Powermax SYNC® で作業がどう変わるのか
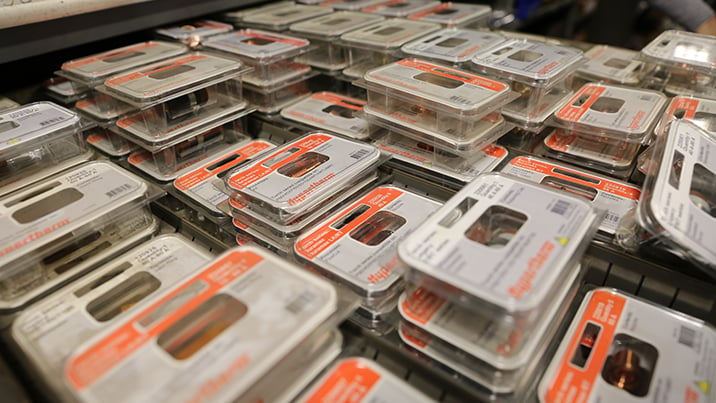
先日、カートリッジベースの消耗部品にはエンドユーザー側から見たメリットがたくさんあり、カートリッジを使用すると交換がより簡単、より安全で、部品管理がしやすいものになることをご説明しました。
しかし、「革新的な消耗部品」は、新しい Powermax SYNC® シリーズの重要な要素の一つにすぎません。私たちがこれからの Powermax プラズマについて考え始めたときに目指したのは、システムを根本から見直してお客様が一様に抱えている問題点に対処することです。実際にお客様と話をしてみると、次の 3 つの現状が明らかになってきました。
-
企業はその大小に関わらず、プラズマ切断作業の熟練者はもちろんのこと、作業者そのものを見つけるのに苦労している。
-
企業はコストを減らして生産性を向上させなければならず、大きなプレッシャーにさらされている。
-
企業は、進行中の作業をモニタリングする術を必要としており、それによって問題をすばやく特定し、対処をすることで、是正に高額な費用を要するまでに事態が深刻化するのを防ごうとしている。
なお、Hypertherm の新しい Powermax SYNC® シリーズは、この 3 つの現状すべてに対応するよう設計されています。
課題 1:熟練者を見つけるのがほぼ不可能。
解決策:トレーニングの必要のない、使いやすいプラズマカッターを作る。
以前のブログでもお話ししましたが、Powermax SYNC® は驚くほど直感的で使いやすいのが特徴です。Powermax SYNC® のシステムに 5 つの個別の消耗部品は付いておらず、必要なのは 10 秒足らずで取り付けられる組み込み式一体型カートリッジだけです。そのため、時間を割いて新しい従業員に正しい消耗部品の見分け方や、正しい順序での組み立て方、トーチへの取り付け方を教える必要はありません。
Hypertherm の新しい組み込み式一体型カートリッジは色分けがされているため、オペレーターは実行中の作業用のカートリッジをさっと手に取ることができる。色は全 4 種:ハンド切断用は黄色、マシン切断用は灰色、ガウジング用は緑、さらにフラッシュ切断やリーチの長い切断などの特殊プロセスの場合は黒を使用する。
カートリッジ消耗部品プラットフォームのもう一つの利点は、摩耗速度に関するものです。従来の 5 ピース構成の部品は、同じ速さでは摩耗しません。一番早いのが電極とノズルで、リテイニングキャップは摩耗が最も遅く、したがって雇用者は、消耗部品を点検して摩耗したものを交換する方法を新しいオペレーターに教えなければならず、トレーニングの時間が必要になり大変です。その点 Hypertherm の新しいカートリッジ消耗部品は、コンポーネントが一定の速度で摩耗するよう設計されており、トレーニングや、無駄な廃棄、ダウンタイムがさらに抑えられます。
また、カートリッジは RFID チップ搭載で、チップはトーチ / 電源装置と通信して、システムの設定をカートリッジに確実に合わせる働きをします。たとえば 65 アンペアの切断カートリッジを取り付けると、システムのアンペア数が 65 アンペアになり、自動的に空気圧が設定されて、切断モードに入ります。そのためトレーニングが少なくて済むだけでなく、オペレーターのエラーもなくなります。
オペレーターにとっては、間違った部品を選んでしまわないか、正しい順序に配置できるか、適切にトーチに取り付けられるかといった心配は不要です。事業主も、新しい従業員のためのトレーニング(消耗部品とは何か、正しい部品の見分け方、それらを適切に並べてトーチに取り付ける方法などについて)に多くの時間を費やす必要がなくなります。
課題 2:生産性をあげるよりも、コストが膨らんでいくスピードの方が速い。
解決策:より効率的なプラズマ切断機を作り、オペレーターがより短い時間でより多くの作業を完了できるようにする。
新しい人材のトレーニングに費やす時間が減れば、もちろん生産性の向上につながりますが、Powermax SYNC® はさらに他の方法でも生産性を高めます。
その一つは、カートリッジ消耗部品はハンド切断で最大 2 倍寿命が長く、マシントーチを使用すると切断品質が向上するというものです。これは、消耗部品の交換やできたパーツの手直しにかかる時間が短くなることを意味します。また、新製品では状態を把握しなければならない部品が 5 つから 1 つになったため、注文と在庫管理が格段に簡素化されます。
従来のプラズマ消耗部品の管理は高くつくうえややこしく、結果的に在庫のコストが増加してオペレーターのミスが増える。
自動設定プロセスやカラーコード式のカートリッジは、パーツの切断不良ややり直しにつながるエラーを未然に防ぐという点でも有用です。オペレーターがミスを起こさないようにすれば、生産性はすでに大幅に向上しているわけですから、それ以上何もすることはありません。つまり、Powermax SYNC® は、付加価値の得られない作業を(「排除」まではいかずとも)大幅に減らすことで生産性を高めるのです。
Powermax SYNC® の利点はまだあります。というのも、Powermax SYNC® のトーチにはコントロール機能が内蔵されており、わざわざ電源装置まで戻らなくてもアンペア数を調整したり、トーチのオンとオフを切り替えたりできるようになっています。そしてこれもまた「付加価値の得られない時間の排除」を可能にするもので、たとえば、はしごの上で作業をしている場合や、作業中機械を作業台の下に置いている場合は、その場でシステムを調整して時間を節約することができます。
課題 3:問題がみるみるうちに拡大し、お金が無駄になる。
解決策:便利なデータが得られるプラズマ切断機を作り、オペレーターが問題をいち早く発見できるようにする。
先にお話ししましたが、Powermax SYNC® カートリッジには RFID チップが組み込まれており、チップはトーチ / 電源装置と通信して、システムの設定が正しいことを自動的に確認します。ところが、このチップには「使用データの収集」というもう一つの役割があるのです。
Powermax SYNC® システムでは、使用中のアークオン時間、アークトランスファー率、空気圧などの情報を収集します。こうしたカートリッジの使用データは、特殊なカートリッジリーダーとアプリを使ってダッシュボードにインポートでき、使用のパターンや傾向に関する管理・比較をしたり、洞察を加えたりすることができます。そしてこのデータは、生じている問題を早いうちに特定して消耗部品の寿命に影響が及ぶのを防ぐうえで役立ちます。たとえば、アークトランスファー率が通常 85% であることがわかっていて、それが低下したり、突然スタート数が少なくなったりすれば、何かがおかしいということになるわけです。
これについて、私たちは実地試用で何度も事例を目の当たりにしました。たとえばこんな話があります。あるお客様が、夜のカートリッジの寿命が短いことに気付いたのです。データを分析したところ、夜間の外気温が低く、システムへのエアフローに影響が出ていることがわかりました。そこで取った対策が「エアフローをわずかに増やす」というもの。たったそれだけでカートリッジの寿命は正常に戻りました。
このお客様はまた、オペレーターのなかにアークをトランスファーせずにトーチを点火している人が複数いることにも気がつきました。そのため、オペレーターを指導し、消耗部品の寿命問題を改善しました。Powermax SYNC® が登場するまで、こうした洞察による状況判断はできなかったのです。
以上をまとめると、Powermax SYNC® は、使いやすさと、無駄を減らすこと、スマートなデータ収集を通じて、企業の一般的課題に対処するのを助けます。だからこそ私たちは、長い歳月をかけて開発したこの新しいシリーズと消耗部品プラットフォームが付加価値をもたらし、作業そのものを変えるのだと確信しているのです。