레이저와 플라즈마 절단 중에서 선택하는 방법: 차트
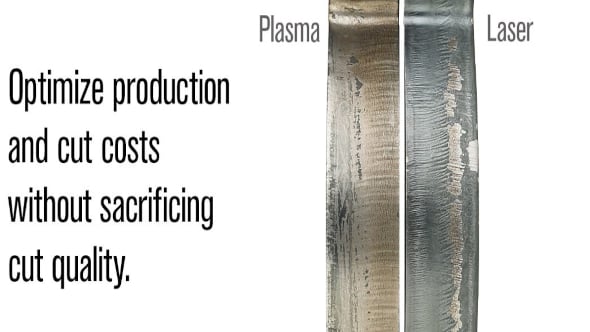
플라즈마 커팅 시스템과 레이저 절단 시스템 중에서 하나를 선택할 때는 여러 가지를 고려해야 합니다. 이 블로그에서 두 가지 기술에 대해 자세히 살펴보았지만, 오늘은 7가지 주요 차별화 요소 즉, 절단 품질, 다용도성, 비용, 안전, 시간 절약/자동화, 내구성, 그리고 각 기술이 이상적인 상황에 초점을 맞추겠습니다. 플라즈마 절단과 레이저 절단은 저마다 장점이 있기 때문에 절단 니즈, 특히 절단할 소재의 유형, 소재의 두께, 절단 복잡성, 절단 품질에 대한 고객 요구 사항에 따라 비즈니스에 적합한 절단 방법을 선택해야 합니다.
플라즈마 절단이란?
플라즈마 절단은 고속 플라즈마 분사를 사용하여 강철, 알루미늄 및 기타 금속과 같은 전기 전도성 소재를 절단하는 열 절단 프로세스입니다. 속도와 정확성 때문에 제조, 건설, 자동차 분야의 금속 가공에 일반적으로 사용됩니다.
레이저 절단이란?
섬유 레이저 절단은 집속된 광선을 사용하여 다양한 소재를 절단하거나, 새기거나, 마킹하는 고정밀 다목적 기술입니다. 금속 및 플라스틱 절단부터 목재 또는 세라믹의 복잡한 디자인 에칭까지 산업, 상업, 취미 생활 환경에서 널리 사용됩니다.
절단 품질
플라즈마와 레이저 모두 절단 품질이 우수하며, 섬유는 얇은 금속에서 결과가 더 좋고, 플라즈마는 두꺼운 금속에서 더 깔끔하게 절단합니다. 레이저 절단 품질이 일반적으로 더 좋지만, 플라즈마 절단 품질은 대부분의 고객 요구 사항을 초과합니다. 그래서 레이저 절단의 품질이 더 높더라도 사용자나 고객에게 실질적인 이점은 없을 수도 있습니다.
플라즈마
-
ISO 9013 범위 2~4의 절단 품질
-
섬유 레이저 절단 품질에 필적하는 절단 품질로 대부분의 고객 요구 사항을 능가합니다
-
용접 준비에 최소한의 이차 작업
-
매끄럽고 직선인 절단면
-
플라즈마로 최소한의 산화물 층과 드로스 생성
레이저
-
ISO 9013 범위 1~2의 절단 품질
-
얇은 커프 크기와 낮은 각도가 장점
-
높은 정밀도 및 정확성
-
얇은 금속에서 우수한 절단 품질
-
두께가 12~16mm 이상 증가하면 거친 표면 마감과 더 많은 드로스 발생
절단 다용도성
플라즈마 절단과 레이저 절단은 모두 복잡한 모양을 자르고, 조각하고, 마킹할 수 있는 매우 다재다능한 기능입니다. 레이저는 더 많은 소재를 절단할 수 있지만 더 깨끗한 소재가 필요하며, 때로는 세척이나 프리컷 기화 과정이 필요해 생산성이 떨어집니다. 플라즈마는 불완전하고 깨끗하지 않은 금속을 절단할 수 있지만 플라스틱은 절단할 수 없습니다. 따라서 어느 것을 선택할지는 비즈니스 니즈에 따라 달라집니다.
플라즈마
-
스탠드오프 거리가 길어지면 절단 작업에 대한 간섭이 감소
-
직선, 베벨, 구멍, 복잡한 모양을 절단
-
스테인리스 스틸, 연강, 알루미늄, 구리, 황동 및 기타 금속을 절단
-
불완전하고 페인트가 칠해져 있거나 녹이 슬었거나 코팅된 소재를 절단
레이저
-
절단, 각인, 마킹 가능
-
복잡하고 정교한 모양 절단 가능
-
강철, 알루미늄, 구리, 플라스틱, 복합재를 절단
-
특수 등급 소재, 수작업 세척 또는 프리컷 기화 과정이 필요하여
-
생산성 감소
절단 비용
레이저 절단 시스템은 일반적으로 플라즈마 절단 시스템보다 2~5배 더 비싸지만, 레이저 시스템은 소모품 사용량이 적고 소재 낭비가 최소화됩니다. 시간이 지남에 따라 어느 시스템이 더 비싼 시스템인지는 사용되는 방법에 따라 달라집니다. 플라즈마는 일반적으로 12mm보다 두꺼운 소재를 절단할 때 운용 비용이 낮고, 레이저는 더 얇은 소재를 절단할 때 운용 비용이 낮습니다.
플라즈마
-
종종 2년 이하의 ROI
-
더욱 저렴한 소모품
-
최소한의 후속 작업
-
일반적으로, 12mm보다 두꺼운 소재를 절단할 때 섬유 레이저보다 운용 비용 낮음
레이저
-
절단 시스템은 플라즈마 비용의 2~5배
-
더 적은 소모품 사용
-
소재 폐기물 최소화
-
일반적으로, 12mm보다 얇은 소재를 절단할 때 플라즈마보다 운용 비용 낮음
-
두꺼운 소재를 절단할 때 높은 가스 및 전기 비용
안전
플라즈마 절단은 레이저 절단보다 안전합니다. 플라즈마 절단은 플라즈마 아크를 장시간 볼 때만 보안경이 필요합니다. 레이저 절단에는 안전 문제를 위해 인클로저와 소재 취급이 필요합니다.
시간 절약 및 자동화
플라즈마
-
대용량 생산 및 절단 속도에 탁월한 선택
-
CNC 시스템과 쉽게 통합하여 자동 절단뿐만 아니라 복잡한 모양과 패턴 절단까지도 가능
-
대량 생산 또는 맞춤형 구성요소에 적합
-
로봇 절단에 적합
레이저
-
두꺼운 철판에서는 파트를 스켈리톤에서 제거하기 어려워 망치로 두드려야 함
-
자동화되고 반복 가능한 대량 생산을 위해 CNC 시스템과 통합 가능
-
얇은 소재를 더 빨리 절단
절단 장비 내구성
플라즈마 시스템에는 간단한 내부 유지 관리가 필요합니다. 레이저 시스템은 더러운 환경에 더 민감하며 주기적으로 청소와 고도의 유지 관리가 필요하므로 공식 서비스 센터에 의뢰해야 할 수도 있습니다.
플라즈마와 레이저의 가장 이상적인 적용 분야
플라즈마 절단 시스템은 12mm~16mm 이상의 두꺼운 소재와 더 빠른 절단 속도가 필요한 작업에 이상적입니다. 레이저 절단 시스템은 높은 정밀도, 우수한 모서리 품질, 복잡한 절단이 필요한 12mm~16mm보다 얇은 소재를 절단하는 데 이상적입니다.
결론: 최선의 선택은 적용 분야에 따라 달라집니다.
플라즈마 절단과 섬유 레이저 절단은 각각 장점이 있으므로 시스템의 용도에 따라 적합한 것을 선택해야 합니다. 플라즈마는 초기 투자 비용이 적게 들고, 유지하기가 더 쉬우며, 사용하기가 더 안전합니다. 두꺼운 금속에서는 레이저보다 성능이 뛰어나고 얇은 금속에서는 레이저와 대등합니다.
문제는 절단하는 금속의 두께, 절단이 얼마나 정밀해야 하는지, 더 높은 수준의 정밀도를 위해 얼마를 지불할 의향이 있는지, 그리고 고객이 요구하는지 여부에 달려 있습니다.
아래에서 이 비교 차트를 확인하십시오.
레이저와 플라즈마 절단의 자세한 비교는 "플라즈마 절단과 레이저 절단 비교: 가이드”를 참조하십시오.