川岸の現場で採用された自動化システム
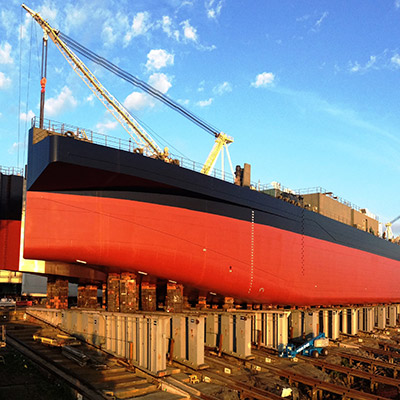
オレゴン州のウィラメット川にある、米国北西部最大の造船所のひとつといわれるこの現場は、慌ただしい雰囲気です。
ポートランドのガンダーソン・マリーン社のチームはフル回転で作業しています。作業員らがプラン図を覗きこみ、トラックがドックに乗りつけ、フォークリフトは大型の鋼板を積み上げたり下ろしたりしています。
作業は24時間シフトで休みなく進められます。チェット・ガンダーソン氏は1940年代初頭、11エーカーのこのウォーターフロントの土地を購入して20年来の事業を拡張することに決めました。 それ以来、この風景は変わっていません。チェットが造船所を構想した時、折しも米国は第二次世界大戦に参戦間近で、彼にとってこれ以上の好機はありえませんでした。間もなく、米国海軍向けに砲艦、救命艇、上陸用舟艇の建造を受注し、現場は活況を呈しました。
現在はグリーンブライアー・カンパニーズ社が所有するガンダーソン・マリーン社は、それ以来、数千もの船舶を建造してきました。これらの船舶には、海洋に関するあらゆる種類の艀、デッキ、ダブルハルタンカー、鉄道車両、ダンプ、重工業、その他数多くのタイプのものが含まれます。
ガンダーソン社の100年近くにわたる歴史の大部分において、それら船舶、そしてかつてのホイールハブやトレーラーは、ほぼ手作業によって造られてきました。造船所の生産調整担当者であるウォルト・ストークマン氏は、生産工程のひとつ、つまり部品の切断について、このように説明しています。
「私たちはどんなものでも手作業で、主にガス溶断トーチを使用して切断したものでした。材料を準備し、その長さを測り、切断位置を確認し、テンプレートを置き、印をつけ、切断し、さらに、ある程度見栄えをよくするために切り口を研ぎます。」
ガンダーソン社のマネージャーらは、この手作業による切断方法は機能はしているものの、あまり効率的ではないことを知っていました。この施設を近代化するための取り組みは、作業員への懸念と熟練者不足の深刻化とあいまって、ガンダーソン・マリーン社に自動化の導入へと目を向けさせることになりました。
ストークマン氏は説明します。「これらすべてを手作業で行うことは、体にも良いものといえません。テーブルの上に身を乗り出し、前かがみになって、腰を曲げなければなりません。人間工学に基づいた改善策を取り入れることが可能なことは分かっていました。また、人員数を削減する必要があることも認識していました。条件に見合った人材を雇うことが難しいのはなおさら、この仕事をするための訓練を受けたいと思っている人たちを見つけることでさえ難しいのです。」
言い換えれば、ガンダーソン社のチームは、これまでの90年間と同じようにビジネスを続けて競争力を維持することができないことが分かったのです。
同社は、近代化の取り組みとして、3 台の大型CNCテーブルをオペレーションに導入することから始めました。Hypertherm HyPerformanceプラズマを装備したこのテーブルにより、ガンダーソン社は平板切断のスピードを大幅に向上させることが可能になり、大きな助けとなりました。さらに、同社はガス溶断ハンドトーチの一部をHypertherm Powermaxエアプラズマシステムに入れ替えました。ガンダーソン社は、3つの大型Hypertherm HyPerformanceプラズマテーブルで、大規模施設でのプレート切断のスピードアップを実現しました。
同社の近代化の取り組みはこれで終わりではありませんでした。3つのCNCプラズマ切断テーブルは平板の切断の効率性を大幅に向上させましたが、会社は依然として多くの手作業工程があることに気付きました。理想的には、ガンダーソン社はプレートに加えて、バージを建造するときに必要となる多くの3次元形状を切断できるソリューションを見つけたいと考えていました。
ストークマン氏は次のように述べています。「私たちはかなりの数の機械を調査し、最終的に900を採用するまでに4 、5機にまで絞り込みました。」「900が選ばれた理由は、ロボットが構造物の4つの金属側面すべてを切断することができるということです。これは便利です。」
900とは、カナダのlnovatechエンジニアリングが製造したSteelPRO 900のことです。これは、ロボットビームライン切断と標準プレート切断の両方が可能な、2つの機能を備えたシステムです。切断テーブルでは平板、ベースプレート、スチフナープレートを切断する一方、Hypertherm HyPerformanceプラズマトーチを装備するFanucロボットは、球平形鋼(片側に短いテーパの付いた長い平らな金属)、チャンネル、角度などの構造上の形状とともに、ビームとチューブの周りをすべて切断できます。
ストークマン氏はこれを大きなメリットであると語っています。「それはプレート切断テーブルを備えているので、必要な時にはプレートマシン上で2D部品をカットすることができます。急ぎでパーツが必要な場合は、すぐにそれをマシンに置くことができます。また、エンジニアリングの変更があった場合、中断せずに素早く部品を切断することができます。たいへん汎用性に優れています。どんな形状でも切断することが可能です。」
軟鋼から切り取った形状は、厚さが1/4〜1インチです。最初の切断の後、HyperthermのSureCut技術を使用して、Y字型開先とボルト用の穴を素早く作ることができます。「切断品質は、非常に優れています。私たちが求めるすべての基準を上回るものです。孔はきれいで丸く、すべて滑らかです。」
ガンダーソン社では3シフト制のため、この作業に以前は 6人雇っていましたが、現在は1人で済みます。この節約は急速に効果をあげました。これにより、ガンダーソン社はより多くの人を、溶接などの終了段階の作業にまわすことができ、製造のスピードアップに役立っています。シックマン氏は、会社がlnovatechのマシンで4,000リニアフィート以上もの材料を取り扱う日があると推測しています。
これほど迅速に作業できるのは、大部分がlnovatechが使用するソフトウェアのおかげです。その多くはカスタム設計で、ガンダーソン社の船舶設計プログラムで動作するように作成されています。シックマン氏によると、他の業者のソフトウェア価格に比べてわずかな費用で作られたこのソフトウェアによって、ガンダーソン社はファイルを簡単にインポートできるようになりました。
「ネスティングソフトウェアに直接インポートすることができるため、その後すぐにすべてのネストが準備でき、材料を切断できます。」
またlnovatechは、ガンダーソン社の特殊な切断リストを扱うためのネスティングソフトウェア(HyperthermのProNest)にコードを追加しました。このソフトウェアだけでも、1週間あたり24時間の事務処理時間を節約でき、人的ミスの可能性も排除できます。
これらの自動化にもかかわらず、マシンのオペレーターは、オペレータステーションで電力レベル、速度、ガス設定、アーク電圧、切断高さ、ピアス高さを変更することが可能です。lnovatechのミケル・クレメント氏は次のように述べています。「Hypertherm のユニットは非常にうまく設計されており、即座に電源設定を変更できます。」システムは操作も簡単です。「トレーニングは短時間で済みます。これまで20人を訓練しました。たった2時間後に、彼らは自分で作業できるようになりました。とてもシンプルです。」とシックマン氏は語っています。
ガンダーソン社は、隔壁のトリミングや小規模な仕事のためのチョップソーなど、いくつかの仕事ではまだガス溶断を使用していますが、大部分がプラズマで行っています。これには、あらゆる種類の海洋船舶を建造する際に非常に重要なステテフナーが含まれます。
「この新しいシステムにより、ステテフナーを切断して艀に接続する方法を再検討することができました。デザインの変更、ステテフナーを切断する方法を変更できたのです。新しい方法では溶接面を増やすことができましたが、溶接サイズは小さくなりました。溶接プロセスをスピードアップすることができたのです。3パス溶接の代わりに、ワンパス溶接を行えるようになりました。
溶接は長くなりますが、同時に薄くなり、実際にはより強固な接続が得られるとストークマン氏は述べています。
ガンダーソンの継続的な技術革新の決断は、過去100年にわたり同社を支えてきました。同社が次の世紀の事業を開始するにあたり、ガンダーソン・マリーン社は有利な立場にあります。
自動化されたプラズマ技術によるロボット切断は、同社がこれまで以上に効率的であることを意味します。同社では、より多くの、よりよい艀を建設しており、ウィラメット川での操業が今後も続くことが保証されています。