강의 자동화
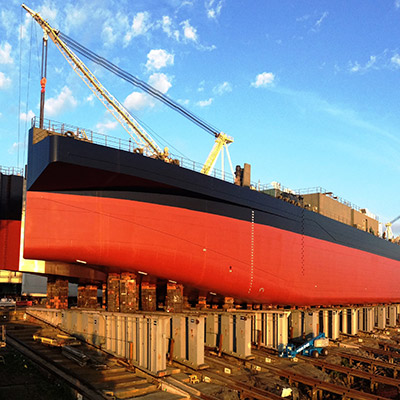
오리건의 윌라멧(Willamette) 강 기슭, 미국 북서부 최대의 조선소는 아주 바쁘게 돌아가고 있습니다.
포틀랜드의 Gunderson Marine 팀은 전력을 다해 일하고 있습니다. 한 무리의 남자와 여자들이 설계도를 들여다보고 있으며, 트럭은 부두로 이동하고, 지게차들은 다량의 강철판을 분주하게 나르고 있습니다.
작업은 24시간 동안 교대로 쉬지 않고 이루어집니다. 1940년대 초, 쳇 건더슨(Chet Gunderson)이 당시 20년된 사업을 확장하기 위해 부둣가에 11에이커의 부지를 구입한 후로 언제나 그래왔습니다. 쳇은 조선소를 계획했고 당시 미국은 제2차 세계대전에 참여하려는 상황이었기 때문에 시기는 더할 나위 없이 적절했습니다. 얼마 지나지 않아 미 해군이 사용할 포함, 구명정, 상륙함들의 주문이 빗발쳤습니다.
현재 The Greenbrier Companies가 소유하고 있는 Gunderson Marine은 그 후로 수천 대의 선박을 건조해 왔습니다. 이러한 선박에는 해운, 데크, 더블헐 탱크, 레일카, 덤프, 중공업 기타 등등 상상할 수 있는 모든 종류의 바지선이 포함됩니다.
Gunderson의 100여 년에 걸친 역사 동안 대부분의 선박들과 그 이전의 휠 허브, 트레일러들은 거의 매뉴얼 방식으로 만들어졌습니 조선소의 생산 진행자인 월트 스토크먼(Walt Stokman)은 생산의 한 측면인 부품 절단에 대해 이렇게 설명합니다.
“우리는 모든 것을 산소 토치로 잘랐습니다. 자재를 가져와 길이를 측정하고, 절단할 곳은 정한 다음, 형판을 놓은 뒤 윤곽선을 그리고, 마침내 절단한 다음에는 괜찮아 보일 때까지 갈아냈죠.”
Gunderson의 관리자들은 매뉴얼 방식이 문제가 있는 것은 아니지만 그리 효율적이지는 않다는 사실을 알고 있었습니다. 시설 자동화를 계획한 Gunderson Marine은 작업자들에 대한 우려와 갈수록 부족해지는 숙련된 기술자로 인해 좀 더 많은 자동화 옵션을 찾고 있습니다.
스토크먼은 “이 모든 작업을 수동으로 수행하는 것은 사람의 신체에 그리 적합하지 않습니다. 작업대 너머로 몸을 기대기도 하고 구부리기도 해야 합니다. 우리는 인체 공학적으로 이를 개선할 수 있다는 사실을 알고 있습니다. 하지만 인력의 필요를 줄여야 한다는 사실도 깨달았습니다. 숙련된 기술자를 구하는 것은 훨씬 어렵고 일을 배우려는 사람조차도 구하기 힘든 게 현실이기 때문입니다.”
다시 말해, Gunderson 팀은 지난 90년간 해온 방법으로는 경쟁력을 갖출 수 없다는 사실을 깨달은 것입니다.
그들은 3개의 대형 CNC 테이블을 작업에 추가하여 현대화 노력을 시작했습니다. Hypertherm HyPerformance 플라즈마가 장착된 이 테이블은 평판 절단 작업의 속도를 비약적으로 가속화함으로써 Gunderson에 큰 도움을 주었습니다. 게다가 이 회사는 그들의 산소 핸드 토치 중 일부를 Hypertherm Powermax 에어 플라즈마 시스템으로 교체했습니다. 3개의 대형 Hypertherm HyPerformance 플라즈마 테이블은 Gunderson의 판재 절단 작업 가속화를 도왔습니다.
이 회사의 현대화 노력은 거기서 그치지 않았습니다. 3개의 CNC 플라즈마 테이블 덕분에 평판 절단 작업을 훨씬 더 효율적으로 수행할 수 있게 되었지만 다른 작업들은 여전히 수작업이 대부분이었습니다. 궁극적으로 Gunderson은 판재뿐만 아니라 바지선을 만드는 데 필요한 3차원 도형을 절단할 수 있는 솔루션을 찾고자 했습니다.
“우리는 상당수의 장비들을 알아봤고, 4~5개의 장비로 좁혀나가다가 결국 900을 선택했습니다.” “900의 장점은 로봇이 강철 구조물의 4면 모두를 절단할 수 있다는 것이었습니다.” 스토크먼은 설명했습니다.
900은 캐나다의 lnovatech Engineering에서 제작한 SteelPRO 900을 말합니다. 이 장비는 로봇 빔라인 절단과 일반적인 평판 절단 기능 모두를 제공하는 이중용도 시스템입니다. Hypertherm HyPerformance 플라즈마 토치를 장착한 Fanuc 로봇은 빔, 튜빙은 물론 벌브 플랫(한쪽 면에 짧은 테이퍼드 립이 있는 긴 강철판), 채널, 앵글 등의 구조적 모양까지 절단할 수 있으며, 테이블은 평판, 밑판, 보강용 판을 절단할 수 있습니다.
스토크먼은 이 마지막 부분이 큰 장점이라고 했습니다. “플레이트 테이블이 있기 때문에 문제가 생기면 2D 부분을 자체적으로 절단할 수 있습니다. 급하게 필요한 파트가 있을 때나 엔지니어링적인 변경 사항이 있을 때도 장비에 넣고 잘라내면 작업이 지체되지 않습니다. 굉장히 다재다능한 장비입니다. 생각할 수 있는 거의 모든 모양으로 절단이 가능합니다.”
연강의 경우, 잘라내는 두께는 ¼에서 1인치까지입니다. 절단 후에는 Hypertherm의 SureCut 기술을 통해 Y자 경사 및 볼트 구멍이 빠르게 만들어집니다. “절단 품질은 아주 좋습니다. 훌륭합니다. 우리가 지켜야 하는 모든 기준을 뛰어넘는 수준입니다. 구멍도 매끄럽고 둥글게 잘리며 모든 것이 동일합니다.”
6명이 필요했던 작업에 이제는 1명 밖에 필요하지 않습니다. Gunderson이 3교대로 운영되기 때문입니다. 절약 효과는 빠르게 증가했습니다. 이를 통해 Gunderson은 용접과 같은 후속작업에 더 많은 인력을 투입하여 전체적인 생산시간을 단축할 수 있습니다. 스토크먼은 회사가 lnovatech 장비에 4,000 직선 피트 이상의 자재를 투입하는 날도 있다고 추산합니다.
이렇게 빠른 작업 능력은 lnovatech에 사용된 소프트웨어의 도움이 큽니다. 대부분은 lnovatech에서 Gunderson의 선박 설계 프로그램과 함께 사용할 수 있도록 개발된 소프트웨어처럼 맞춤형으로 제작된 것입니다. 스토크먼의 말에 따르면 다른 벤더들이 요구했던 금액의 극히 일부로 제작된 이 소프트웨어를 통해 Gunderson은 손쉽게 파일들을 불러올 수 있다고 합니다.
“네스팅 소프트웨어로 직접 불러오기가 가능하고 잠시 후 네스트들이 준비가 되면 자재를 절단할 수 있습니다.”
또한, lnovatech는 Gunderson의 전문 절단 목록 작업을 위해 네스팅 소프트웨어(Hypertherm의 ProNest)에 코드를 추가했습니다. 이 소프트웨어만으로 일주일에 24시간의 사무 처리 시간을 절약할 수 있으며 인적 오류의 가능성도 제거할 수 있습니다.
이러한 모든 자동화에도 불구하고 장비 운용자는 운용실에서 전력 레벨, 속도, 가스 설정, 아크 전압, 절단 높이, 피어싱 높이를 변경할 수 있습니다. lnovatech의 미켈 클레멘트(Miquel Clement)는 'Hypertherm 장치는 매우 잘 구축되어 있으므로 전원 설정을 즉시 변경할 수 있다'고 말합니다. 시스템 운용도 매우 간편합니다. “교육 시간이 짧습니다. 지금까지 약 20명을 교육했습니다. 불과 2시간이면 혼자서도 운용을 할 수 있습니다. 그 정도로 간단합니다.” 스토크먼은 설명합니다.
Gunderson에서는 아직도 벌크 헤드 다듬기에 산소 연료 토치를 사용하고 작은 부분은 절단기를 사용하여 절단하지만 대부분의 절단 작업은 모두 플라즈마로 수행됩니다. 여기에는 모든 종류의 선박을 만들 때 매우 중요한 보강재도 포함됩니다.
“새로운 시스템은 우리가 보강재를 절단하고 바지선에 붙이는 방식에 대해 재검토해볼 수 있도록 해주었습니다. 우리는 보강재를 절단하는 방법, 우리의 디자인을 바꿀 수 있었습니다. 새로운 방법은 용접면은 늘리고 용접 치수 줄여주었습니다. 우리는 용접 공정의 속도를 높일 수 있었습니다. 3회 통과 용접 대신 이제 단일 통과 용접을 할 수 있게 되었습니다.”
스토크먼의 말에 따르면 더 길고 더 얇은 용접은 더 튼튼한 접합부를 만듭니다.
Gunderson이 내린 지속적인 혁신에 대한 결정은 지난 100년간 회사를 잘 이끌어왔으며, 2세기를 맞이함에 있어서도 Gunderson Marine의 입지는 유리하다고 볼 수 있습니다.
플라즈마 기술이 결합된 로봇 토치 절단은 회사의 효율성을 그 어느 때보다 향상시켰습니다. Gunderson Marine은 더 많은, 더 나은 바지선을 건조하고 있으며, 윌라멧 강은 앞으로도 분주할 것입니다.