어떻게 생산성을 향상시킬 수 있을까요?
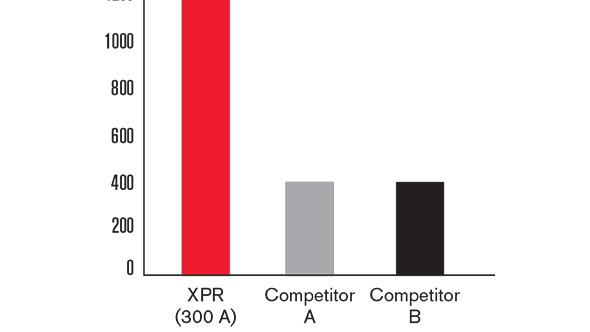
산업용 절단의 경우 생산성은 3가지 즉, 절단 속도, 절단 품질, 시스템 가동 시간으로 결정됩니다. Hypertherm에서 새로 출시한 XPR300은 빠르게 절단하고, 2차 작업을 줄이거나 아예 하지 않도록 하고, “스마트” 기술과 시간 절약 단계를 통해 시스템 가동 시간을 향상시키는 시스템을 개발하여 이러한 3가지 생산성 요소를 개선하였습니다.
절단 속도
XPR300은 300암페어와 63킬로와트의 전원을 공급하기 때문에 260암페어를 공급하는 이전 시스템보다 빠르게 절단합니다. 정확한 절단 속도는 절단하는 소재의 두께에 따라 다르지만 일반적으로 15~40mm 두께의 소재인 경우 10~20%, 50mm 두께의 소재인 경우 38%, 60mm 두께의 소재인 경우 거의 50% 정도를 각각 더 빠르게 절단할 수 있습니다.
Thickness | XPR300 | HPR260XD | HPR400XD |
XPR300 |
HPR400XD versus XPR300 % |
|
15 mm | 3440 | 3130 | 3950 | 10% | 15% | |
20 mm | 2550 | 2170 | 2805 | 18% | 10% | |
25 mm | 1950 | 1685 | 2210 | 16% | 13% | |
30 mm | 1530 | 1290 | 1790 | 19% | 17% | |
40 mm | 940 | 790 | 1160 | 19% | 23% | |
50 mm | 560 | 405 | 795 | 38% | 42% | |
60 mm | 385 | 258 | 580 | 49% | 51% | |
70 mm | 250 | N/A | 380 | N/A | 52% |
절단 속도 (mm/min)
XPR은 HPR260XD보다 더 빠르게 절단할 뿐만 아니라 효율성도 더 뛰어납니다. 아래의 도표에 나와 있듯이 XPR300은 200암페어로 설정된 HPR260XD의 절단 속도를 내는 데 170암페어만 있으면 됩니다. 더 빠르게 절단하지만 작업에 필요한 에너지는 더 적습니다.
절단 품질
절단 품질의 경우 XPR300은 X-Definition이라는 완전히 새로운 수준의 품질을 자랑합니다. 이 절단 등급은 열 절단 부분의 절단 품질을 규정하는 ISO 9013 국제 기준으로 측정된 것과 같이 절단 품질을 높여줍니다. 이 기준은 1~5 등급이 있으며 1이 가장 좋은 절단 품질입니다. 새로 출시된 XPR은 소모품의 거의 전체 수명주기 동안 ISO 3 등급의 절단 품질을 제공합니다. 이에 반해, Hypertherm의 HPRXD 시스템은 아래와 같이 4 등급의 절단 품질을 제공합니다.
위의 도표는 12mm 연강을 절단할 때의 결과이며, 연구소 테스트는 더 낮은 전류에서 더 얇은 연강을 절단할 때의 ISO 2 등급 절단 품질입니다. 향상된 절단 품질과 더불어, 고려할 다른 요소는 절단의 일관성입니다. 도표에 나와 있듯이, 20초 절단 작업을 수백 번 수행한 연구소 테스트에서 절단 품질이 매우 일정했습니다. 새 소모품으로 절단한 부분과 1,000번 이상 사용한 소모품으로 절단한 부분이 거의 동일합니다.
절단 품질의 획기적인 향상은 스테인리스강과 알루미늄뿐만 아니라 연강 절단에도 해당됩니다. 이것은 특허를 신청한 몇 가지 신기술 덕분입니다. 이러한 프로세스 중 하나인 Vented Water Injection은 질소 플라즈마 가스를 물 쉴드와 결합하여 플라즈마 아크의 정렬과 포커스를 향상시켜 줍니다. Vent-to-Shield라는 두 번째 프로세스는 배기된 플라즈마 가스에서 질소를 회수하여 쉴드 가스와 혼합합니다. 이 두 가지 기술 덕분에 HPR과 비교했을 때 모가 나지 않고 더 깔끔하게 절단하며 표면 마감도 더 좋습니다. XPR은 구멍에 사용하는 플라즈마 아크와 새로운 아크 분할 프로토콜을 안정화해 주는 최신 아크 안정성 프로세스도 사용합니다. 이 프로토콜은 업계를 선도하는 Hypertherm의 True Hole 프로세스를 능가합니다.
시스템 가동 시간
XPR에서 적용된 기술이 많지만 실제로는 시스템이 덜 복잡합니다. 전원공급장치의 센서는 세밀한 진단 코드와 획기적으로 향상된 시스템 모니터링 정보를 제공합니다. 덕분에 문제 해결 시간이 줄어들며, 사전 예방적 데이터를 제공하여 시스템 최적화를 전반적으로 개선해 줍니다.
또한, 이 시스템은 콘솔과 연결부가 줄어들어서, 작업자들이 설치 시간은 줄이고 절단 작업에 더 많은 시간을 사용할 수 있습니다. 여기서 도움이 되는 기능에는 작업자가 도구를 사용하지 않고 토치를 토치 콘솔에 장착할 수 있는 EasyConnect™ 연결 장치가 있습니다. 특허 출원 중인 QuickLock™ 전극은 간편한 ¼ 회전 잠금 기능으로 작업 준비 시간을 단축해 주며, 새로운 설계 덕분에 작업자는 한 손으로 빠르게 토치를 교체할 수 있습니다. 모든 콘솔에 고급 자동 가스 기능이 탑재되어 작업자가 CNC에서 직접 절단 작업을 선택하여 수행할 수 있으며, 전원공급장치의 Wi-Fi를 통해 멀리서 시스템(또는 여러 시스템)을 모니터링할 수 있습니다.
전반적인 운영 비용뿐만 아니라 시스템 가동 시간도 소모품 수명 개선으로 향상됩니다. 특허 출원 중인 Cool Nozzle™ 기능은 노즐을 직접 액체 냉각하여 소모품의 수명을 40% 향상시켜 줍니다. 특허 출원 중인 PowerPierce® 기술은 쉴드와 거의 동일한 역할을 수행합니다. 쉴드를 액체 냉각하여 피어싱 작업 중 금속이 녹는 것을 실질적으로 예방하여 쉴드가 손상되지 않습니다. 토치 콘센트 밸브는 가스 흐름을 빠르고 정교하게 제어하여 산소 프로세스 수명을 획기적으로 늘려주고 램프다운 프로세스를 빠르게 진행합니다. 아래와 같이 대부분의 경우 이러한 램프다운 제거 덕분에 소모품 수명이 다른 시스템보다 거의 3배나 늘어납니다. 소모품 교체에 시간이 적게 든다는 것은 절단 시간 및 다른 중요한 작업을 수행하는 데 더 많은 시간을 사용할 수 있다는 의미입니다.
네, 바로 이것입니다. 빠른 속도, 향상된 절단 품질, 뛰어난 시스템 가동 시간 덕분에 XPR300의 생산성이 개선되었습니다.
어떻게 생산성을 향상시킬 수 있을까요?