プラズマ切断とレーザー切断の比較ガイド
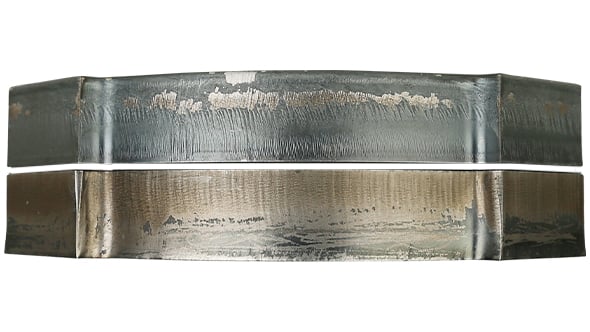
プラズマ切断機またはファイバーレーザー切断機の購入を検討する際、どちらの切断技術が生産環境に最適でかを判断する要素がいくつかあります。これには設備投資、金属の厚さ、切断品質、速度などが含まれます。さらに、材質の表面、機器のメンテナンス、運用コストも考慮する必要があります。作業に応じて、プラズマ切断とファイバーレーザー切断にはそれぞれ利点があります。
まず、切断技術の違いを理解しましょう。
プラズマ切断とは?
プラズマ切断は、切断材料を溶かして吹き飛ばすことができるプラズマとして知られる高熱のイオン化ガスを生成することにより、鋼鉄、アルミ、その他の導電性金属を切断します。通常、高速プラズマ電気アークをワークピースに向けるプラズマトーチを使用して切断され、正確かつ効率的な金属切断が可能になります。プラズマ切断は、その速度と精度により、製造、建設、自動車業界で一般的に使用されている金属加工プロセスです。プラズマ切断は、ハンドトーチを使用するか、自動切断用のテーブルを備えたコンピューター数値制御 (CNC) を使用して実行できます。
プラズマ切断の種類
プラズマ切断の各方法にはそれぞれ利点があり、切断用途、切断される材料、希望の切断品質などの特定の要件に基づいて選択されます。
従来型プラズマ切断
従来のプラズマは最も一般的なプラズマ切断の種類であり、マイナスに帯電した電極とプラスに帯電したワークピースとの間にプラズマアークが発生します。
高精度プラズマ切断
高精度プラズマ切断は、従来のプラズマ切断をさらに改良したものです。より幅が狭く、より正確な切断ができるため、自動車産業や航空宇宙産業など、厳しい精度要件が求められる用途に適しています。
高品位プラズマ
高品位プラズマ切断は、最高レベルの精度が要求される用途によく使用されます。高度な技術を使用して、より狭い切り口と開先で高品質の切断を実現します。
水注入プラズマ切断
水注入プラズマ切断では、水をプラズマアークに注入して電極とノズルを冷却し、消耗部品の寿命を延ばし、ヒュームと騒音を低減します。反りやすい材質を切断する場合や、熱の影響を受ける部分を最小限に抑える必要がある場合によく使用されます。
デュアルガスプラズマ切断
デュアルガスプラズマ切断により、鋼鉄を切断する際の切断速度と品質が向上します。酸素を二次ガスとして使用して鉄金属 (鋼など) の切断を補助し、一次プラズマガス (通常は窒素または空気) がプラズマアークを生成します。
ファインプラズマ切断
ファインプラズマ切断では、小さなノズルと低出力のプラズマアークを利用して正確な切断を行います。この方法は、アートワークや小規模な金属加工などの用途で使用されます。
プラズマ切断の選択が最適である条件とは?
プラズマ切断は、多くの切断用途に優れた多用途で効果的な方法です。その適合性は、切断する材料、板厚、要求される精度、および希望する切断速度などの要因に影響されます。これらの条件と要件を評価することは、プラズマ切断が特定の切断作業に最適であるかどうかを判断するのに役立ちます。
プラズマ切断が好ましい選択肢となる条件には、次のようなものがあります。
導電性金属
プラズマ切断は、鋼鉄、ステンレス、アルミ、銅、真鍮、その他の金属などの導電性材料に対して非常に効果的です。
材質の厚さ
プラズマ切断は、薄板から厚板まで幅広い材料厚の切断に適しており、16 mm (5/8 インチ) を超える厚さの切断ではファイバーレーザーよりも優れています。
高速切断
大量生産環境や迅速な切断が必要な場合、プラズマ切断は優れた選択肢です。高速切断により、生産性が大幅に向上します。
正確かつ複雑な切断
プラズマ切断は高レベルの精度を実現し、最小限の切り口幅で複雑な切断を行うことができるため、精度と複雑な形状が要求される用途に適しています。
最小限の熱影響部 (HAZ)
材料の反りや歪みを引き起こす可能性がある熱影響部を最小限に抑えるには、熱影響部の比較的小さなプラズマ切断が有利です。特に、水注入プラズマ切断を使用することで実現します。
クリーンな切断
プラズマ切断は、ドロス(残留物)が最小限のシャープな切断が可能です。これにより、より滑らかな表面仕上げ、切断後の大規模なクリーニングや仕上げプロセスが削減され、材料の無駄が最小限に抑えられます。
万能性
プラズマ切断では、直線切断から、開先、穴、形状などの切断が可能です。さまざまな用途や材料に適応できるため、柔軟性の高い選択肢となります。
ポータブル性
ポータブルプラズマ切断システムにより、現場での切断や修理作業が可能です。ポータブル性は、建設、造船、メンテナンス、修理作業において貴重です。
自動化
プラズマ切断は CNC システムと簡単に統合でき、複雑な形状やパターンを自動で正確に切断できます。これは、大量生産やカスタマイズされたコンポーネントを必要とする業界に最適です。
高い費用対効果
他の切断方法と比較して、プラズマ切断機はコスト効率の高い切断方法です。電極やノズルなどの消耗部品は、より手頃な価格です。高い切断速度と最小限の後処理により、生産コストの削減にも役立ちます。
安全
プラズマ切断は、切断に可燃性ガスを使用せず、眼に対する損傷のリスクが少ないため、ファイバーレーザーなどの他の切断方法よりも安全であると考えられています。
環境への配慮
プラズマ切断は、他の切断方法よりも煙やヒュームの発生が少ないため、空気の質と職場の安全性に関して、より環境に優しい選択肢となります。
ファイバーレーザー切断とは?
レーザー切断は、集中光線 (またはレーザービーム) を使用して、さまざまな材料を切断、彫刻、またはマーキングする高精度で多用途の技術です。金属やプラスチックの切断から木材や陶器への複雑なデザインのエッチングまで、工業、商業、趣味の分野で幅広く使用されています。ファイバーレーザーは、過去の Co2 レーザー技術を改良したものです。
ファイバーレーザー切断の種類
ファイバーレーザー切断の種類は、出力、機能、特定の用途などのさまざまな要因に基づきます。一般的なレーザーの種類をいくつかご紹介します。
高出力ファイバーレーザー
高出力ファイバーレーザー切断機には、通常、1,000 ~ 15,000 ワット以上の出力範囲のレーザー源が搭載されています。これらの機械は、鋼鉄やアルミなどの厚い材料を高速で切断できます。
中出力ファイバーレーザー
中出力ファイバーレーザー切断機の出力は 300 ~ 1,000 ワットで、さまざまな材料や厚さに対応できます。
低出力ファイバーレーザー
低出力ファイバーレーザー切断機の出力は 300 ワット未満で、微細で精巧な切断が必要な用途に適しています。
高速ファイバーレーザー
一部のファイバーレーザー切断機は、特に薄い金属板の切断用に最適化されています。薄い金属、プラスチック、ホイルなどの材料を高速かつ高精度で切断できるように設計されています。
ファイバーレーザー切断の選択が最適である条件とは?
ファイバーレーザー切断は、いくつかの切断用途に適しています。非常に特殊な条件や状況で優れた効果を発揮します。
ファイバーレーザー切断が優れた選択肢となる条件は次のとおりです。
材料の適合性
ファイバーレーザー切断は、金属 (スチール、アルミニウム、銅)、非金属 (プラスチック、複合材)、一部の反射材など、さまざまな材料の切断に効果的です。
精度と正確性
精度が高く正確な切断が可能なファイバーレーザーは、精巧さ、厳しい精度要件、複雑な切断を必要とする用途に最適です。
速度
ファイバーレーザー切断は、薄い材料の場合、他の切断方法よりも高速に切断できます。
万能性
ファイバーレーザーは、薄いホイルから厚い板まで幅広い厚さに対応できます。材料の切断、彫刻、マーキングに十分な多用途性を備えており、1 台でさまざまな用途に対応できます。
最小限の熱影響部 (HAZ)
ファイバーレーザーの HAZ は小さいため、材料の歪みや反りのリスクが軽減されます。これは、薄い金属や精密部品などの熱に敏感な材料にとって非常に重要です。
複雑な形状
ファイバーレーザーは複雑な形状を切断できるため、カスタマイズされた部品やデザインを必要とする業界にとって貴重な選択肢となります。
自動化
ファイバーレーザー切断システムは、CNC システムと統合して、自動化され反復可能で効率的な切断プロセスを実現できます。これは大量生産に有益であり、人的エラーを最小限に抑えます。
廃材の削減
ファイバーレーザーは精度が高いので材料の無駄が最小限に抑えられ、材料コストと環境への影響を削減したい企業にとってコスト効率の高い選択肢となります。
非接触切断
ファイバーレーザー切断は材料との物理的接触を伴わないため、切断ツールの磨耗を軽減し、ツール交換の必要性を排除します。
レーザー切断ではなくプラズマ切断を選択する場合
プラズマ切断とレーザー切断のどちらを選択するかは、いくつかの要因によって異なります。プロジェクトの特定の要件、使用する材料、予算を考慮することが重要です。
プラズマ切断がファイバーレーザーよりも優れた選択肢である場合の重要な要素は次のとおりです。
金属の板厚
板厚が 16 mm (5/8 インチ) を超える場合、プラズマ切断がファイバーレーザーよりも優れています。
切断速度
特に 16 mm (5/8 インチ) を超える金属を切断する場合、プラズマはファイバーレーザーよりも速く切断します。これにより、生産性の向上、ボトルネックの減少、納期遵守の改善、キャッシュフローの増加など、ビジネス成長の可能性が高まります。
切断表面
プラズマは、板厚が 16 mm (5/8 インチ) を超える場合、一般的にファイバーレーザーよりも滑らかな表面仕上げを実現し、消耗部品一式の寿命にわたって一貫した切断面の品質を保ちます。
切断品質
プラズマは、軟鋼、ステンレス、アルミにわたりレーザーに匹敵する切断品質を実現できます。
メンテナンス
プラズマの最も重要な特性は、そのシンプルさ、堅牢性、信頼性です。メンテナンスが簡単なため、通常、社内のメンテナンス部門は最も複雑な手順以外のすべてを簡単に管理できます。高品質のプラズマ切断機を購入することで、機械の長い寿命が期待できます。ファイバーレーザーは、電源コンポーネントが少なく、古いレーザー技術よりも信頼性が高くなります。それでも、これらの機械にとってメンテナンスは非常に重要であり、専門の技術者がシステムを定期的に検査、調整、保守する必要があります。
設備投資
プラズマ切断機への初期投資は、通常、ファイバーレーザー切断システムの 2 ~ 5 分の 1 です。これは一時的なコストのように思われるかもしれませんが、会社の損益計算書に計上される減価償却費は、今後数年間にわたってファイバーレーザーシステムの総所有コスト (TCO) を大幅に増加させることになります。
消耗部品と運用コスト
切断作業の直接的な運用コストを考慮すると、より厚い金属の場合、洗練されたプロセスとガス消費量の削減により、通常プラズマの方がフィート/メートルあたりのコストが安くなります。薄い金属の場合と同様に、ファイバーレーザーの直接運用コストが低い場合でも、ファイバーレーザーシステムの電力消費量とガス消費量の要件により、プラズマ切断システムと比較してコストが高くなります。
X-Definition プラズマによる技術の進歩
Hypertherm XPR® プラズマ製品シリーズは、マシンプラズマ切断テクノロジーにおける最大の進歩です。X-Definition® 技術は、Hypertherm のプラズマの性能を大幅に向上して軟鋼での切断品質を著しく高め、ステンレスおよびアルミの様々な用途でも切断の可能性を広げています。
XPR プラズマ切断システムの利点
- X-Definition による業界最先端の切断品質
- 最適化された生産性と運用コストの低減
- 設計システムの最適化