 2년 미만의 시간이 소요될 것으로 예상했습니다.
Bollinger는 작업 속도와 절단 품질 뿐만 아니라 아웃소싱 작업에서는 제어하기 힘든 낭비의 최소화에도 중점을 두고 있습니다. Bollinger가 선택한 설계 도구는 조선 및 해양 산업에서 사용되는 3D 모델링 도구인 ShipConstructor입니다. 플라즈마 및 워터젯 테이블에서 Hypertherm의 ProNest 2017을 사용하여 CAD/CAM 소프트웨어가 부품을 효율적으로 중첩할 수 있어 스크랩이 거의 남지 않습니다. 또한 ProNest의 선택적 베벨 기계 모듈을 사용하여 경사진 모서리를 절단합니다.
이제 수개월간 지속된 조선 작업이 마무리되고 선박을 인도할 시간이 되었습니다. 연안경비대의 Sentinel급 고속 응답 커터와 같은 보트는 탠덤 크레인 시스템을 사용하여 바이우 라푸쉐에 조심스럽게 내려집니다. 연안경비대 선박이 종종 겪는 까다로운 조건에서 완벽한 항해를 보장하기 위해 엄격한 테스트를 거친 후 Bollinger는 배송 일정을 정하고 다시 새로운 작업을 시작합니다.